Every clutch job I've done has been with the help of my dad. When we're putting the trans back in, he always insists on getting the bellhousing completely flush against the engine before tightening any bolts. Using the bolts to draw the trans to the engine, he's always told me, could damage the pilot bearing.
Which makes for a very tricky portion of the job. Lining up the input shaft on a 100-lb. object with a pilot bearing with very tight tolerances usually requires many, many attempts. That's the hardest, most frustrating part of the job for me.
Is he right? Will I bunge up the pilot bearing if I just start tightening those bolts to pull the transmission into its final position, or have I been doing it the hard way for naught all these years?
The cars I have specific experience on: CVH and Zetec Escorts, Mazda Miata.
oldtin
SuperDork
7/26/12 10:22 a.m.
Less concern for the pilot bearing than stress on the input shaft/bearing. I try not to have full weight on the transmission, but for a one-man job, I don't mind using the bolts to snug things up.
Entirely possible. BUT. Your biggest issue normally is getting the input shaft engaged and through the clutch disc splines then the pilot.
I get the trans as close to the motor as possible and at least engaged partially in the disc. I then install a few bolts snug to the current position, as you are normally tired at this point. I make sure to have the clutch cable or hydraulics hooked up and push the damn clutch in. From there the trans slides right in. The clutch disc is what holds getting the trans back in, no matter how well the disc was aligned.
You want to keep it as straight as possible, but I would have no qualms about hanging it with a couple upper bolts, getting a jack under the tail and then leveling it with the jack and drawing it in with the bolts. Like oldtin said, the input bearing it taking most of the stress here,the clutch disc being locked in and lined up takes stress off the pilot bearing.
Is it really a problem that there are transmission input shaft/engine pilot bushing clearences that are so tight that it takes force to put them together?
That's a serious question- I don't know that.
Opinion wise, IIRC, for movement that is supposed to be allowed for in the design, that tight of a fit doesn't seem to be right. but it's been a good 20 years since I've done anything with part tolerances.
I side with pops on this one.
I always clean the input shaft with a little emory and test fit the pilot on it before installing it in the block. Then I clean the teeth really well and lightly grease them. You should not need much effort to put them together - so I would generally worry that if you need to torque it in you are forcing a thing that should not require it.
I have friends who have damaged clutch fingers during an install and can only imagine they had it misaligned and drove it home anyway or got tired and let the weight hang before it was all the way in.
Just did one in the '01 Miata last week. Splines dropped through easily but It didn't want to snug up after 15 minutes of wrestling. Got it close (~1/4" gap) before threading the top bellhousing bolts in by hand. A little jiggling on the tail and the gap closed up tight all around.
Not sure if that exactly answers your question, but that's the 2nd Miata I've done that way and the 1st (turbo - 3 track seasons + 20K street) is still going strong.
I'd also be concerned about the possibility of cracking one of the mounting ears off the transmission. It should go all the way into place without having to force it, you may have to spend some time jiggling things to get the shaft and its splines to line up.
Dashpot wrote:
Just did one in the '01 Miata last week. Splines dropped through easily but It didn't want to snug up after 15 minutes of wrestling. Got it close (~1/4" gap) before threading the top bellhousing bolts in by hand. A little jiggling on the tail and the gap closed up tight all around.
That's exactly what I'm talking about, but that "little bit of jiggling" sometimes is a lot more than just a little jiggling. I'm not concerned about using force to slip them together, the pilot bearing has always fit fine on the input shaft.
But once you're pulling the transmission toward the engine and don't have the input shaft seated inside the pilot bearing—that last 1/4" when the input shaft is lined up with the disc splines but not inside the pilot bearing—is it possible that I could pop the inside race out of the pilot bearing, or push the bearing cockeyed, or crunch it up.
I've found the key is getting the splines on the disc, and the bearing to resemble a target. PERFECTLY set clutch disc requires very little effort to re-attach the transmission
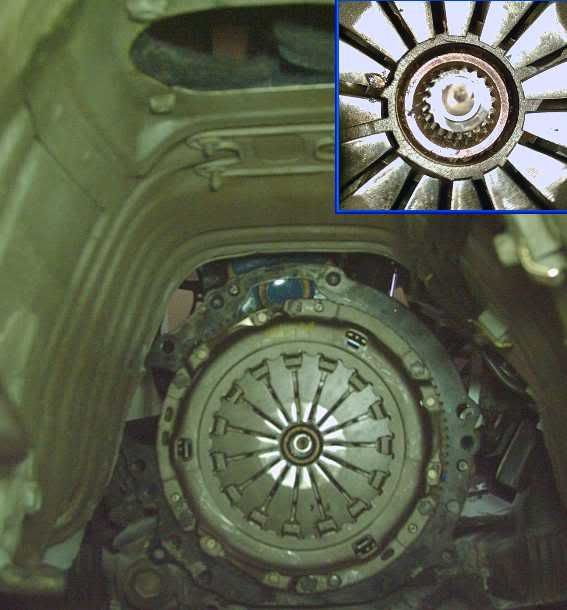
First, you gotta get the splines in the disc. Then you gotta get the pilot into the bushing. Then you gotta get the dowel pins into the bellhousing. Mess up any of these steps, and you mess up the job.
I remember talking to a sales rep from a clutch manufacturer a few years ago- he said that their clutch warranty claims dropped by 90% or so as soon as they started shipping the little plastic clutch alignment tool in their kits. He said that almost all of their warranty returns had a bent disc, usually from the mechanics getting worn out trying to jam it in, so they would let the trans hang from the splines for a while as they caught their breath.
Pops is right. Spend the time to clean everything up, align it properly, have enough strength and help or tools that you can easily lift the thing in place and have it slide into the holes easily.
A tip for using the clutch alignment tool - make sure you can slide it in and out easily. That'll show the difference between "close but not quite" and "perfect".
I've seen a busted block from a mechanic trying to force what he thought was a tight fit on the bearing. The trans was moving in as he tightened the bolts, but then one of the ears busted off the block. Why? Because the pilot bearing was designed for a different trans and was a different thickness, and the input shaft was bottomed out. Sometimes, you need to find out why it's so hard to get that thing on...
I side with pops on this one too. A few things I have learned over the years:
Those plastic cheapo tools are teh suck. They are usually a much sloppier fit than the input shaft so the pilot/disc can be as much as .040 out, Since most bronze bushings have ~.003 or so clearance and the disc splines even less that's enough to make it hard to install the trans. This means you have to get a bit creative; I have stuck a piece of thin cardboard over the tip of the tool to make it a tight fit in the pilot bearing, then 'eyeballed' the splines to make sure the disc is centered. Sometimes you can use safety wire or paper clips to make the tool a tight fit in the disc which also helps with the centering. Just be sure you can get the wire etc back out!
See if there is a hole in the bellhousing which will allow you to tighten the PP bolts after the trans is in place (MGB's are good for this). Install the disc and PP with the cheapie tool, then tighten the PP bolts so that it holds the disc in place but you can still slide it with some effort. Now install the transmission, it makes the wiggling etc much easier. Then tighten the PP bolts through the aforementioned hole.
Most input shafts have a chamfer on the tip to make inserting it in the pilot bushing/bearing easier but some do not (MGB's again). It helps a lot to file a small chamfer on the end of the shaft.
If you just can't get that last 1/4", try this: start the bolts and run them up to the bellhousing but do not tighten them. Now use a pry bar to work the release lever to disengage the clutch and allow the disc to move, I have had that 'finish' the alignment for me. If it's a cable clutch, the cable can be connected and accomplish the same thing but you really need two people: one to push the clutch pedal in, the other to be ready to push the transmission the rest of the way when you let off the pedal.
I usually use a piece of threaded rod, or bolt with the head cut off in 2-4 of the bolt holes, and the trans almost always just slides right in.
I usually get them close, say 1/4" to 1/2", and hang the transmission with a couple of bolts. Then I kick the crap out of it. If that won't snug it up, I start looking for why.
With most pressure plates, the alignment tool is nice, but not critical. I have centered discs by feeling the edge of it in relation to the pressure plate, with the bolts snugged enough the disc can be moved, but will stay in place when it is left alone. feel the same amount of plate in three spots around the disc, you are good.
Zomby Woof wrote:
I usually use a piece of threaded rod, or bolt with the head cut off in 2-4 of the bolt holes, and the trans almost always just slides right in.
I was going to say that.
A couple head less bolts help a lot. they were a standard in my tool box.
Once everything is lined up it should slide together with no force.
Zomby Woof wrote:
I usually use a piece of threaded rod, or bolt with the head cut off in 2-4 of the bolt holes, and the trans almost always just slides right in.
Used to do that for heads sometimes too, as long as there is room to slide the head straight down. B20 Volvos didn't have any dowels, IIRC.