67 Lemans. There are tons of options for mix-n-match GM brake, steering, and spindle combos. Only problem is that they have drawbacks galore. The spindles on A-bodies are short enough that it causes a camber-out condition during compression. (short spindle means the upper A-arm is pointing down and swings out as it comes up.)
B-body and some F-body spindles are taller, but with a cast-in steering arm that is in the wrong spot, it makes lots of bump steer. Howe makes tall ball joints for lower and upper which helps alot, but then I'm relying on skinny ball joints to take that load.
Since the spindle is forged steel, what is preventing me from making it 2" taller? I could use a tapered shaft from a ball joint as a starting point, weld that to some 1-1/2" solid bar stock and weld the stock to the spindle... you get the idea.
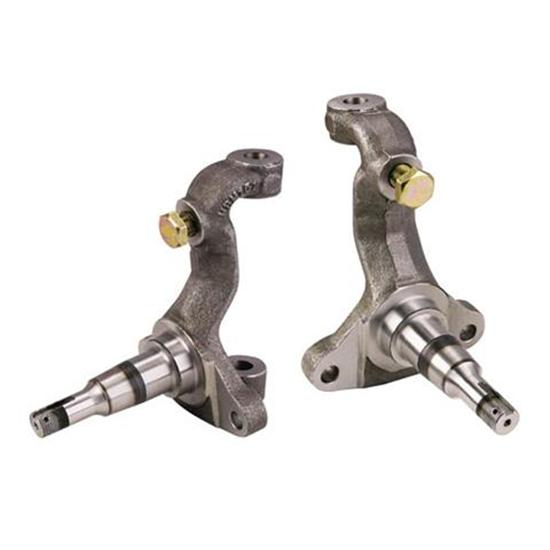
It may be possible to modify the spindle, how it would hold up would be a concern to me. They do make tall versions of the stock spindle: https://www.cachassisworks.com/p-1215-camaro-67-69-chevelle-64-72-nova-68-74-2-drop-tall-upright-spindle.aspx
I ran the Howe ball joints on my 67 El Camino, both street and autox, never had any issue with them.
Yep... $400 for $30 worth of steel. Howe joints aren't much cheaper at $70 each.
I was thinking more like $30 worth of steel and $10 worth of welding. My hope was to avoid the incredibly expensive tall spindles from the aftermarket.
curtis73 wrote:
Yep... $400 for $30 worth of steel. Howe joints aren't much cheaper at $70 each.
I was thinking more like $30 worth of steel and $10 worth of welding. My hope was to avoid the incredibly expensive tall spindles from the aftermarket.
Thats a silly argument - get yourself your own 100 ton forge, some dies, some billet, maybe a mechanical engineering degree or two, and you can probably make yourself a set of spindles too. Until then, $400 is a bargain to make sure you and your hot rod are not seen on the next episode of "Worlds Blankiest Blank"
It is a silly argument, but my point was to say that the only reason they are $400 is because they are specialty items. I'm on the GRM forum. The point is to find out if I can make my own specialty item instead of paying the first-world, rich-guy premium. If I want to know how to throw money at a project, I'll read Car Craft. 
Look at what all the drift kids do. Everyone welds on there spindles. Ive seen some scary stuff work.
http://2.bp.blogspot.com/-6-S2Y0zWotI/UTRLCkXnwbI/AAAAAAAAA4Q/x0aoZNPhGUU/s1600/2013-03-03_20-13-47_944.jpg
Then there is some that think it through a little more.
http://fc3spro.com/TECH/DRIFT/DCOMPARE/ds4.jpg
Here was my thought. Take a tapered shaft from a ball joint, thread the top with a die for 1/2" or 9/16" threads, depending on its OD. Torque it in place just like a ball joint shaft. Take a piece of solid hex bar about 2" long and about 1.5" diameter (drilled and threaded) and torque it down onto the spindle at about 40 lb-ft. Then take a piece of flat 3/4" stock (not shown to scale because I ran out of room) drilled to bolt onto the hex and a tapered hole for an upper ball joint.
Preheat, weld, enjoy.
The upper ball joint sees a tiny fraction of the abuse that the lower does. Most of its loads are lateral instead of vertical. If a 9/16" lower ball joint shaft can suspend the entire weight of the car in extreme situations, then I would expect my 1.5" x 2" long solid steel upper to hold up. Especially because it primarily sees lateral loads.
As always, I am over-thinking, but this is a fun bench-build idea.
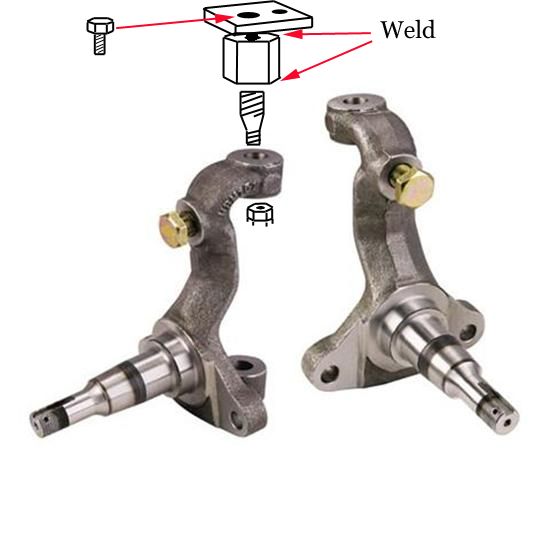
Probably easier to modify the control arm with a ball joint spacer of some sort.
Kenny_McCormic wrote:
Probably easier to modify the control arm with a ball joint spacer of some sort.
Which won't do a darn thing because you aren't moving the pivots.
Actually, it would do something - it would make wheel fitment more difficult.
Would it make more sense to use the later spindles and just bend the steering arms to suit/use a rod-end and bumpsteer spacers instead?
Regarding upper ball joint strength, remember that replacement ball joints are generally held in by four 5/16" bolts, at least one of which has stripped threads because someone tried overtightening it. And the upper control arm is a lightweight, heavily cantilevered piece of 16 gauge steel. Strength should be considered but I think most loads on the upper arm come from resisting braking forces.
Check with local short track/dirt track guys. The spindles I see on NASCAR cup cars have lots of bits welded to them. granted not to extend the upper ball joint position, but the idea is not unheard of. Worst case, get a junkyard piece, weld it up and see how it turns out. Then put it in a press and see what gives...
As a guy that autocross and daily thant gen a body, I can truly say you're over thinking this.
Ive got tube arms, hotchkis coils, bilstein shocks, jgc steering box, and a second generation trans am sway bar on the front of mine. Other than needing a different set of upper control arms due to mammoth wheels, im truly content with it. In my experience, the bump steer and camber gain are not the limiting factor that the internet wants you to believe.
If you are convinced that you need to change that geometry, proforged makes tall upper and lower ball joints for 50 ea. Speedway has the tall spindle for~299.
I truly believe that it's unnecessary.
There used to be / may still be, a tapered adapter to extend the stock ball joint stud it had a fat OD close to the pad on the knuckle size and a tapered stud to fit in the spindle So its was a male and female tapered unit to raise the pivot point. Roundy round car used them in the 80's Hard part was lock the two tapes together you had to heat it and screw it one then drill for a pin. pain in the buttock.
I agree you can get away without doing this, a lot of cars either come with truly atrocious suspension geometry or obtain it with a little lowering, but there are gains to be had with good geometry and if you want them, your idea is solid.
You might also want to consider designing and CNC'ing custom spindles, if you can do your own CAD you should be able to get it done for about half the cost of the commercial drop spindles.
There was a guy selling suspension parts at the last track event and I remember there ws a fabricated spindle there that was pretty delicate looking. Not cast, not forged, just fabricated plate and tube stock with some gussets. I asked the guy what it was made for thinking he was going to say thunder roadster or something butt it wasn't. It was for a 944 I think. Oh parts are generally overbuilt to handle the kinds of ridiculous mistakes people make with curbs, speed humps, and other hoo ing events. I think you can make the extensions work in all but the most extreme looses. But you will just need to be ready for repairs when your oops crosses that line.
tuna55
UltimaDork
2/6/15 7:31 a.m.
There is no fundamental reason that it won't work. I don't expect the spindle is heat treated. If it's steel, the only drawback is that it's really big.
Personally, I would be happier borrowing a mill and pin/bolt a spacer to the top/bottom pads and then whittle away the same thickness from the inside. Get yourself a reamer and you're set.
I am using tall lower balljoints on the truck, and I suspect they work but they have zero miles. You could also space the balljoint away from the control arm pretty easily which will also help somewhat.
It's steel, and you can weld and operate a mill. I am pretty sure that this isn't impossible.
I watched a guy cut a used NASCAR spindle and reweld it together with dozens of passes with a mig welder to change the kingpin angle. It took most of a day to do the pair but they worked fine. What about doing that to make them taller? You may use enough wire to make them as expensive as ready made ones though.
$5 in wire, $50 in electricity, $500 in time... 
I've made things like that before. The accursed Audi 016 Shift Ball in one of my cars is 90% weld. But it is definitely not for the faint of skills because it's easy to make a lattice of weld instead of a solid part.
If we must modify a spindle, I'd feel better modifying the steering arm of the B/F spindle (or some other part in the system) to correct bump steer than the main body of the stock spindle, which probably has some degree bump steer problems to begin with.
Knurled wrote:
Kenny_McCormic wrote:
Probably easier to modify the control arm with a ball joint spacer of some sort.
Which won't do a darn thing because you aren't moving the pivots.
Wouldn't it make the effective arm length shorter? Also bring the arm up farther in its travel giving more gain on bump, hopefully to a point of getting the arm level at ride height.
A ball joint spacer would effectively lengthen the arm, I would think. Regarding yoru second point, nothing changes if you aren't changing the actual pivot points. When people talk about the angle of the control arm, they mean the angle of the inner pivot - ball joint pivot axis. The fact that the control arm is shaped like a squashed out horseshoe means nothing.
Shortening the arm, in a lowered car, would give one major benefit of a practical nature: You won't need a huge stack of shims to align the car. There's also only so much negative camber you can get because of the way camber is adjusted, and the more negative camber you try to get with the shim adjustment, the less clearance you have to the header on the passenger side. This can be a non trivial problem with certain engine/header combos!
Knurled wrote:
Kenny_McCormic wrote:
Probably easier to modify the control arm with a ball joint spacer of some sort.
Would it make more sense to use the later spindles and just bend the steering arms to suit/use a rod-end and bumpsteer spacers instead?
Later spindles are cast iron. Not nice for modifying.
Dusterbd13 wrote:
As a guy that autocross and daily thant gen a body, I can truly say you're over thinking this.
Ive got tube arms, hotchkis coils, bilstein shocks, jgc steering box, and a second generation trans am sway bar on the front of mine. Other than needing a different set of upper control arms due to mammoth wheels, im truly content with it. In my experience, the bump steer and camber gain are not the limiting factor that the internet wants you to believe.
If you are convinced that you need to change that geometry, proforged makes tall upper and lower ball joints for 50 ea. Speedway has the tall spindle for~299.
I truly believe that it's unnecessary.
good to know. I have a feeling that the spring rates and sway bars I'll be using won't allow enough body roll to really make compression camber much of an issue, but I'm tending toward being perfectionist with this build. It is my dream car after all.
There is also the fact that I will be lowering it a tad which will slightly counteract that camber issue
it's been a while since i've seen anything good on making those cars handle, but i'm remembering that lowering the A body a couple of inches puts the steering arm in a better place for bumpsteer and what not as well as putting the upper arm in a better spot for camber and caster magic to happen... putting in a tall lower balljoint makes it even moar better.. aftermarket upper arms are generally made with more caster and camber dialed in so you don't need a 2" thick stack of shims to make it all work.
ask these questions on the forum at www.chevelles.com and you will get steered in the right direction once you wade thru all the "just buy the low end $1500 package from so-and-so" posts and find the actual useful DIY gems..
I'm also kind of a master of wading through hundreds of pages of Moog parts catalogs. I recall doing that a lot with the Bonneville when I put 3/4 ton truck spindles on it. I matched up specs for ball joints - bolt patterns, tapers, etc, and was able to put together a mix n match assembly with only minor adaptation. I remember using shocks from a Dakota, springs from my Impala SS, upper ball joints from the truck, and then I forget exactly what I did for the lowers. I was able to fully adapt the truck spindles and brakes with minimal headache.
Only problem is... parts stores rarely have physical catalogs anymore and the manufacturers' websites often just list application. Plus the nice thing about being at a parts store catalog was I could go pull the parts off the shelf and visually compare things.
Maybe a NAPA or something would still have paper catalogs I could use.
FWIW, I've seen some of the knuckles modified for drifting take a shocking amount of abuse without blinking.
Like, 'slide sideways into a curb hard enough to shatter the wheel' type damage.
Obviously YMMV depending on the skill level of the welder and how much you're modifying things, but yeah.
curtis73 wrote:
I'm also kind of a master of wading through hundreds of pages of Moog parts catalogs. I recall doing that a lot with the Bonneville when I put 3/4 ton truck spindles on it.
Details please! That is very... intriguing.