I've been trying out a new-to-me 115v MIG welder that I got at a swap meet. It is a PowerMiG 130 (made in Italy) I am running 75% argon 25% CO2 and 0.3 mm wire.
When I can get it to feed it lays down a nice weld, but about half the time I strike an arc the wire gets stuck to the tip and stops feeding, or intermittently sticks and gives me short "bursts" of arc. When the wire gets stuck the residual compression in the wire will usually spring out of the tip after a few seconds with a little pop, but sometimes I need to remove the tip to get it free. One time tonight it even welded its self to the tip so bad I had to cut it off and replace the tip. I have tried various tensions of the feed wheel and new tips with no change in behavior.
When it is working it seems to "get in a groove" and I am able to weld several nice beads, but once it cools down I have the same issue again. 
Any suggestions would be appreciated.
In reply to bgkast:
Are you sure you don't have a kink in the wire jacket? If you disable the wire feed roller (like changing the spool), can you push the wire from the machine to the gun?
Are you using the correct sized tip?
Sounds like the HF mig. it simply doesn't put enough pressure on the plastic drive wheel to move the wire smoothly. Several people have notched the spring perch to adjust this. YMMV
0.3mm wire? Do you mean .030? (0.3mm is .011 of an inch, that's about 3 human hairs)
Anywho..... If you hold the tip too close to the metal, it sparks back and welds itself to the tip. Try holding the tip another 1/2 inch away when you start, then move in if necessary when laying a bead.
Also there's some anti-spatter stuff you can buy. Get the tip really hot by welding for a bit, then dip the tip in this can of fluid. It keeps stuff from sticking.
Dan
Sounds like it needs a new liner. The Italian MIG's use a plastic liner that pushes into fittings on each end. Don't bother looking for a replacement. Head to the nearest farm supply or welding store and buy one of the wire wound metal liners and cut it to length. It will fit right in.
That was the most major improvement to my little MIG, I also fabbed up steel copies of some of the critical plastic pieces in the drive mechanism but that was more reliability based than performance.
oldtin
UltraDork
7/31/13 8:37 a.m.
My little lincoln has those issues when there isn't enough pressure on the drive mechanism to push the wire through. It's a home depot version, so the drive mech has a bunch of plastic parts. A few bits have broken, so it's kinda hacked together. Like others said, a crappy liner will do the same thing.
Here is a comparison shot of the two liner types
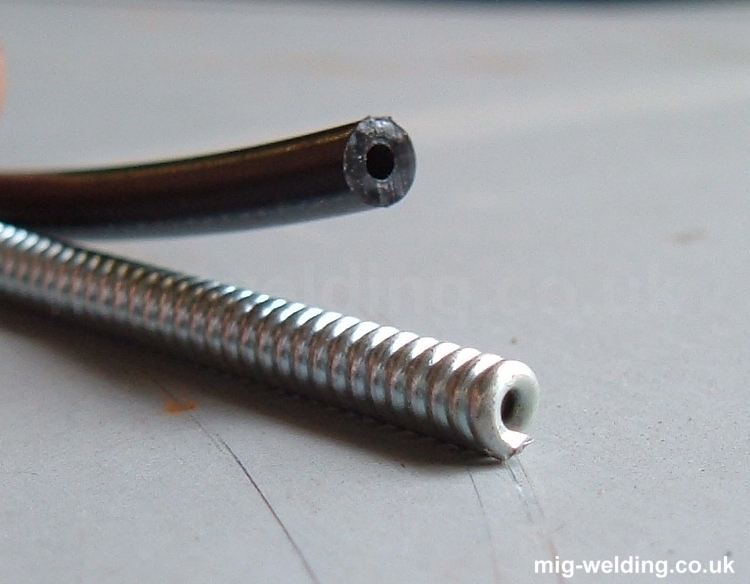
On my swap meet italian MIG the plastic liner was actually worn all the way through in a 6 inch section.
The drive mechanism on these things isn't the greatest so any drag in the liner compounds the problem. Luckily it is an under $20 fix.
Symptoms of a bad liner are
Tricky to get a smooth weld at low amps, End of wire isn't steady when welding - seems to move up and down, , Motor speed changes while welding, The wire slips between the feed wheels
I tried one of those metal liner replacements on mine (Italian HF), and it didn't work any better for me. I would up buying some teflon tubing from McMaster and used that. Had to Aggie Rig the ends a bit, but it works great now. I do have to be very careful when I change wire and have everything straight and feed it through bit hand, otherwise I run the risk of pushing the wire through the side of the teflon tubing. But other than that, it sure feeds smooth now.
Thanks for the tips. I'm actually using 0.6mm or 0.023 inch wire. I have a feeling this is the original spool that came with the welder since it is sized in metric.
I have noticed it works a bit better if I start with a lot of wire then pull in after I strike the arc. I was welding real thin stuff so I was using the lowest power setting.
I will cook for some of that compound that 914driver mentioned. I will also look into replacing the liner.
Thanks!
In reply to bgkast:
Thin wire is definitely going to get caught up in the liner/jacket easier. How thin of material are you welding?
MIGing anything thinner than 20 gauge with MIG is going to be flat out hard without the best equipment. Some of the tubes on the Exocet are 20 gauge, and it's a challenge with 0.030 wire. We plan to get a 440V power supply in our new shop to make it easier.
Not sure the exact thickness, because I cut it out of an old dumpster lid....probably around 20 gauge though.