I still feel good about my math. Alright, we got a bunch of springs, including an ebay kit I bought only for the perches because it was so cheap.
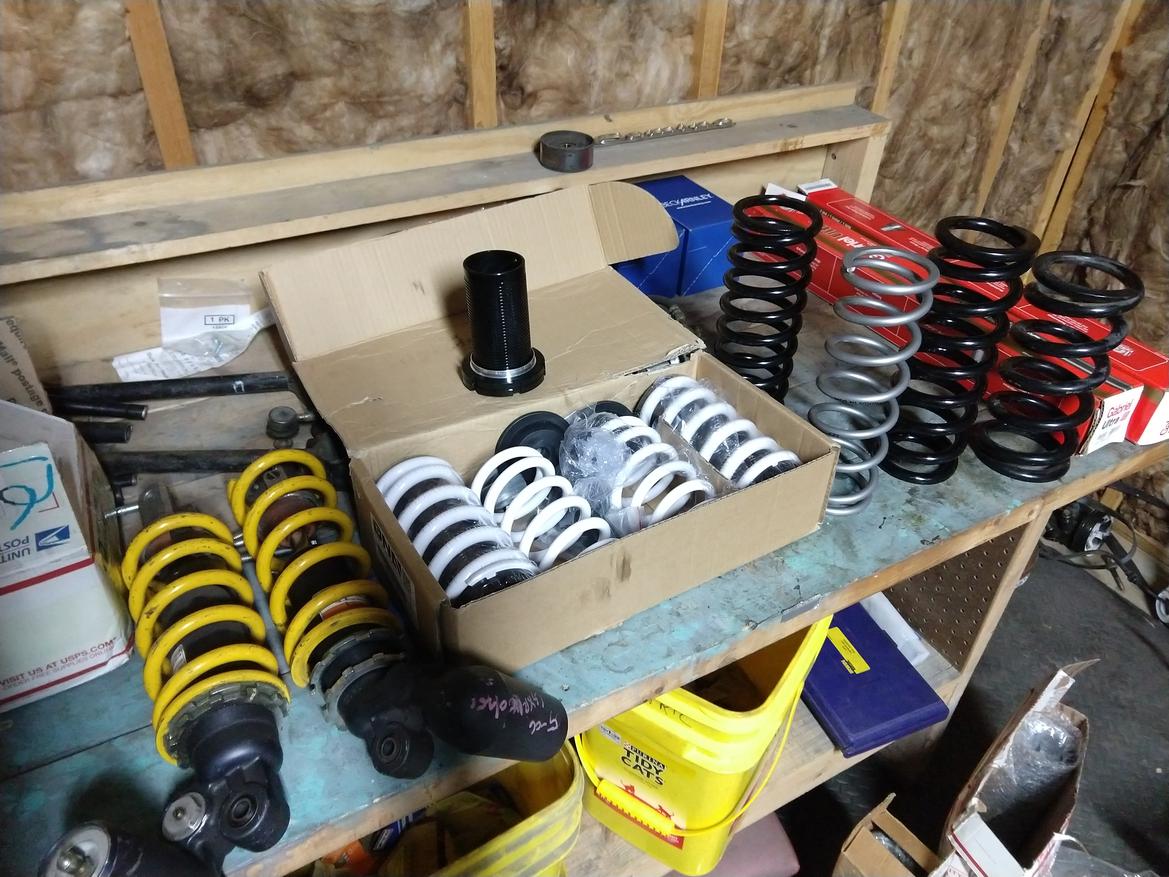
Turns out those fleabay perches don't actually fit a real 2.5" ID spring, so I helped them.
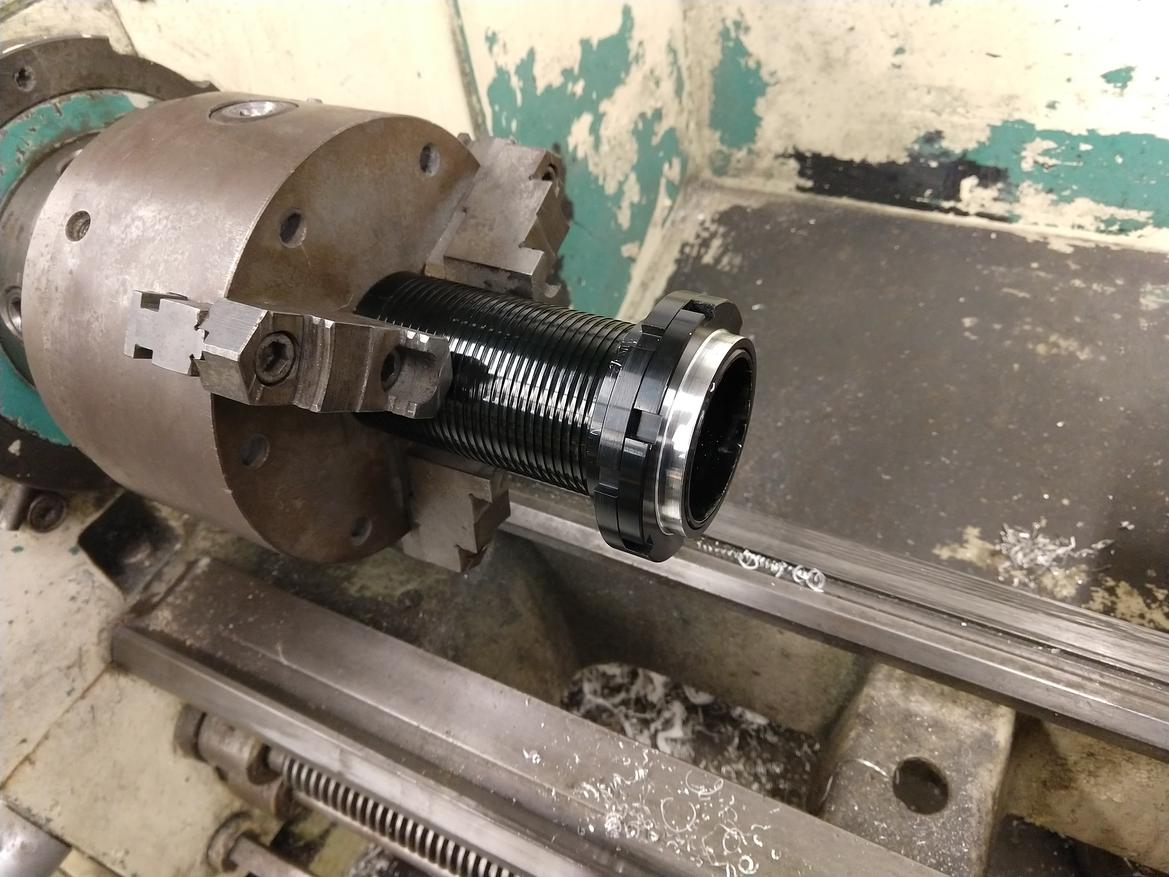
Starting cutting up more parts for the upper perch so I can reuse the Avalon's strut bearing.
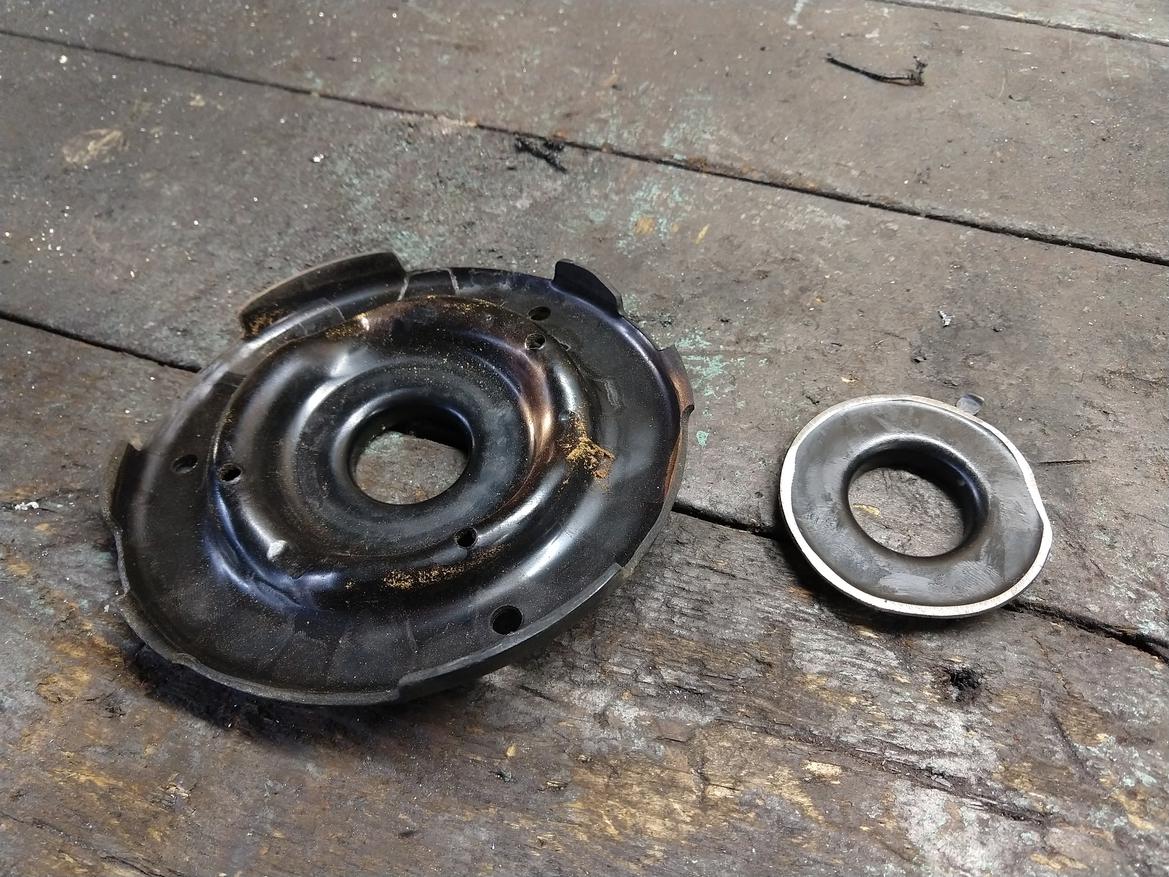
...and it's just not going to work. I did a lot more careful measuring of the Lotus body. There is simply not enough room for a McPherson strut, even if they were 2" shorter than I've already made them. There is a flat fiberglass panel that connects the outside skin to the inner shell that would have to get cut. That's not a big deal, except then you have zero access to the strut hat for installation. I invested a lot of work into the struts, but I'm glad I know for sure now.
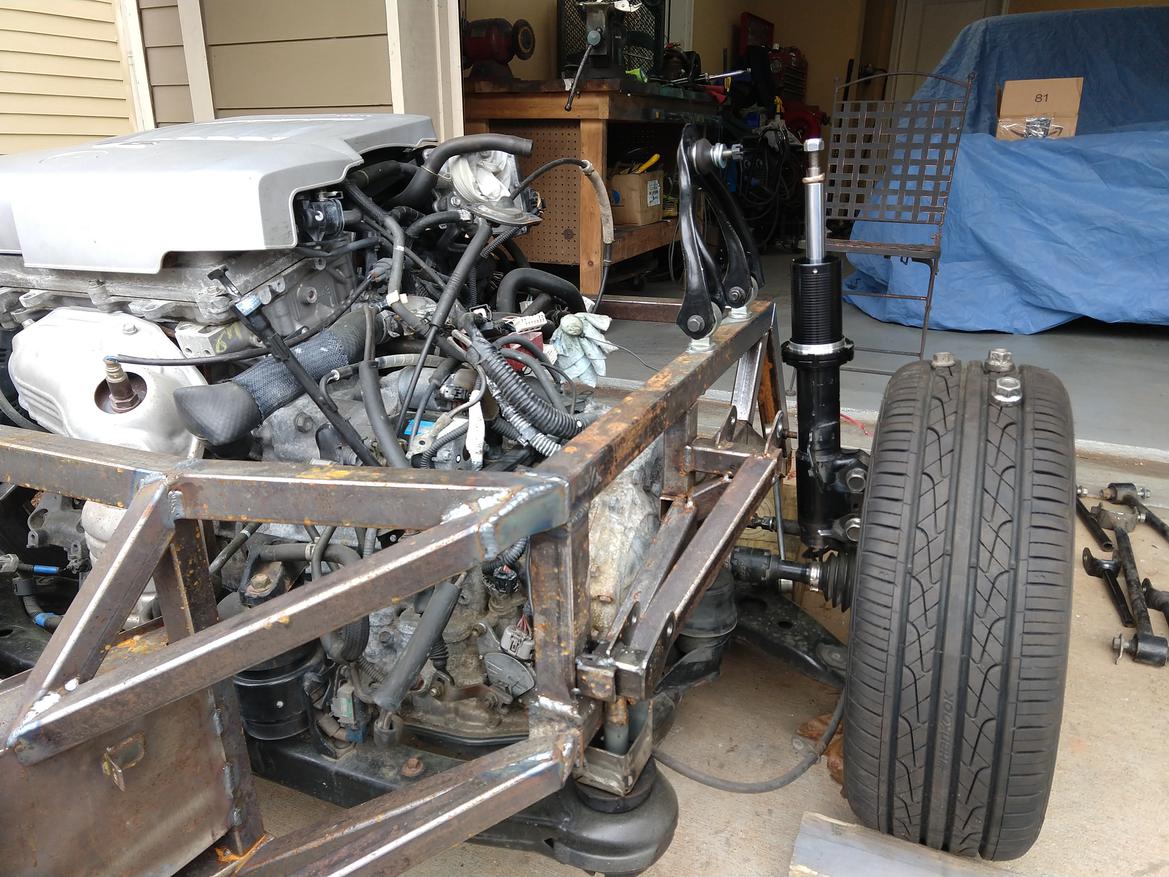
It's been a bummer of week trying to figure this out. So I went back to crux of the problem - can't put the coilover mount in the right spot, because there's enough droop allowed by the Honda UCA ball joint. I was so stuck on adding preload, or a stiffer spring. My math says if I could just move the coilover mount closer to the rocker, by having a lower droop point, I'd be good.
So let's test that. I ripped out the Honda control arm and made a dogbone from the ends of more Toyota Avalon rear suspension links. I just tacked them on the frame and the Holy Bracket. This actually puts $40 back in the budget.
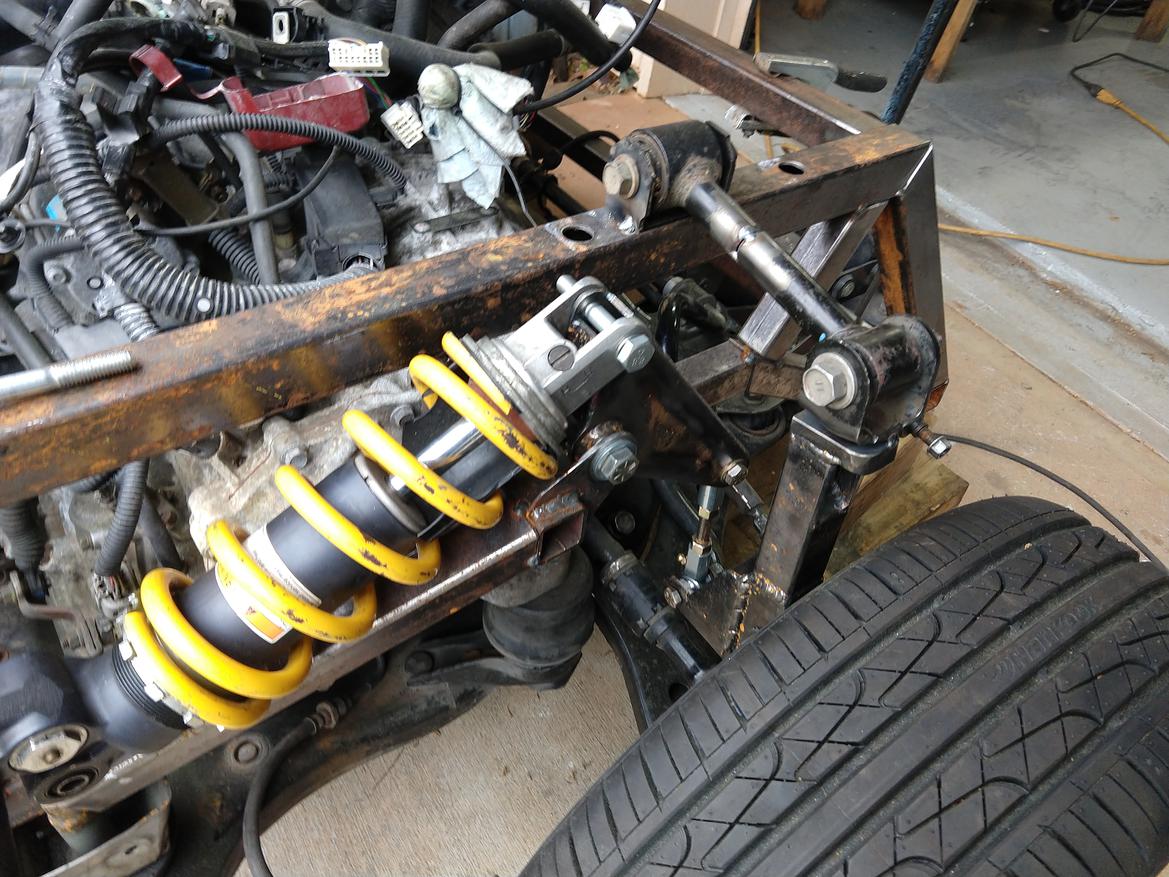
Without the shock, I tested the range of motion. Basically unlimited until the rocker goes vertical. And then tacked the coilover mount just about 1/2-1" further rearward than I previously could. And put the coilover in. And added weight...and...
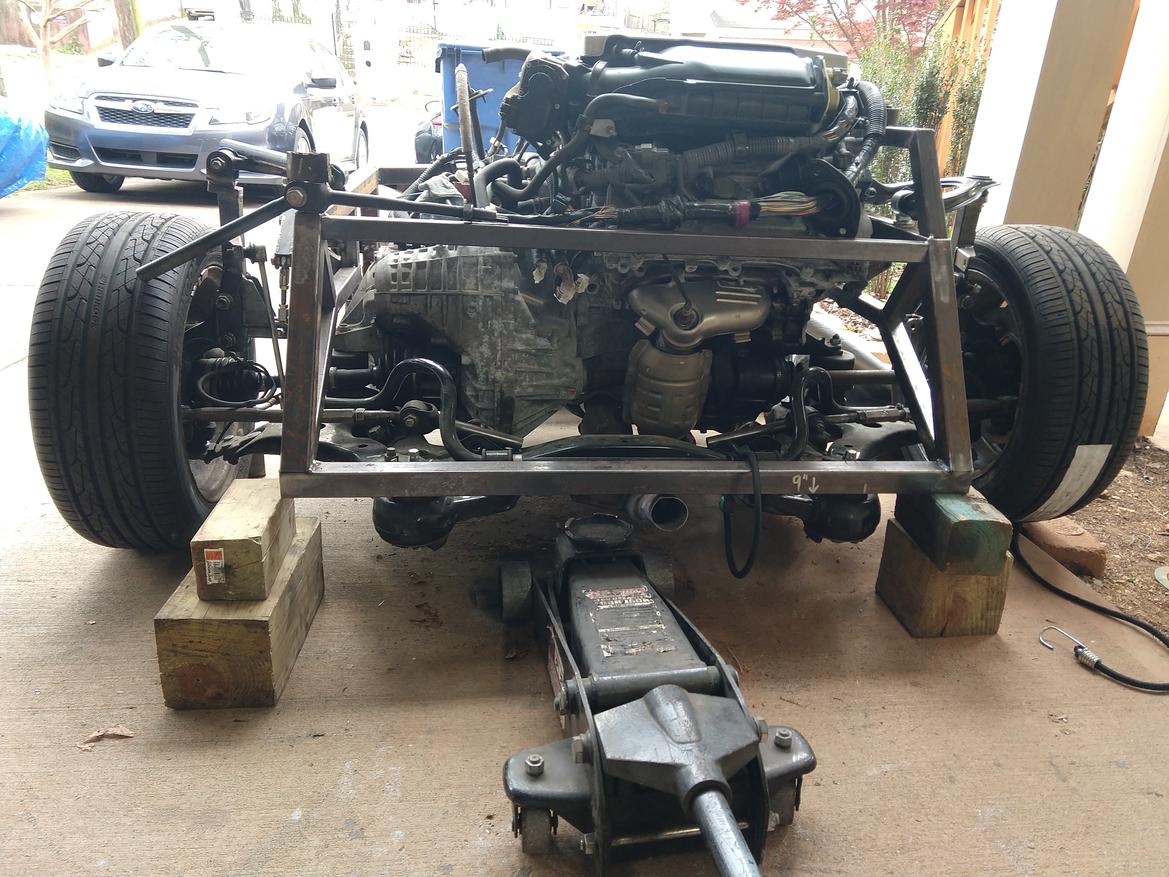
It's damn near perfect! The right side is supported at target ride height with the 2 blocks. Left side is sprung. It's almost 1" too high, which is good because there's more weight to add. This is also max preload, so I can come down more. The jump-up-and-down test feels way better than before. Not racecar stiff, just sports car firm. And that's uhh without shock damping...more on that soon.
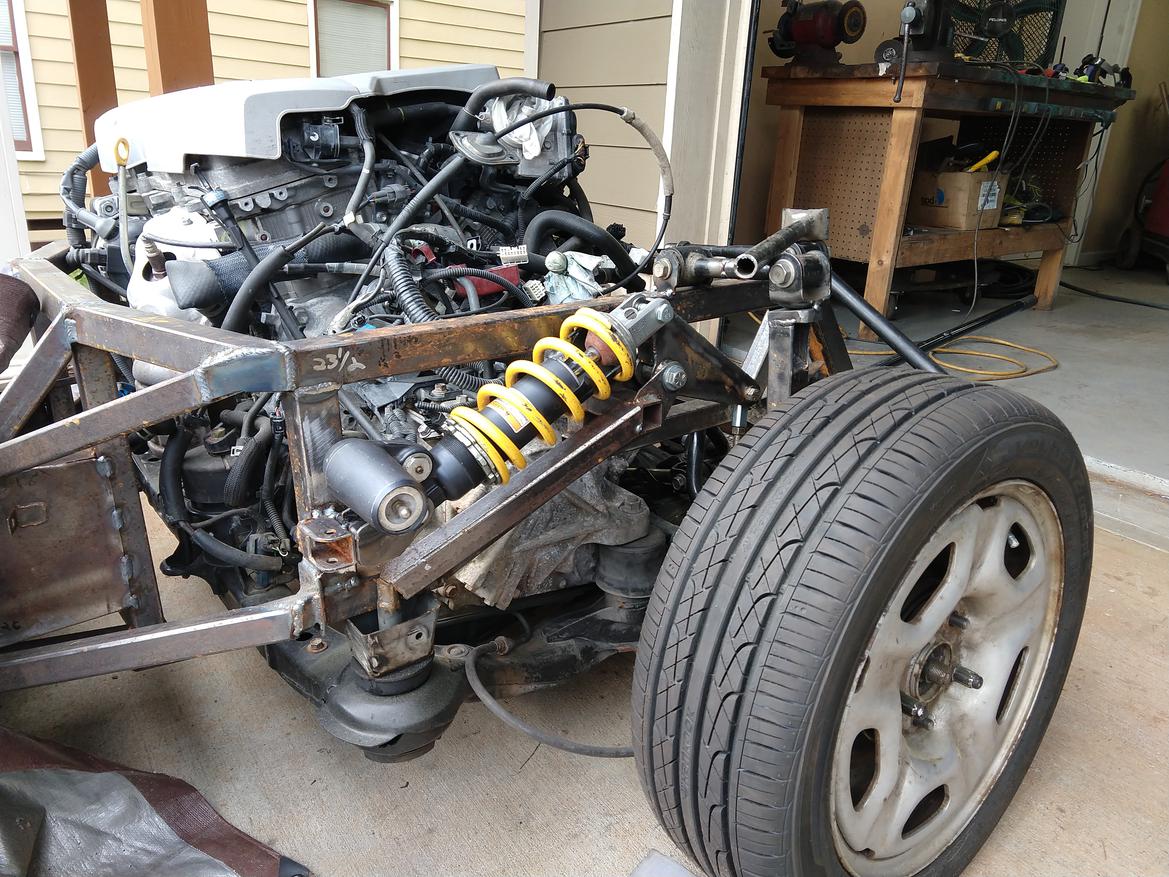
Of course the test dogbone is not enough for the wheel torque, so it will evolve into a proper triangulated UCA. Of course using recycled Avalon toe links.
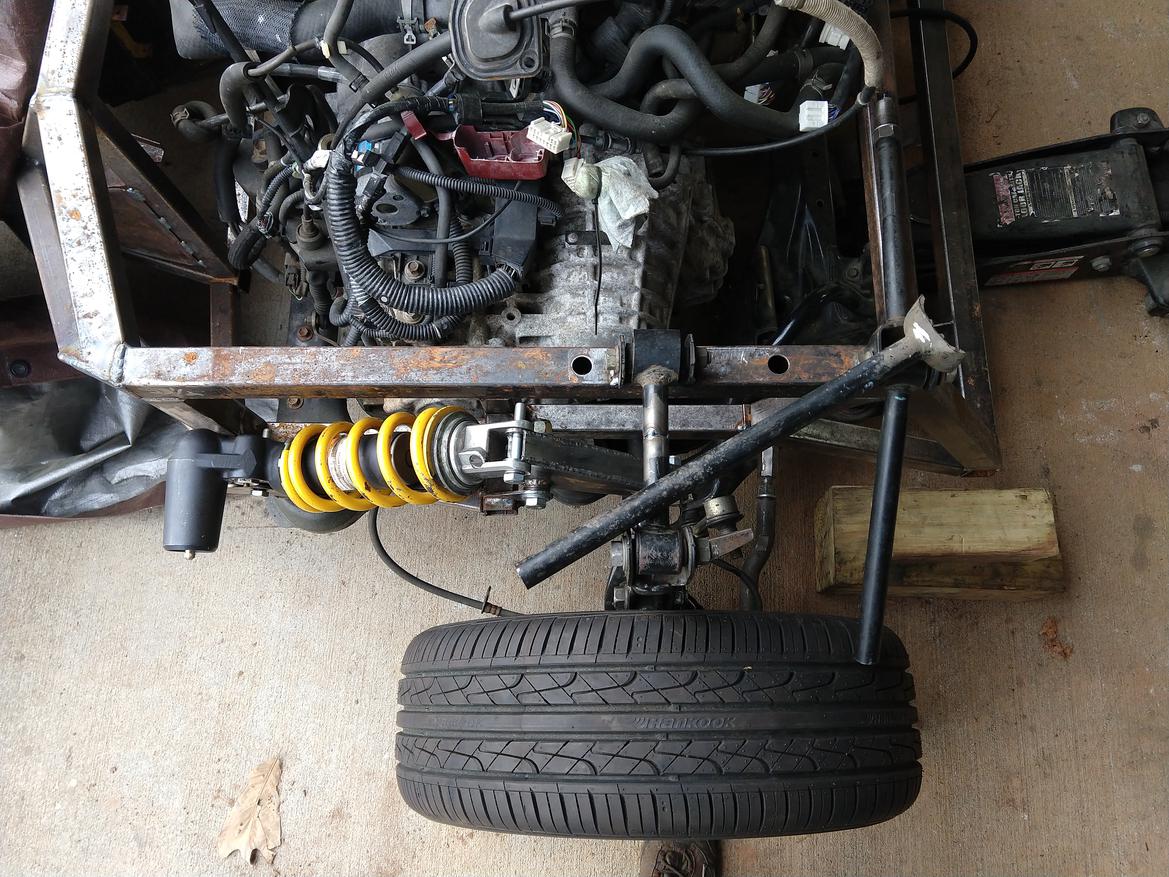
So that's all great. But why is the shock not damping? In a stupor of exploratory frustration, I accidentally over-loosened the damping adjuster and all the oil poured out. I tried to refill with fork oil, but now it's jammed closed and I can't retract it. I don't know what happened but it's definitely berkeleyed. Luckily these are ubiquitous on ebay, so I can just replace.
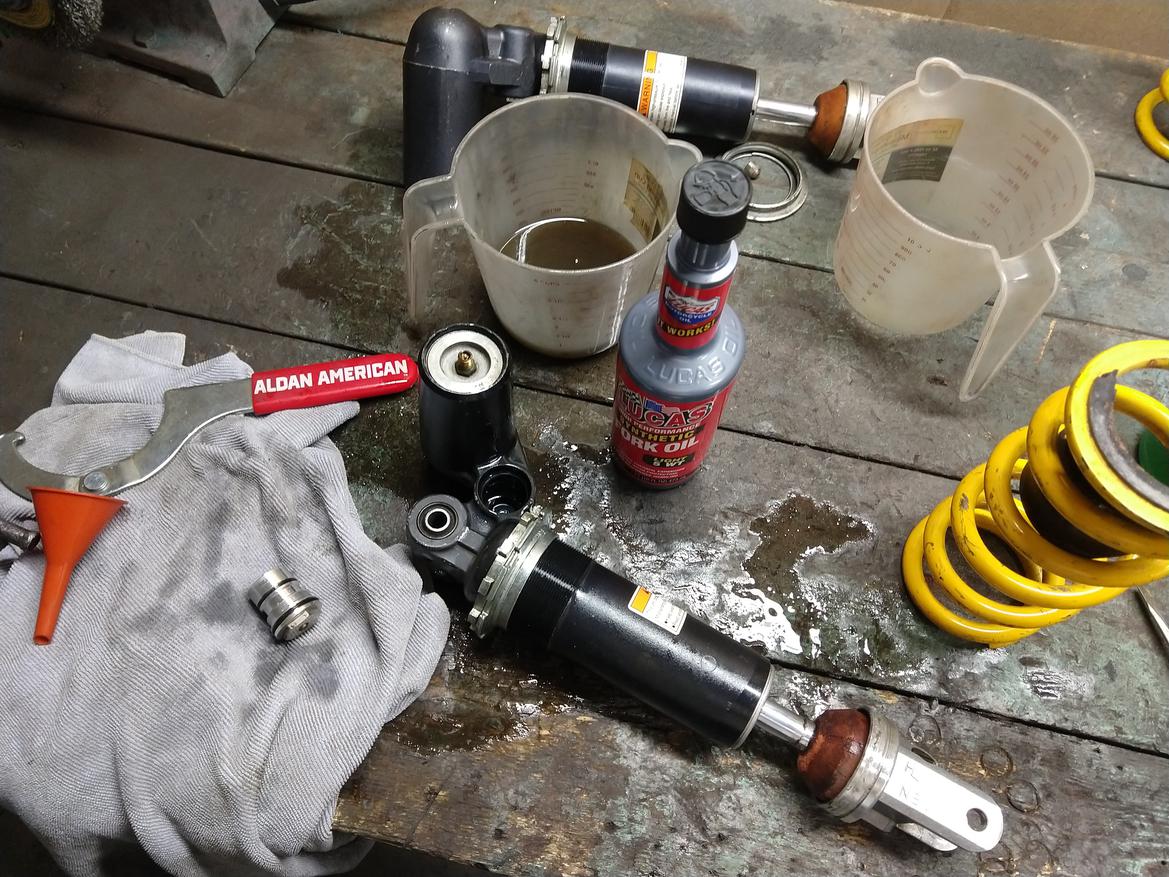
So that's not a lot of actual progress. In fact I think I went backwards, from a functional parts perspective. But I finally have a clear path forward. I was obsessing about this problem for so long. I was researching pretty far out there for alternatives, including high-dollar actual car coilovers and even torsion bars... Now I just have to execute.