So this winter, as a college graduation gift to myself, I'm having a cylinder head developed for my bike. I'll also be changing the head pipe when I get the motor back in the frame.
For the cylinder head, I got a hold of a top-notch V8 cylinder head guy who has a lot of experience with Chrysler Hemi's (Nick Smithberg, https://www.facebook.com/pages/Smithberg-Racing/224572780930205 ) and he said he was interested in working on the head as a nice break from his typical stuff.
Things are progressing very nicely with the head. Unfortunately, he had a flowbench issue when he recorded the base line on my cylinder head and forgot to re-base line it before he started making changes. I picked up a junk head for cheap thinking it was stock (had it dropped shipped) to set a new base line and just to use for experimenting purposes. Turns out it had been ported previously, but I didn't realize this until he had it in his hands. Oh well. Here are the flowbench results for the intake on the junk head:
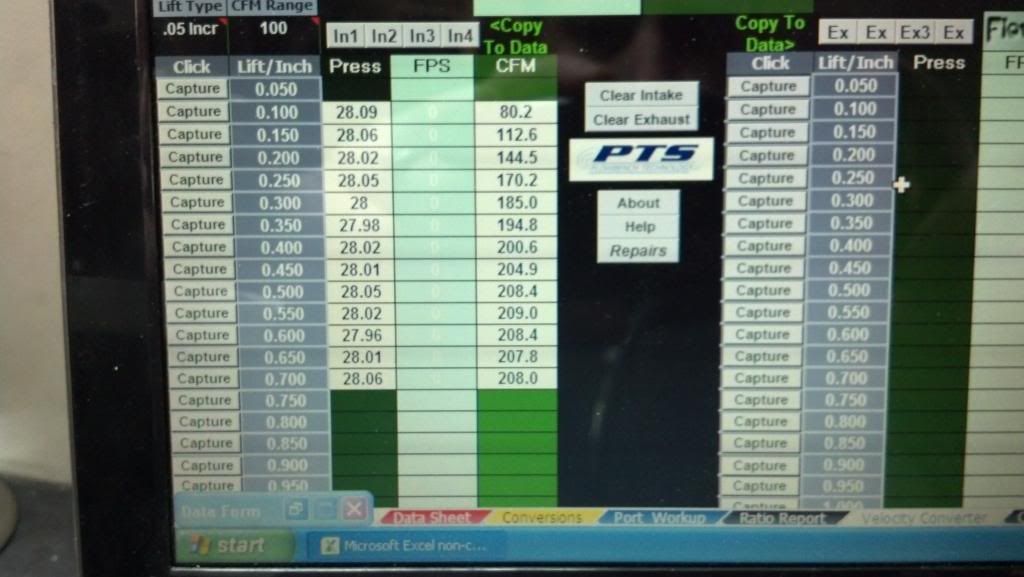
We're pretty confident a stock head flows in the 185-190cfm range based on the results of that. That jives up with other flow bench data at 28" depression.
The plan is to make the port as efficient as possible without resorting to making a huge port that is all but unrideable. The port face has been opened up to 38mm (1.50") from the just slightly bigger than stock 36mm (1.42") that my head was previously. Racers tend to open this up to 40-41mm or so. Then most of the work was focused on the short side radius as the port angle enters the head low relative to the valve seat, so it makes for a tight radius and the valve seat / profile.
Here is the finished chamber and valves. The head has since been blasted and decked to get the combustion chamber volume where we need it.
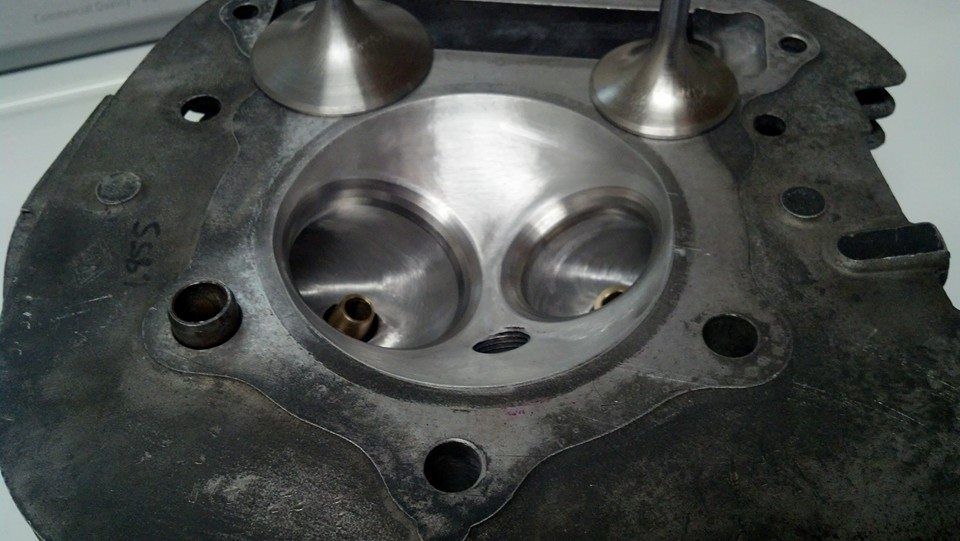
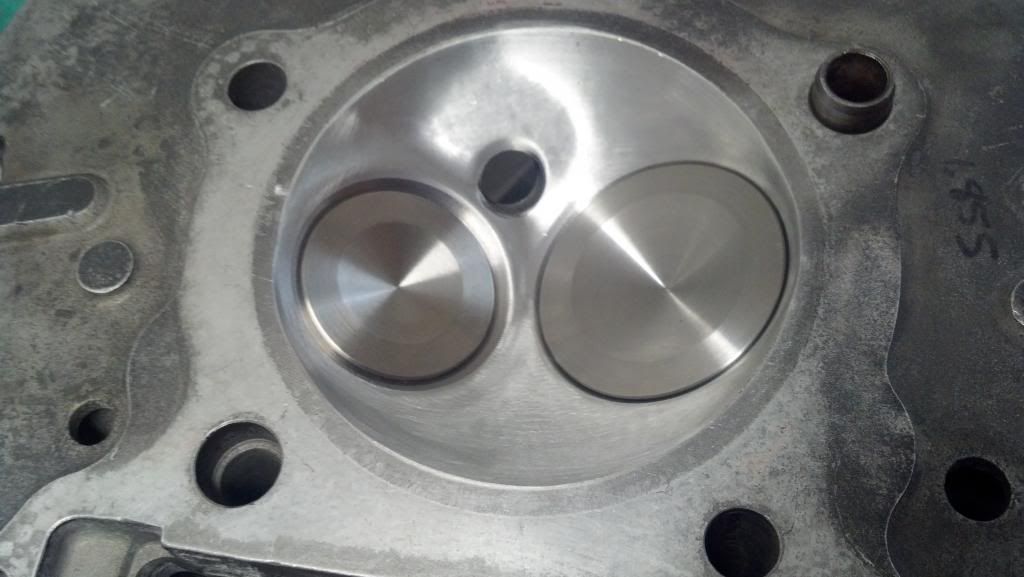
a photo of the intake port:
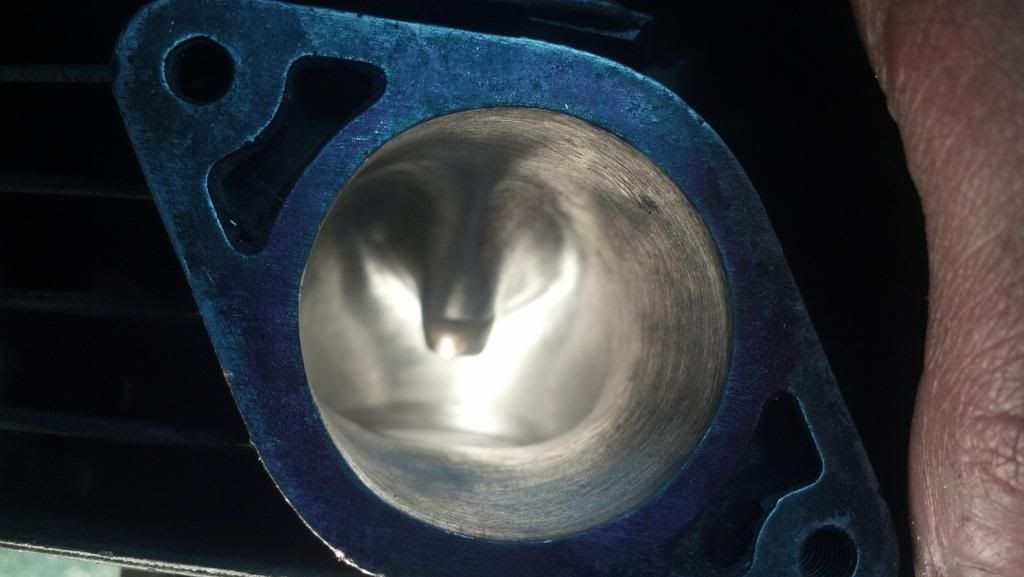
Valve retainers to fit the 7mm valves:
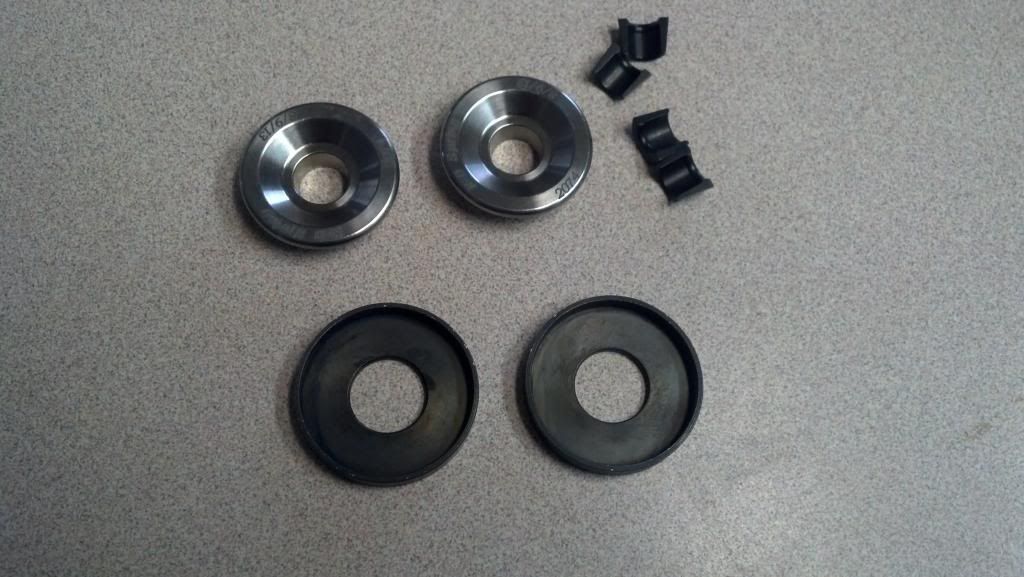
So as you can see above, we flow tested the Mikuni VM-36 (36 mm venturi) with a more traditional style velocity stack.
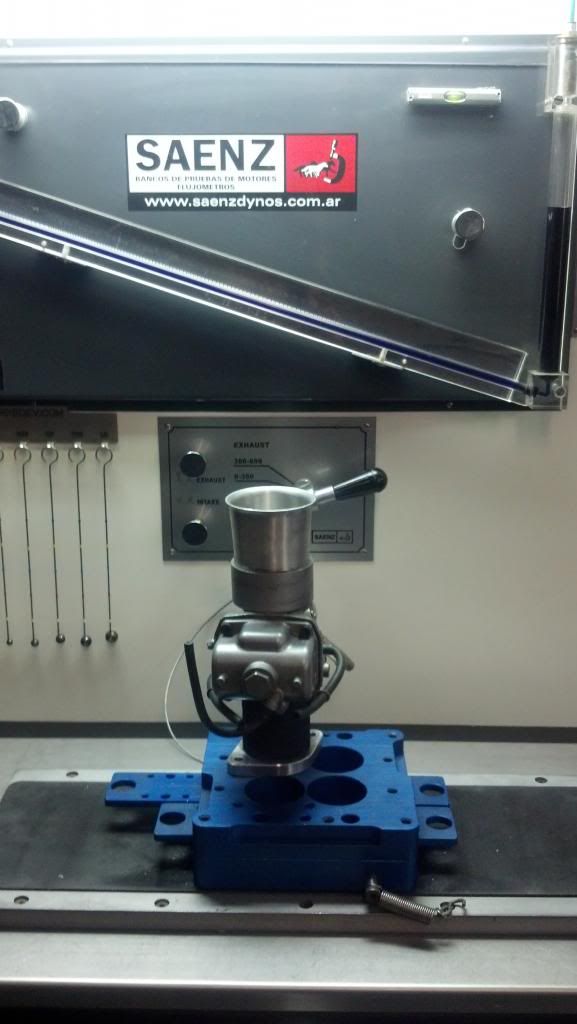
and the flow numbers at WOT
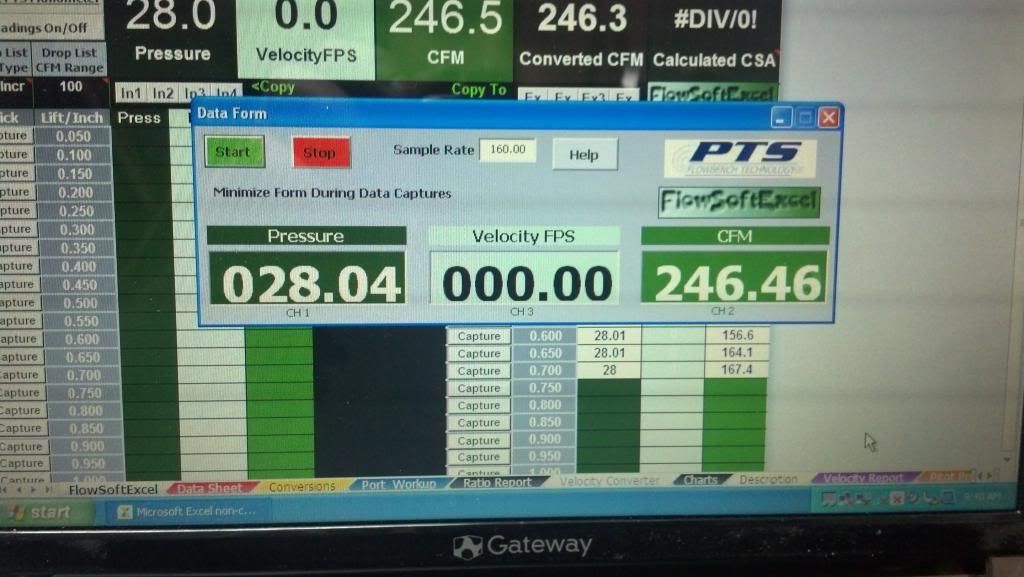
After that test and testing the combination on the head (was losing almost 30cfm at .600" lift), I decided to pick up a Mikuni TM-38 flatslide (38mm venturi), which works out to be an increase of 11% in area. Now the venturi matches the spigot and the port entrance diameter.
Here is the TM-38 attached to the spigot and being flowed:
and flowbench figures:
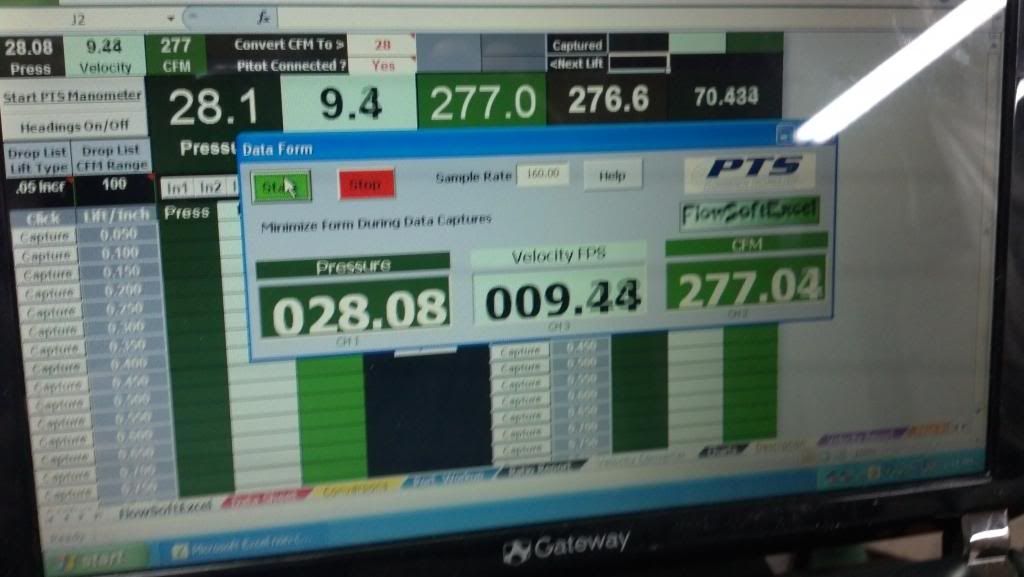
So a 11% more area and 12% more flow, and that's without a velocity stack of any sort.
Here are the final flow numbers with the spigot attached (but without the carburetor):
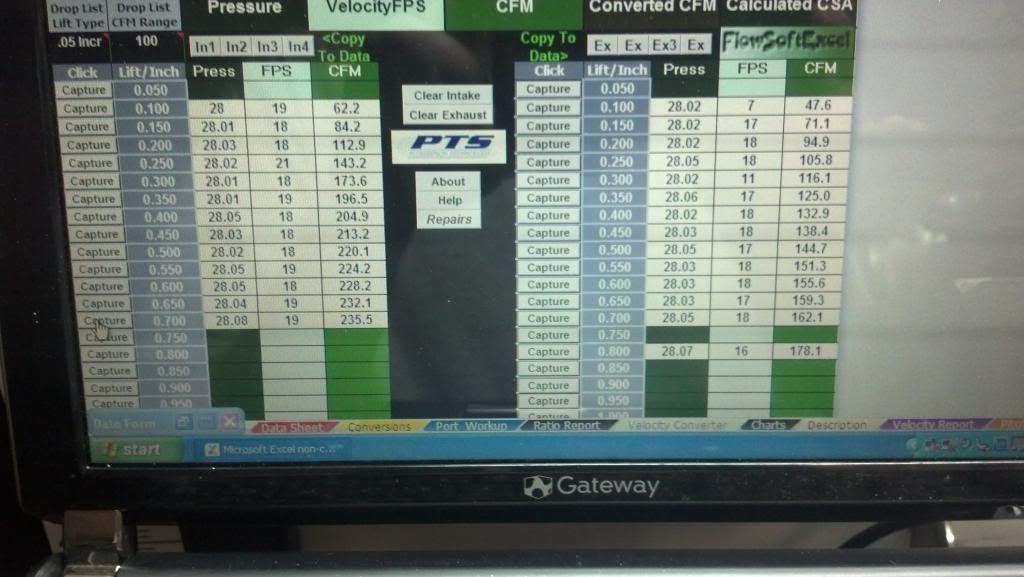
Went up from a 1.85" valve to a 1.90". The port actually lost about 1.5% of flow by doing so, but made the port VERY stable on the bench. I'll take some flow if it means a smoother and more stable port.... especially when you start thinking about the kind of depression is actually occurring in the engine.. If the port is starting to break up at 28" H20, it'll be a mess at 3x that.
The right side is the exhaust. Those numbers are without a pipe. The .800" number is .700 valve lift but with a pipe. Was just really looking for the port to sound clean, which it did.
Keep in mind, this isn't what I would call a 'race' port. The goal with this was port efficiency and port stability. This is a nicely sized port with very good velocity. To take this further, we would go with a larger carburetor (40-41mm) which is where the port face would open up to. The intake valve size would be reworked a bit and the port just touched up to get it working better with everything sized differently.
Going forward, I'm looking to possibly get JE or Arias to update their dated piston designs. Something a little lighter and something with the top ring moved up to the .200" range to minimize crevice volume.
In the future, I'd like to ditch the pod filter and build an airbox with a flat panel filter underneath. This will help with some flow losses that are inherit to the individual pod filter design.
Here is the velocity stack I had made up for the TM-38:
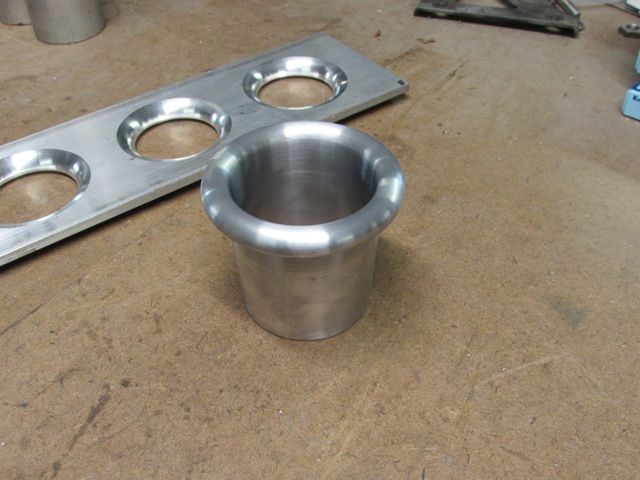
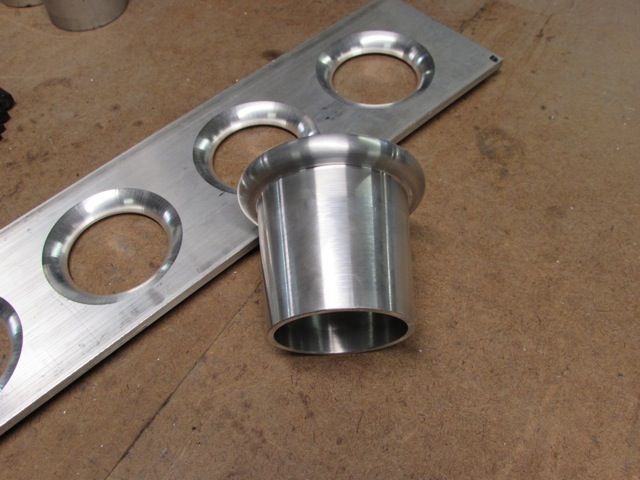
Besides flow, it also aids in the effort to get the intake tract length where it needs to be.
I'm going to change up the head pipe slightly. I'm going to change the step length and shorten the primary as well.
Lastly would be camshaft development. We'd give back some of the low lift flow we too away and probably take 15-20* of seat to seat duration out of the camshaft.