I'm building a new house and shop, and finally doing a large metal building with at least one lift. I am waffling about where to put the doors and the lift. The building will be 30'x65', and I'm planning on enclosing 15' on the right side to put in a bathroom/bed/hangout room. The current plan is two 12' doors on the front, with the 2 post lift lined up with the door on the right (to leave as much clear space in the rest of the shop as possible) and possibly a 4 post lift to come later.
I tend to be rolling non-running cars around to get them on the lift, and part of me thinks that putting one door on the end and turning the lift to align longways would be better for this. Putting the doors on the front works better for driveway layout but I do have room to put a door on the side if I need to. What say you? Notional plans below ("front" is the right side of this drawing with the doors).
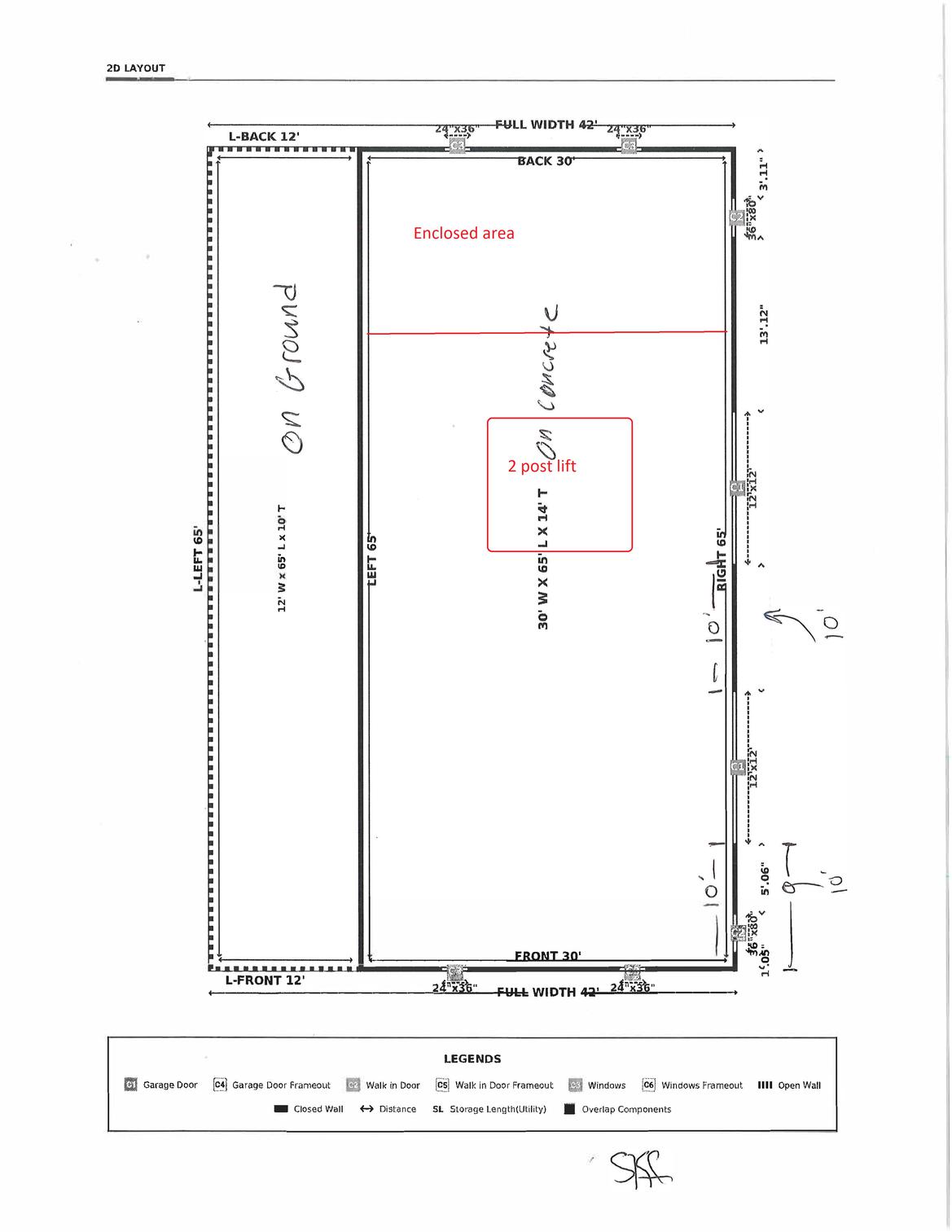
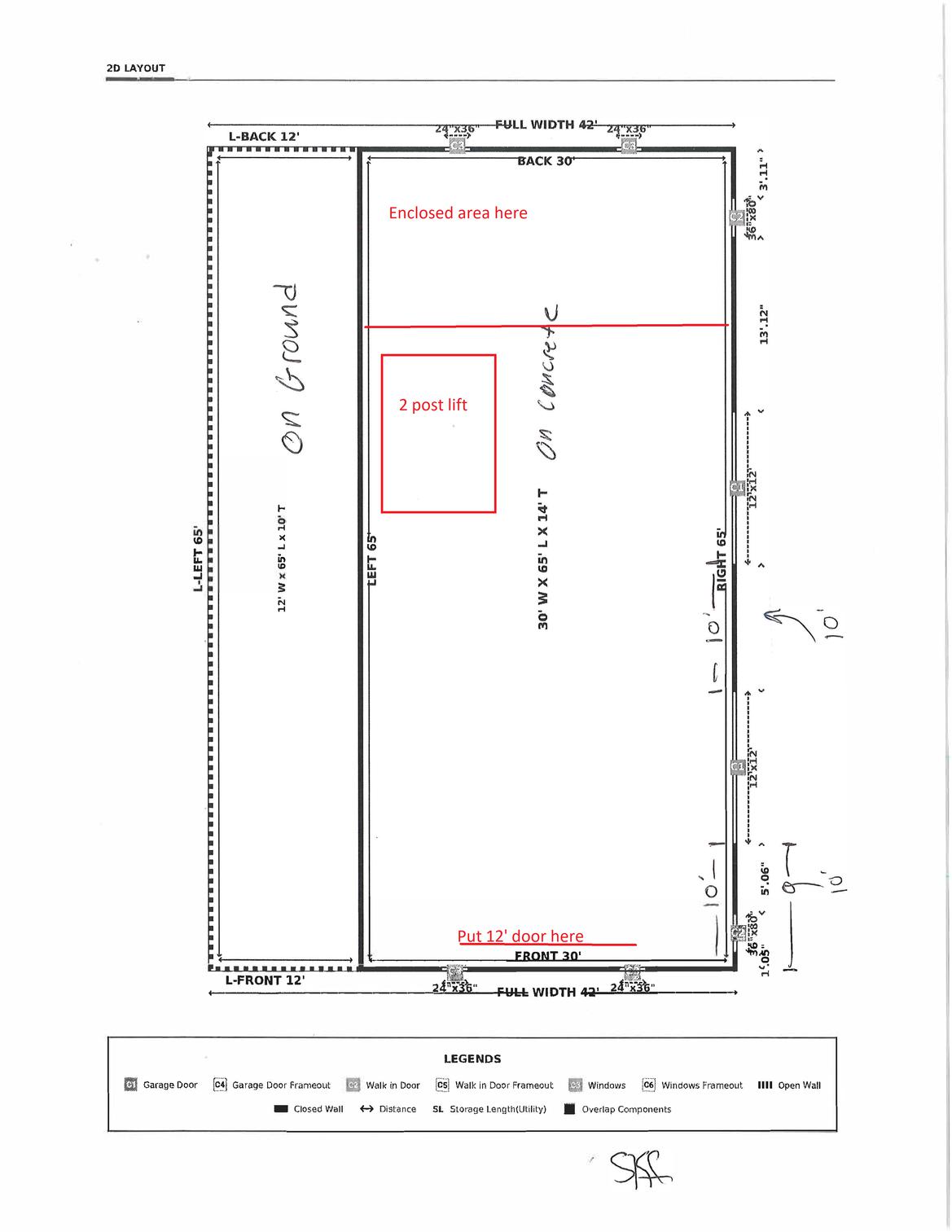
If you put it next to the wall be sure to leave enough room to get around it and work on that side of the car you lift.
I think putting it right in front of one of the smaller doors is what I would do.
My little MaxJax lift gets used way more for street cars than project or race cars, so it would seem like a big waste of space to me to have to leave a clear access from a garage door to the lift if the lift weren't lined up with and reasonably close to the door.
MiniDave, good point; I want space in front of the lift for the main tool box also.
pkingham (Forum Supporter) said:
My little MaxJax lift gets used way more for street cars than project or race cars, so it would seem like a big waste of space to me to have to leave a clear access from a garage door to the lift if the lift weren't lined up with and reasonably close to the door.
That's my buddy's take on it also; his lift (which I use often) is directly in front of the door. Problem is when you need to get an engine-less car on it, and now you have to pirouette the car 90 degrees in a tight space to get it on the lift. Wheel dollies make it possible for a single person, but not hugely fun.
I have an old boat winch bolted to the legs of my metal shop bench (which is bolted to the floor) so I can pull cars up onto my scissor lift. Of course the cars I work on only weigh about 1500 lbs (classic Minis and Sprites) so it handles them easily.
SV reX
MegaDork
8/26/22 9:03 p.m.
In reply to Kendall Frederick :
First off, start drawing to scale. Your drawings are fooling you. You don't have the lift drawn the right size.
Draw the footprint of the largest car you might have. For me, that's a full sized truck. 20' long. If your shop is 30', a truck would take up 2/3 of it. Your drawing is fooling you.
You've drawn a square in the first drawing, and a small rectangle in the 2nd. The footprint of a car is not square, and is much bigger than the rectangle you drew.
Leave 7' in front of the vehicle. That's 3' for a tool box, and 4' of working space.
The 2 post needs 11' wide, and the post should be a MINIMUM of 2' from a wall. That's tight. 3' is better.
I don't see the point in installing a lift oriented 90* to the door. It makes the rest of the shop useless. The lift needs 13' from a wall. That means your 30' shop would be a maximum of 17' with the lift in front of it. That's not enough space to park another car and still work on it. Plus, the orientation would likely encroach on 2 different garage doors making the entire space useless.
You are building a good sized shop. Keep ALL vehicles oriented the same direction- perpendicular to the entrance doors.
SV reX
MegaDork
8/26/22 9:11 p.m.
(FWIW, I have installed over 200 lifts in the last few years)
The shop I am building will have 2 bays 13' wide x 30' long. That gives me space in front of the cars to store things.
My lift will likely be the home of long term projects, so I am choosing a symmetrical lift instead of an asymmetrical one. The asymmetrical gives better access in and out, but the symmetrical one lets me back the car in and have it sit in the same spot (in relation to the building) while I work on the rear. Can't do that with an asymmetrical one. If I was looking for quick turn around and easier access to the interior, I'd choose the asymmetrical one.
Good luck!
SV reX
MegaDork
8/26/22 9:19 p.m.
One more thing...
I think you will regret 10' between the doors. That plus the 12' doors equals a 17' wide bay. That's enormous. The commercial bays I am building are less than 12' wide. It's gonna become an automatic clutter space between the cars.
You have 50' of space. That's enough for 4 bays. You are making it 2. That's instant clutter.
Move the doors to one side (with less space between them) and allow a 3rd bay with no door. The space will be much more usable.
SV reX
MegaDork
8/26/22 9:41 p.m.
I have owned a shop with 12' doors. I liked them, but I'm not sure they were an asset from a layout perspective.
10' doors are enough for a single car. The problem with 12' doors is although they are generous for 1 car, they can't EVER fit 2 cars. In my case, it was a 22' wide space with a 12' door on the middle. The 22' could have easily fit 2 cars, but the 12' door couldn't. So, the 12' door defines a space that could be used for 2 cars as an oversized space for only 1 car. Again, more clutter.
MiniDave, I like the boat winch idea. I would love a gantry crane setup in the shop to pick up and move stuff in any direction.
SV reX, some good ideas here, thanks! I drew those red rectangles in Paint in about 2 minutes to try and illustrate the general orientation and placement of the lift for this post. I know they're not to scale. :-)
I like the 12' doors and I'm going with them, but I like your suggestion about moving them closer together. I think I'll take it. I am not really planning on 4 or 5 cars in there at one time; I want some good welding and fabrication space on the other side of 2 or 3 cars.
Of course, I own 6 cars right now after "paring down" a few years ago, so maybe I'm more of a dumbass than I think. That's also why there's a lean to on the back side, I'm hedging my bets.. :-D
SV reX
MegaDork
8/27/22 5:50 a.m.
In reply to Kendall Frederick :
Even if you don't put 4 or 5 cars in there, you'll have more useful welding and fabrication space if you move those doors closer together and leave a bay with no door. With 12' doors you will have generous bays even if the doors are only 1 or 2 feet apart.
Good luck!
Totally unrelated to the lift location question. If you are building a metal building you can increase the longevity considerably by building it on top of a concrete wall 2 blocks high. It keeps the water splash from the ground off the outside and facilitates washing the floors on the inside without soaking the steel at the building base.
In reply to madmrak351 :
I put drains in the concrete, half way down each side wall, and spaced the wood interior panels 1/4" above the floor. I know galvanized tubing ain't what it used to be, but I figure it'll last the 20 years (or less) that I'll be here.
Good plan on yours. I’m red iron inside so you’re way ahead of me with the galvanized frame. This one has been up 22 years in the South Georgia climate. In 20 more years I will be lucky to still be here, much less able to still enjoy working in it.....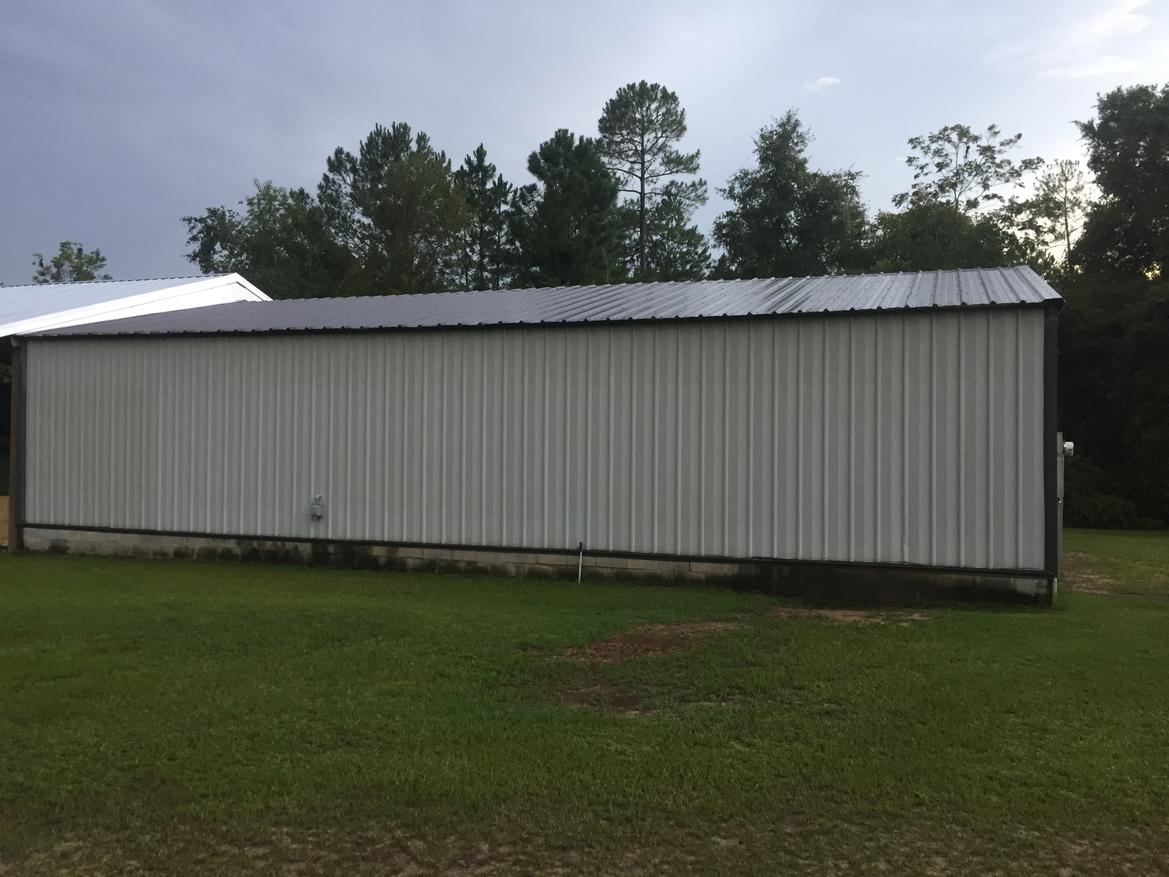
In reply to madmrak351 :
To continue off topic, my second building was gonna be 50 x 50 x 15, red iron, so the 24 x 40 "vertical carport" style framing went up at 9' walls. Then the price was falsely inflated over the weekend 35%, so...
I have a 9' tall shop to put a lift in, one day. Limits my placement to center!
madmrak351 said:
Totally unrelated to the lift location question. If you are building a metal building you can increase the longevity considerably by building it on top of a concrete wall 2 blocks high. It keeps the water splash from the ground off the outside and facilitates washing the floors on the inside without soaking the steel at the building base.
I was seriously considering this.. we are doing stem walls for the house, but it would bump the cost for the shop several thousand so I've decided on leaving it monolithic slab. We did put about 1' of fill on the site and I'll slope it off on all sides. That and gutters should help.
Thanks to the revised FEMA flood maps of 2011, my formerly non-flood-zone 10 acres became flood zone A, and now I have a big pond and 3' of fill where the house will be.. :-)
I built a shop a couple years ago with the same questions and deliberations swirling in my head for months. After much consideration, I came up with the sketch below. Every buddy/gearhead who has seen the layout likes the doors and so do I. The ease of access cannot be understated and is a major factor in the usability of the finished space. Especially for non-running projects, the ability to pull straight thru is very useful. I would hate to have to do iron ballet every time a car goes on the lift...one of my buddies has a shop layout like this and it's so not fun, he rarely uses it. Also good point from SV reX and I concur: 20 feet is a realistic length for a vehicle footprint unless you only plan to work on smaller cars. I needed space to park six, plus a 20-foot wide working bay that I could still get two vehicles in lengthwise.
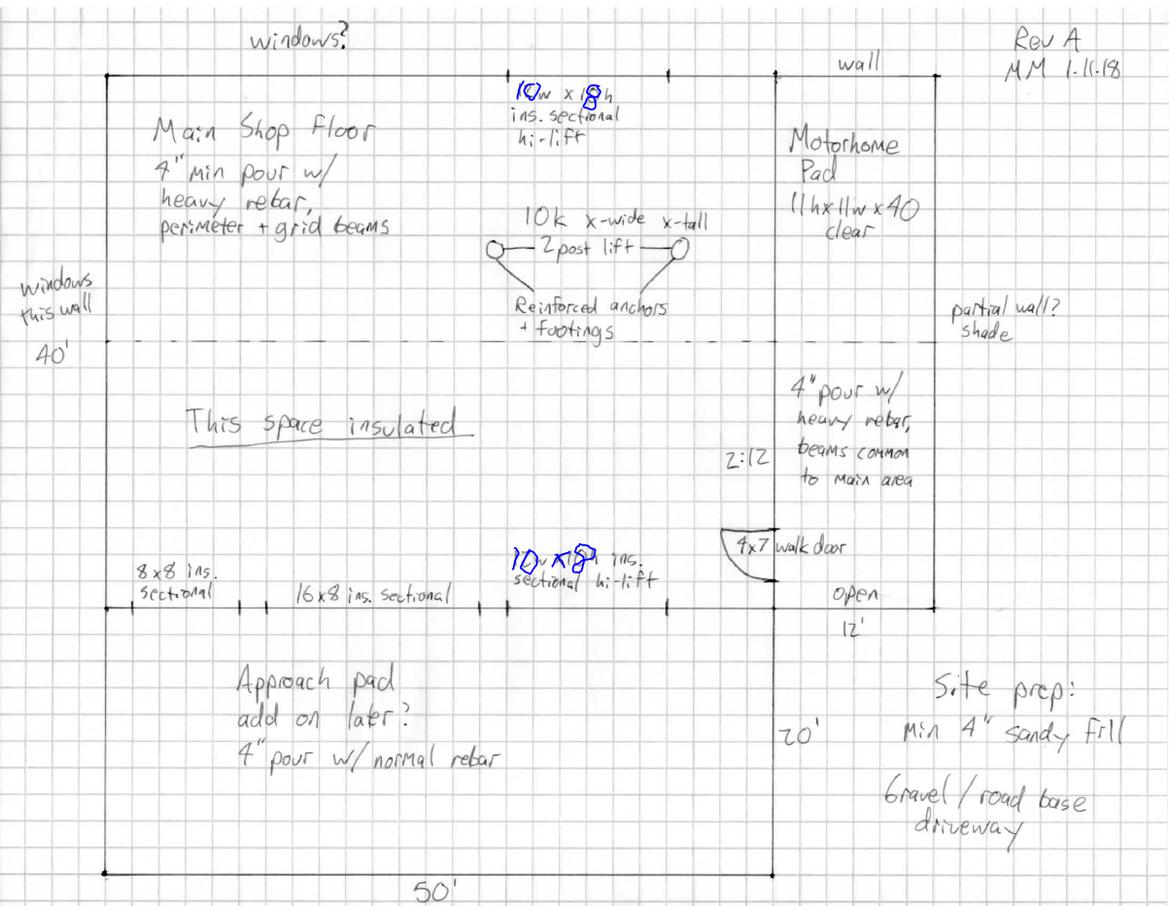
SV reX
MegaDork
9/3/22 2:38 p.m.
I had a shop with doors opposite each other like that. 40' from door to door.
Its amazing.
It's also completely useless unless you have dead car storage (that's not very visible) behind the rear door.
In this example, I'm understanding the "rear" of the shop to be along the side property line. That would make it much less useful.
SV reX
MegaDork
9/3/22 2:42 p.m.
In reply to Nockenwelle :
Is there a reason why you put an 8' door and a 10' door? Why aren't they the same?
SV reX
MegaDork
9/3/22 2:48 p.m.
Note...
Insulated doors are expensive. A medium sized door can jump from $800 to nearly $3000.
They are nice, but have a big price tag. Climate may determine whether they are worth it.
Another note...
Rebar in a garage slab is overkill. Fiber works. Bond beams are also overkill. Add control joints (not near lift posts). Also do a turn down at the edge of the approach ramp, so the slab is thicker to drive cars over.
Windows are great. I'd put them high so they let light in, but discourage theft.
All good points, gotta love the GRM crowd.
For my layout, there is 30 feet from the rear wall to property line. The intent was to be able to drive a tow vehicle straight thru while pulling a trailer or random car-shaped heap of immobile into the work area. I have had to do this maybe a dozen times since building and it's far more convenient that a come-along or winch with floor anchors. 30 feet is still enough room to maneuver a truck smaller than a crew-cab longbed.
Regarding the doors, the reason for dissimilar sizes was a balance between cost per square foot and ease of access. I didn't need more than an 8 foot door on the left, but didn't want to bang mirrors on the sides pulling into the work area on the right, and also have room to pull trailers and dualy trucks in. It would have been almost impossible to fit a second 10 foot door on the front and leave enough wall for structure without shifting everything over to the right.
Climate in north TX is generally E36 M3, and so is soil stability. Insulation was non-negotiable for me. Foundation cracks and settling are facts of life here (how ridiculous is it to have to water your foundation all summer with soaker hoses?), hence the concrete spec that's probably overkill for most parts of the country. In my case, "heavy" meant #4 instead of the standard #3, so several steps short of a seismic-rated California overpass. I vehemently dislike cracks in my floor, and to that end, elected not to do control joints either. I also had to bring in 100 yards of fill and sand to partially mitigate the soil problems and because I was not going to have my new building sitting in a puddle. It rains a lot here when it rains and drainage is crap.
SV reX
MegaDork
9/3/22 3:31 p.m.
All good points.
Standard construction method would say control joints should be no more than every 15'. Concrete cracks. Control joints are designed to address this.
In reply to Nockenwelle :
I really do like the idea of driving straight through with a project on a trailer. You have me weighing options on adding a door in back.. I have tons of room (10 acres).
SV reX
MegaDork
9/6/22 10:56 a.m.
In reply to Kendall Frederick :
If you have the space, it's a no brainer.
Not only easy to load through, but the best part is sunlight and air circulation. I used to open both ends every day, just because it was so pleasant.
SV reX
MegaDork
9/6/22 10:59 a.m.
Note that many trailers are wide enough to be tricky driving through a lift. I've done it, but my trailer used to ride up over the base plates of my lift, clearing g the posts by less than an inch.
Picking up the car directly off the trailer is probably not gonna happen. You'd have to have the stars align pretty well for the arms to miss the wheel tubs, etc. So, make sure you still consider unloading space.