(7-25-2020)
So, ever have one of those days that seem to go really well, and lots of things get accomplished and then SURPRISE! I hate those days...
It was a bit hot today, but with the help of a portable AC unit, the garage was pretty livable. I spent quite a bit of time out there today, and got a lot done.
A few "episodes" ago I mounted up the intercooler. Today I started on the plumbing. I bought a generic "intercooler piping kit" from Amazon. It has a selection of alum tubes, alum elbows, silicone connectors both straight and elbows, and a number of T-bolt clamps to put it all together. Because of the size of the turbo outlet, and the throttle body I needed to order silicone "reducing elbows" to adapt to the 2 1/2" piping that came with the kit, but I have all that now, so thought I'd get to it.
The intercooler is mounted in front of the radiator, so I needed to cut a couple holes in the shrouding in front of the radiator. A "sheet rock" bit in a dremel made short work of that (though it did add a little clean up time...). I'm not done with everything on the drivers/intake side of the motor, so without the intake manifold mounted I couldn't do anything over there, but I did get everything finished on the passenger/turbo side. Worked out pretty well! I'm hoping to find someone that can weld a pair of the alum pipes together to eliminate one of the joints if possible, but otherwise I'm happy with how that worked out.
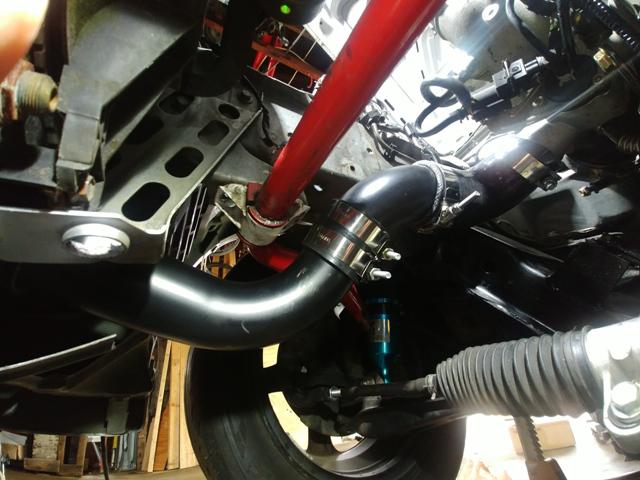
With that done I moved onto the steering. If you remember I'm adapting a steering rack from a Saturn Vue. I'm doing this because the OEM steering rack was going to have to be lowered to fit the motor in place. Doing that would have added quite a bit of pump steer, and I wanted to avoid that. I was already planning to use the electric power steering out of the Vue so I wouldn't have to adapt the Miata power steering pump to the EcoBoost motor, so while I was at it I bought the rack too.
So, I mounted the rack several posts back. Recently, with the help of one of our club members we came up with an adapting solution to get the Miata outer tie rod ends onto the Vue inner tie rods. That worked out fantastic (thanks again)! Today I worked on connecting the Miata steering shaft to the Vue rack.
The Miata steering shaft and rack both have a splined shaft. The Vue has a "double D" shaft. This is effectively a round shaft with 2 flats ground into opposite sides. Simple and effective, and as you'll see later, easy to "adjust". Neither the Miata, nor the Vue U-joint were going to be easy to adapt to merry these 2 parts together, so I sourced a new U-joint from, where else, Amazon! It would plug right into the rack, and I'd have to adapt to the steering shaft. With the location of the rack and the steering shaft I test fit the new U-joint. It slipped onto the rack just like it should, and the other end stopped right about at the steering shaft. this should be pretty easy to just cut the Miata U-joint, and weld on the part with the correct spline!
So with the dissected "part of a U-joint" I test fit everything. It's a little tight. I need about 3/4" more room between the 2 shafts to be able to get everything in place.
So, I fired up my angle grinder and "extended" the 2 flats on the steering rack input shaft! that worked great, but the shaft hit the inner workings of the U-joint before I got enough room. So, I fired up the cut off wheel equipped angle grinder (I have 5 angle grinders so I don't have to swap attachments, I just grab the one with the right parts...).
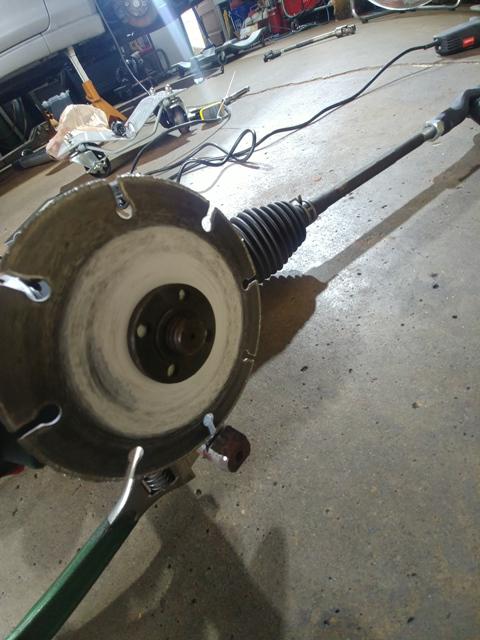
With THAT done it was just a matter of getting the parts lined up correctly and welding them together. After a tack weld, test fit, partial weld, test fit, final weld "test fit", TADA, everything fit!
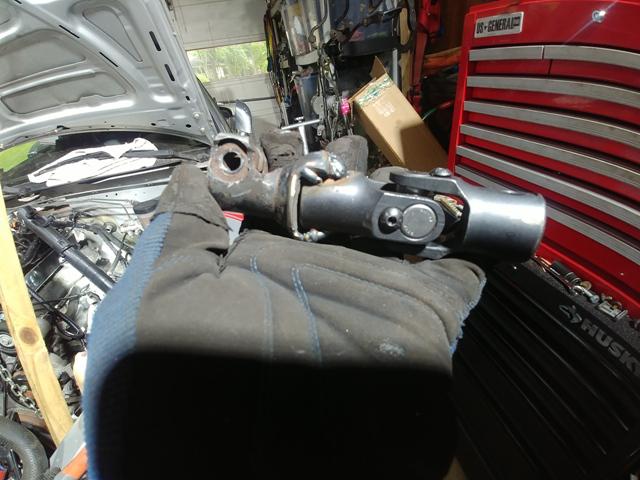
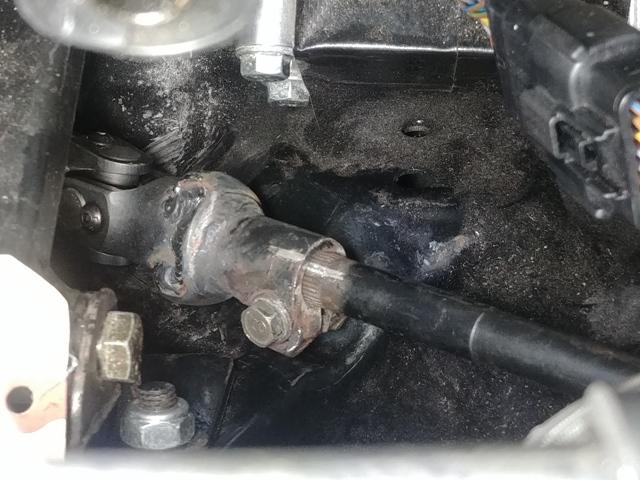
Once everything was installed and tightened up I checked one last time that everything moved freely. I had the right wheel pointed off to the right to be able to tighten the outer tie rod, so I spun the wheel left. the new rack has a little more travel than the OEM Miata rack, and has about 3 1/2 turn lock to lock, so I expected it to turn 2 to 2 1/2 revolutions since I already had the wheels pointed to the right. It only turned about 3/4 of a rev... Huh, that's odd. So, I hop out to see what's hitting what. Everything looks clear, the wheels are still pointed right. So, I hop back in and try again. Nope, wheel won't turn left, so I turn it right. It spins about 3 1/2 revs.... I hope back out and watch the wheels as I spin the steering wheel. Turn the steering wheel left, the wheels point right. Turn the steering wheel right, the wheels point left. SURPRISE!
Yup, you guessed it. the Miata connects the steering in FRONT of the axle, the Vue connects BEHIND the axle!!!
Damn, it was ALL DONE too....
So, a big reminder if you are looking at a project like this, research EVERYTHING.
The really sad part of this chapter is I think the stock rack would work now. When I "needed" the smaller rack I was trying to get the motor as low as it would go. Once it was in the car I found that I had room to raise the motor (about 1") without contacting the hood. This gave me more ground clearance as well, so I had rebuilt the motor mounts last Fall. With that change I think I could now use the OEM steering rack...
I do still have the mounts that I cut off (yeah, just ask Kerry, I never throw ANYTHING away...). So, if anyone knows of an available manual steering rack from an NB Miata, looks like I'm in the market....