I've got a few broken off exhaust bolts in my aluminum heads.
I remember someone posting a video on here (a long time ago) where the a guy used an accelerated chemical reaction to "rust" the steel away. I think he used a battery charger/electrolysis. I've searched but couldn't find it.
If I recall correctly he used some pretty colorful language.... Can someone point me in the right direction to find it?
Thanks
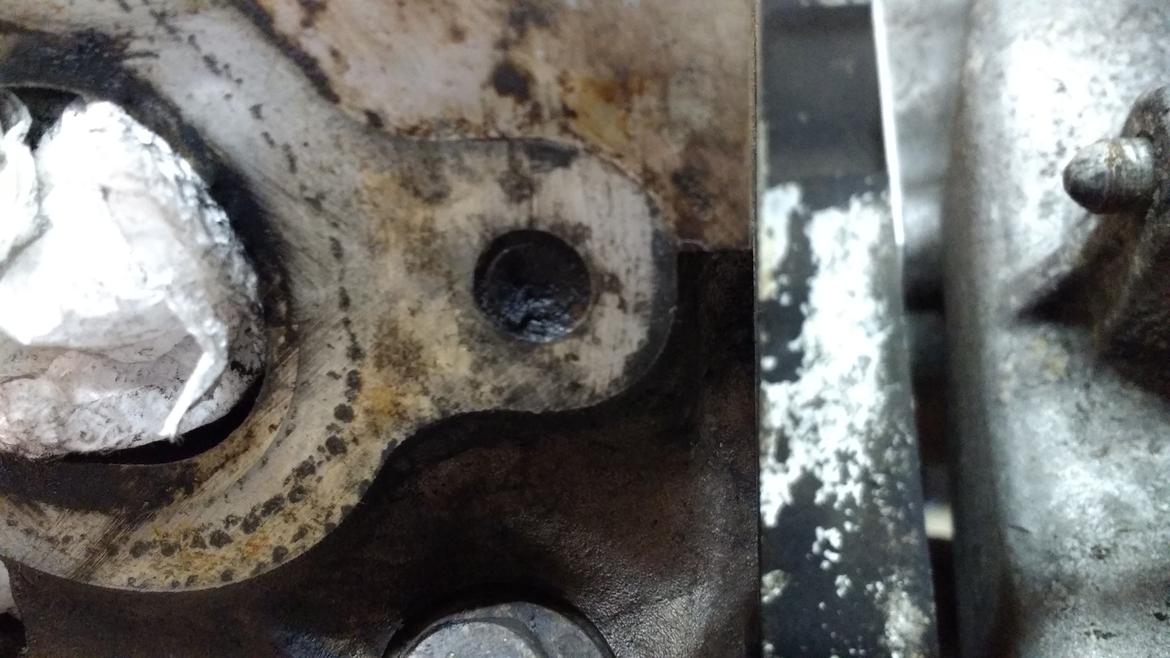
Ug.
Right. Angle. Drill.
And patience. Plenty of patience.
I have this exact problem. I'd be interested in trying this bought I'll probably end up using more traditional methods.
Nugi
Reader
12/10/19 10:29 p.m.
https://hackaday.com/2015/08/03/dissolve-steel-drill-bits-in-alum-from-the-grocery/
Alum
If you have a welder this is what I have done to about 5 different sets of LS heads.
Weld a nut to the cracked stud, quench that weld with a spray of PB Blaster and start to turn it while it's still hot. If the nut keeps shearing off I smack the stud with a center punch and hammer, try and knock that rust loose. Then I build a little weld up until I have something I can grab with vise grips or try to weld another nut to it.
This is not what was asked for, but left handed drill bits are a treat for this kind of E36 M3. Center punch, go slow, ever increasing sizes of drill bits.
Apologies if this is too rudimentary.
Weld a washer to the end of the bolt. Weld a nut to the washer. Turn nut with socket, break weld.
That's okay, you need to do this in order to get the rusty crud off the end of the stud.
Repeat: washer, weld, nut, weld. Stud will come out this time, if not then it will come out the third time.
Have done this many, many times on Chevys and Fords that break exhaust manifold bolts. It takes so little time and effort, you'll never pick up a drill again.
lrrs
HalfDork
12/11/19 5:27 a.m.
It was AVE from youtube. He used alum, previously mentioned.
I tried it on exhaust studs on a subaru, no luck. Might have been to cold, it was winter and I did keep it heated with a light bulb. The engine might have been to much of a heat sync in my 30 degree garage.
wheelsmithy said:
This is not what was asked for, but left handed drill bits are a treat for this kind of E36 M3. Center punch, go slow, ever increasing sizes of drill bits.
Apologies if this is too rudimentary.
This is what I did with my 313k mile engine. Had 6-8 broken studs, was able to get 3-4 with a tool that grabbed the remaining stud. Two we had to drill the whole way through and used an EZ out reverse drill bit. Then retapped the threads to clean it up.
The weld a nut on is a popular solution on the Internet.
Knurled. said:
Weld a washer to the end of the bolt. Weld a nut to the washer. Turn nut with socket, break weld.
That's okay, you need to do this in order to get the rusty crud off the end of the stud.
Repeat: washer, weld, nut, weld. Stud will come out this time, if not then it will come out the third time.
Have done this many, many times on Chevys and Fords that break exhaust manifold bolts. It takes so little time and effort, you'll never pick up a drill again.
This is the correct answer. We do this quite regularly, with the engine still in the vehicle.
You will slip with a drill and screw up threads way more often than you will cause trouble with a welder.
Thanks for all the responses guys. I guess I should try the weld on washer/nut method.
I know for sure the drill/"easy" out method is NEVER easy. And for me at least 90% of the time results in drills off center and cussing followed by ruined heads and holes into water jackets.
The Engineer in me wanted to try the dissolving Metal route, but alas I'll defer to the experts advice.
lrrs said:
It was AVE from youtube. He used alum, previously mentioned.
I tried it on exhaust studs on a subaru, no luck. Might have been to cold, it was winter and I did keep it heated with a light bulb. The engine might have been to much of a heat sync in my 30 degree garage.
I tried his method unsuccessfully, too, on a Ford mod motor. It was summer, so I don't think you had trouble because it was winter. I think the alum they sell in Canuckistan must be stronger or something. Lol
Is spark erosion considered too non GRM? That's what I had done when I had a steel bolt break off under flush on an aluminum intake manifold. It only cost me about $20, but that was 20 years ago.
Another vote for welding a nut to the broken stud. Do it once, and you'll never want to drill out another broken bolt ever again!
Another positive is that it concentrates the heat right into the stud, expanding it instead of the metal around it, causing the bond to be broken.
Mig works great for this, tig would be just as good if not better. With the mig, I get a piece of scrap out and get a pretty hot setting going. Then on the stud I just trigger it, letting it cool till it just stops glowing and rinse repeat, making a little tit by stacking the little weld balls onto each other. Then you have a nice little place to hang a nut on so you don't have to try and hold it in place over the hole.
I'll melt some wax on it while it's still hot, but I wait at least until it stops glowing to put a wrench on it. You might have to work it back and forth a bit, but it will come out.
In reply to TheRyGuy :
That's the joy of welding to a washer, you just build up the weld bead until it gets to the washer and then weld to that.
As Streetwiseguy points out, this is suuuper easy to do when fighting broken off studs in-chassis. I'd tack the edge of the washer to a piece of steel coat hanger so I could position it with one hand and then zap it in with the MIG in the other hand. Then break it off or snip it off with side cutters if for some reason it doesn't want to just snap off.
There's a small risk of boogering the end of the threads in the head... well who cares? It's probably boogered anyway, given the mechanism that causes the bolts to shear in the first place.