We have a salt water pool at home. There is a control box mounted to the side of the house that manages the process. I recently realized that the system was no longer generating chlorine. With the help of the internet, I traced the issue back to a failed resistor on the circuit board (pic #1 below). It's evidently a common problem, as there are several youtbue videos on replacing the resistor. I bought one (pic #2), but the back of my circuit board (pic #3) looks unlike any of those online (lucky me).
Unlike a normal circuit board, mine has some sort of metallic plate covering both the front and rear area where the resistor goes. I tried a solder gun on it, but you can see the results.
Figuring it out is the difference between a $5 fix and a new board (~$600). Can anyone shed any light on what I should do? I would appreciate the insight!
And feel free to use small terms. I am a complete noob on soldering!

Newer lead free or low lead solder is difficult to rework/repair. You need a solder iron with more power or use a heat gun made for de-soldering.
Home depot sells a 100/140 watt solder gun that would probably work. The cheap soldering guns are problematic and tend to work OK a few times before the tip needs to be cleaned or replaced.
How many watts is your iron?
1988RedT2 wrote:
How many watts is your iron?
No clue. It looks like this, but much older and very used. 
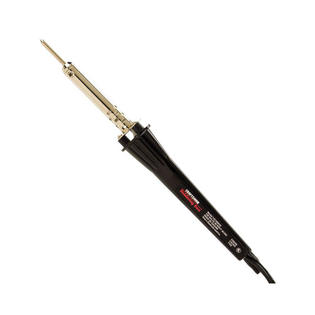
That resistor looks like a capacitor. I think you're going to need something a little more powerful. We can't tell much by looks anyway. Kind of like showing any other general hardware and asking how well it will do the job. Should be able to heat up the plating and stick a sharp pointed screw driver or other pointy device under there and start peeling that E36 M3 off. They really didn't want you to berkeley with that. It prevents you from paying them.
N Sperlo wrote:
That resistor looks like a capacitor. I think you're going to need something a little more powerful. We can't tell much by looks anyway. Kind of like showing any other general hardware and asking how well it will do the job. Should be able to heat up the plating and stick a sharp pointed screw driver or other pointy device under there and start peeling that E36 M3 off. They really didn't want you to berkeley with that. It prevents you from paying them.
I don't think you want to rip that foil off. I think with a good bit of heat, you could still de-solder it. But not with a 20-watt pencil iron.
The local pool store that's been helping me may be willing to solder it on for me. That might be the easiest route.
Rather than desoldering the old capacitor, I'd clip it off as high above the board as possible. Then 'tin' the remaining wires sticking out and the legs on the new capacitor then solder them together.
Rule No. 1 of soldering: your work piece needs to be hot enough to melt the solder. If it isn't the solder won't stick, this is known as a 'cold joint'. It not only looks bad it will fail quickly.
'Tinning is easy; have your solder ready and the iron hot. Touch the iron to the stump of wire sticking out, then touch the solder to the wire (NOT the soldering iron tip). It should melt and flow quickly, as soon as it does take the iron off. Now do the same thing to the other stump sticking out. These are now tinned. Next the capacitor legs have to be tinned also.
Cut the wires on your new capacitor down to about 1/2" long. This next is easiest if you use something to hold the soldering iron. Grip a leg of the new capacitor as close to the ceramic stuff as possible with a pair of needle nose pliers. The needle nose are essential; they will act as a heat sink and prevent damage to the capacitor. Touch the tip of the leg to the soldering iron tip, wait a second or two, then touch the solder to the leg. As soon as it melts take the 'leg' away from the soldering iron. Now do the same for the other leg.
Grip one leg with the needle noses as close to the body of the capacitor as possible. Now lay the leg side by side with the stump sticking out of the circuit board, they must touch. Now touch the soldering iron to the place where the stump touches the leg and wait for the solder to melt. As soon as it does take the soldering iron away and hold the pieces together till the solder hardens, typically 2-3 seconds. Now do the same thing to the other leg and stump.
You are done!
In spite of its appearance, it's not a capacitor. It's a thermistor.
http://www.farnell.com/datasheets/1393770.pdf
N Sperlo wrote:
They really didn't want you to berkeley with that. It prevents you from paying them.
Although I am often tempted to believe that product design frequently includes thwarting DIY repairs, I think in this case, the foils are there because of the current (up to 25 Amps) going through that particular component.
the easy way is what Curmudgeon said … leave as much of the old thermistor leads as you can … and mate the new one using the method he described …
the only thing he left out is the use of solder flux (I've always found liquid flux the easiest to use)
put a tiny amt on the leads to be tinned, then tin the solder tip (so that it's got a good coating of solder)
I usually would then wipe the tip clean and re-tin and then put the tip against the lead … then apply solder to the lead … as it flows, remove the iron
wash rinse repeat for all four leads
again doing as he said, but use a tiny amt. of flux, reheat one of the left over leads, and then hold the new lead against the old … they should fuse together (actually would be easier if you had a helper( … a third hand… to hold the solder on the joint as you heat the two leads … and allow a bit of solder to flow helping to bind the two leads together … then do the same for the other two leads
(how I made my living for the last 15 yrs .. LOL )
If you can't get the tip hot enough just by plugging it in, you can heat the tip with something else. Place it on the coil of an electric stove, put it over a flame. Old school soldering irons didn't heat up, they were placed in a flame to heat, used, and then put back on the flame. I have a 100 year old gasoline plumbers torch and irons that up until they invented those sweet plastic shower pan liners, I used to use for soldering copper pans. I've done the pin to pin solder before by heating up needle nose pliers, holding the two wires together with the hot pliers and flowing the solder in once the wires got hot. Trick to solder is to remove the heat as soon as you can or else it continues to heat up your work. Best case scenario is it takes longer for the solder to cool. Worst case is you damage what you are trying to solder.
You're going to have to preheat that board to get the solder to melt. Those are some huge pads, and most soldering irons, even my soldering station, are going to have trouble heating up that much copper.
Do you have a heat gun? Heat up that part of the board with it, then try your soldering iron. Try not to heat up the components, but the board itself.
Clipping the leads and soldering to those might be your only option if you can't get the solder to melt.
I just realized who posted this, lol. Since I'm pretty close, I can help you out. Drop me a PM if you need more hands-on help.
Curmudgeon's idea is the best, me thinks. Simple.
N Sperlo wrote:
Curmudgeon's idea is the best, me thinks. Simple.
Yes. It will be the best solution considering what equipment OP has.
Thanks folks. I took the path of least resistance and dropped if off with the repair guys at the pool store. They have a big time butane soldering set up and are confident they can get it done.
If they say nay, I've got a big gun (soldering
)
I recall once when I was working in a TV repair shop. I had a set apart with the case opened up. Dead power supply. Plugged into the wall. The owner walked up and said, "Oh, there's a thermistor that always goes bad on those." Without looking, he reached inside the set (plugged into the wall), grabbed the thermistor, twisted it so the two leads shorted together and the set sprang to life. Safety is highly over rated.