Can't find any of my manufacturing process pictures unfortunately, but here's some more info
We had two main layup processes, a two-stage process for the larger elements, and a single stage process for the flaps.
For the two stage, we'd layup the leading edge after laying up the main surfaces. This allowed us to use a thicker (stiffer) mylar sheet on the first stage surface layup to avoid the ridges you see below. After that cured, we'd layup the leading edge strip in a second layup, with a thin sheet of mylar conformed to the profile. Having this done separately allows you to tape the mylar to the wing surface, so that it doesn't move when you bag it. The leading edge was done as the second stage as the tape would press into the foam core under vacuum without the carbon skin.
For the single stage, we'd just layup the entire wing with the thin mylar. It was a lot easier to avoid the ridges with the shorter chord length.
We settled on a two-ply layup for all of our wings, but never really did any testing to validate that. 1 ply was too weak and 3 ply seemed unnecessarily heavy. We'd use a plain weave for the inner skin and a "Spread-Tow" for the outer skin. The idea here is that the spread tow would better distribute the aero loads across the surface and that the plain weave would better handle the local loads. Really though, the spread-tow just looked cool, but we didn't have enough material donated to use it for both plies. We would, however, apply reinforcement patches at the mounting points. We would add a 2 ply patch about 1-1.5' oversized around the mounts.
Here's a picture of a front wing flap made with the single stage process so you can see the kind of surface finish you can get. The edges didn't have mylar as the span for the FW flaps is short.
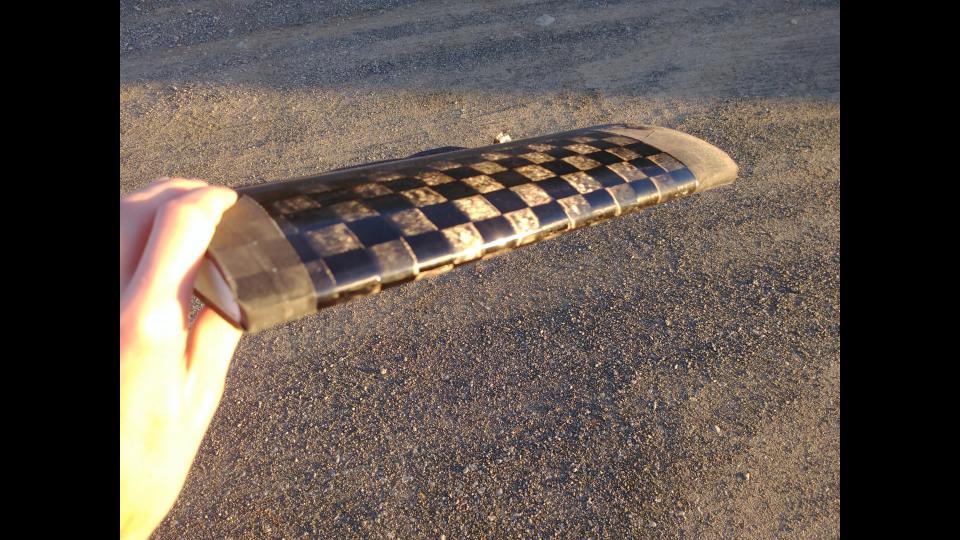
Here's one of the full rear wing assembly. This was made during the year we didn't have the thin mylar, so the leading edges weren't as nice. We ended up sanding them down and taping over them.
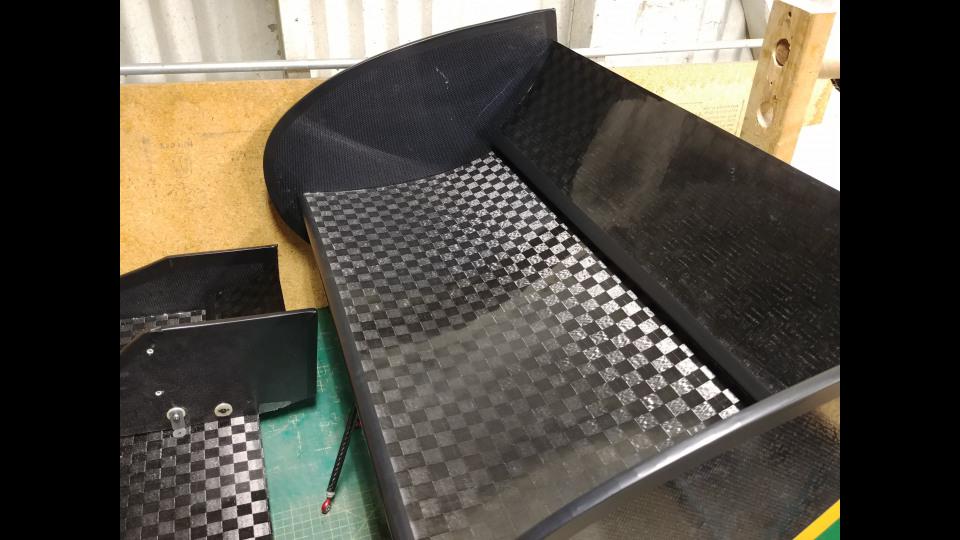
Here's a picture of the ridges when trying to use the single stage layup for the mains.
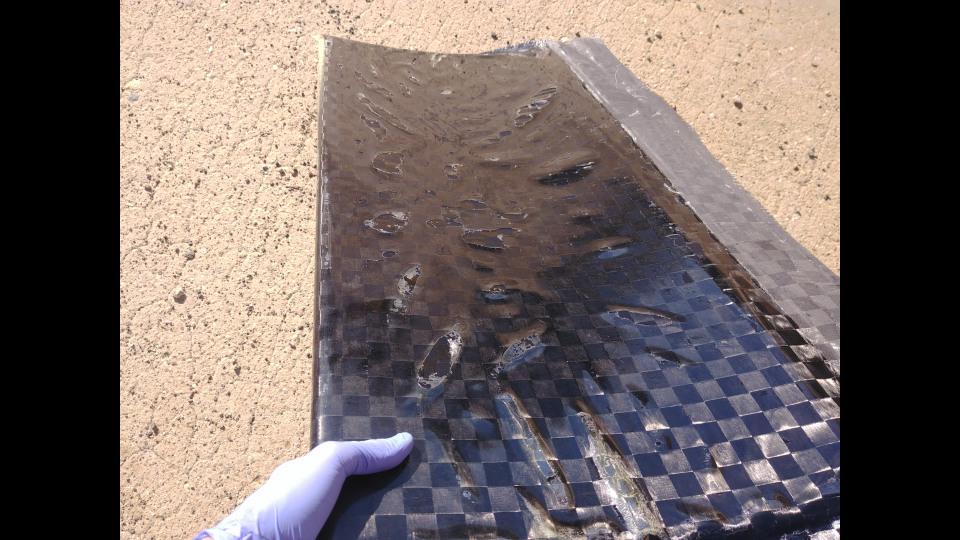
Couple more notes. You shouldn't need to apply a release coat to the mylar, but it's good practice and is good insurance to prevent it from sticking to the carbon. We usually used Frekote, but there are many options. You'd want that wrapped in teflon sheets or some other release layer, and that wrapped in breather, before placing the wing in the bag.
The mylar is kinda finnicky to work with, but you can get great results. Let me know if you want any more details, happy to add