Have to move a seat track on the new seats for the duster. Have to move the rail to clear the floor, and narrow the space between the tracs by about 4 inches.
The rail im moving is the outboard side, with the recline mechanism mounted to it. The bracket on top of the rail has to remain where it was from the factory to hold the back of the seat and recline mechanism in place.
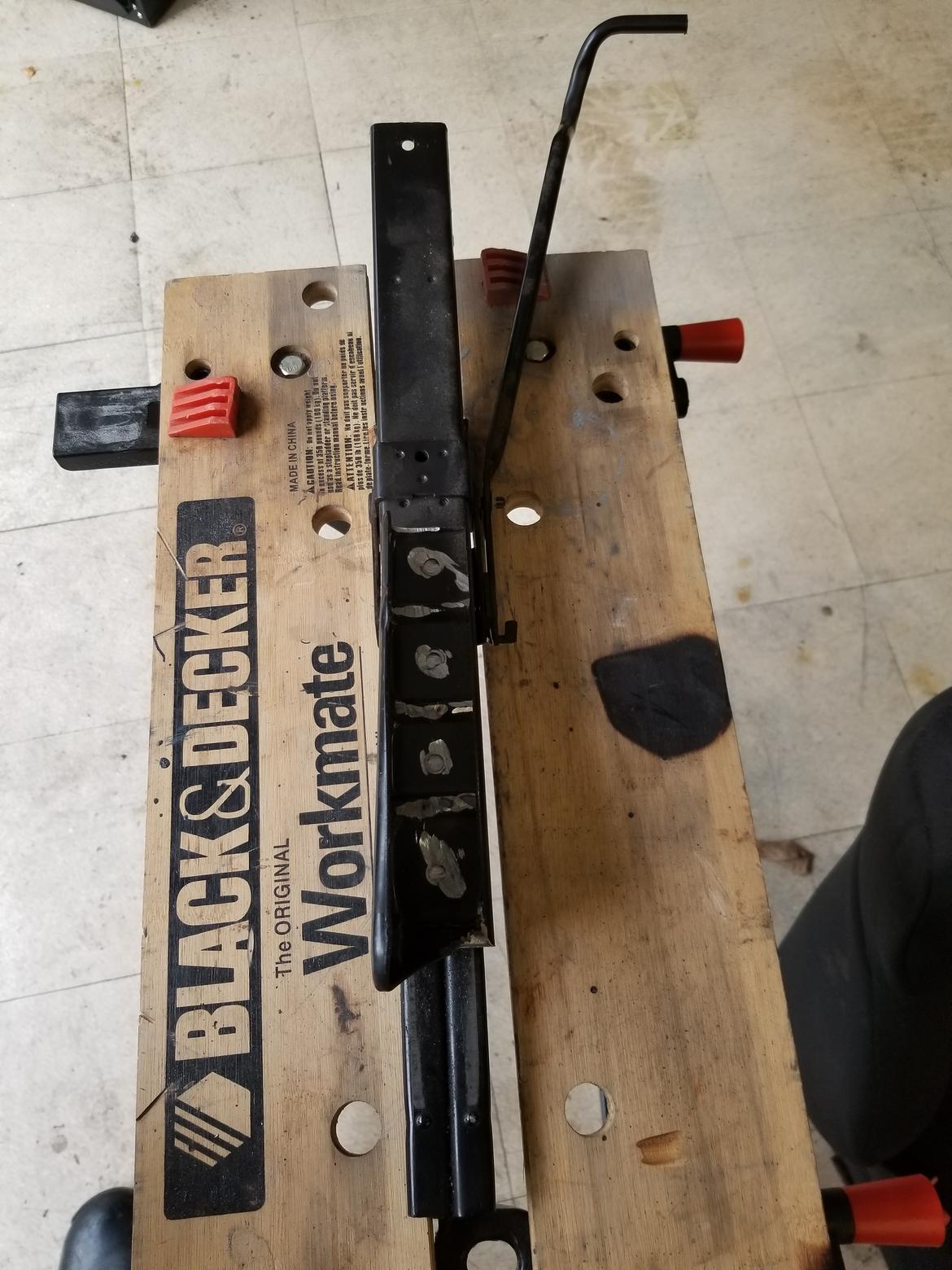
Needs to move around to about here (not to scale, etc)
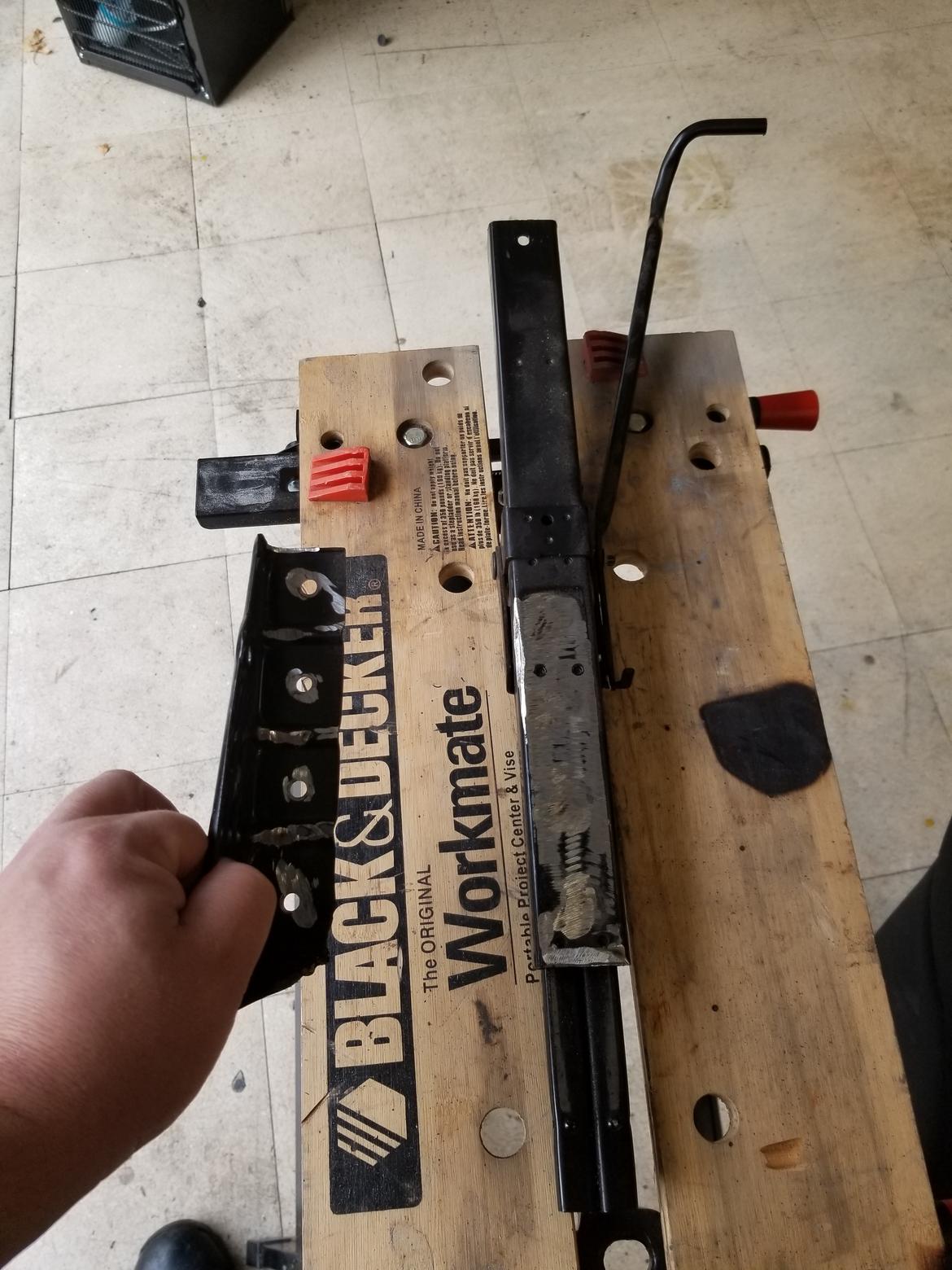
What should I use to bridge the gap? Im thinking 1/8 plate welded to both halves. But....
The front of the rail will have a new hole drilled in the seat frame, or a piece of steel welded in and drilled for it.
What say the hive and more experienced people? I would be
Here's an in place picture of what we need to do mocked up on the seat base itself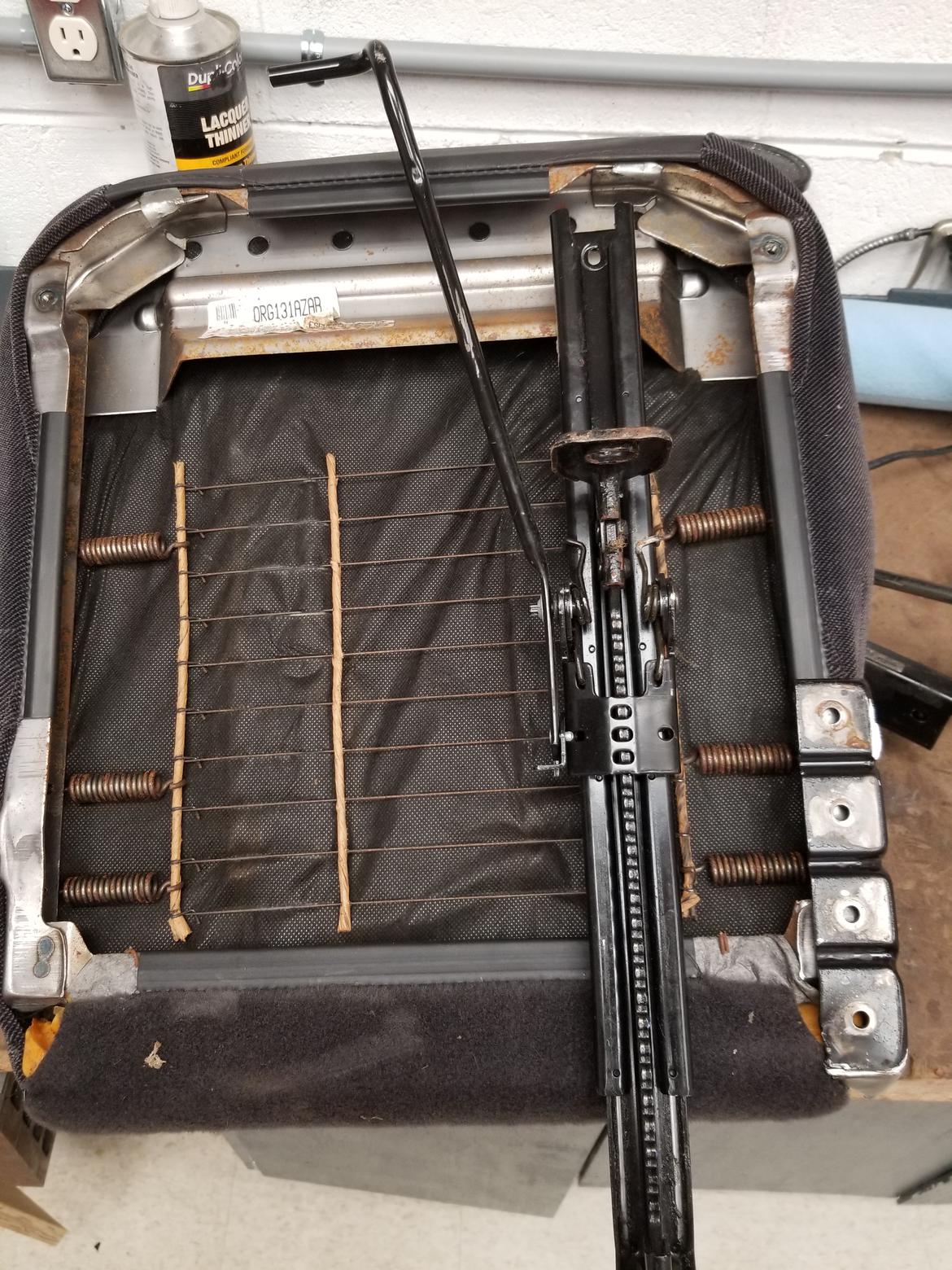
Can you bridge the entire seat (both rails) with angle iron? That will keep it from just trying to twist the one adjuster rail.
In reply to ¯\_(ツ)_/¯ :
Yes i could, weld angle to inside edge of c channel shaped top track to same spot on the other side.
Or are you thinking something different?
¯\_(ツ)_/¯ said:
Can you bridge the entire seat (both rails) with angle iron? That will keep it from just trying to twist the one adjuster rail.
That's what I did for the stock slider rails on my racecar to fit raceseat brackets. Held up in an accident with a concrete wall at 100+ mph at Charlotte.
Just make sure you aren't butt welding it. It must overlap and preferable hit more than 1 plane if possible.
After looking at your pic, just weld some steel across from 1 side of the seat to the other and drill some new holes. Weld some nuts to the top side of the new welded in steel for fastening hardware.
In reply to Dusterbd13-michael :
I think we're talking about the same thing. I'd do that, if it needs to be low notch the channel/angle where it crosses the sliders. 1/8" should be plenty.
In reply to wvumtnbkr :
Answered what i was trying to ask above.
Does in need to be anywhere specific along the length of track, or just as far fore/aft as possible?
Dusterbd13-michael said:
In reply to wvumtnbkr :
Answered what i was trying to ask above.
Does in need to be anywhere specific along the length of track, or just as far fore/aft as possible?
Not sure if this answers your question, but I would layer it up right where the existing mount holes are.
To say it another way, modify the seat by adding some steel to it so the sliders bolt on like they don't know the difference... definetly bridge the gap from one side (where the seat normally mounts) to the other side (where the seat normally mounts.
Drill your holes where you need them for the sliders. Weld some nuts to the seat side of the reinforcement so you don't need 2 wrenches to install.
Make sure the welded in nuts are on the top side so that the clamping force of the fastener is what holds this together. Don't rely on the small bit of weld of the nut to the reinforcing metal to hold it together. Welding the nuts is just for convenience. Not for structure.
I've done this a few times. You have my number if you want specifics.
Ok. I THINK i get what youre saying. Easy to see on the front part.
The rear, where the seat tracks originally bolted on perpendicular to the front (up on the side of the triangle) i cant picture how to do other than flat plate from horizontal of triangle to horizontal of bracket. Maybe able to do a SMALL gusset (1/4-1/2 tall) to make the plate 3d, then go to angle between the seats.
Any flat material is going to deflect, unless you make it really thick, and then the seat base or the rail will deflect. Some sort of square tube, running across the seat, trimmed to fit up into the pocket formed below the seat springs and welded to the frame on both sides gives you structure. Then you weld tabs to that to attach to the slide. Does the other slide have to sit outboard of the seat the same distance this one is inboard?
No air. Trans tunnel side remains unmolested.
Will solid round stock welded to flat stock serve to eliminate deflection? Like 1/2 inch solid round?
Mr_Asa
New Reader
1/15/20 5:31 p.m.
In reply to Dusterbd13-michael :
I've been wondering this for a project of mine, I'll be following along to this and may hijack it once you get your answer
In reply to Mr_Asa :
Dude, hijack! We all learn from the hijacking around here
Mr_Asa
New Reader
1/15/20 6:14 p.m.
In reply to Dusterbd13-michael :
I think the responses you've gotten have answered a lot of it. I need to get out to the car again and take a look and see what might be in the cards.
Weekends are for wrenching for me.
If you look at the beam equations in the engineering texts, you'll see that angle has many times the bending stiffness of plate and square tubing has many times the stiffness of angle. Last time I made a seat bracket for my track car I tried to use all the square tubing I could.
Michael, how much gap is there between the top side of the track and that wire suspension harp? Any chance your tiny little butt will sink in far enough to contact the track?
Also, if you cantilever the recline out 4 inches you'll be significantly changing the load path in a rear collision situation. It needs to be strong, not just some flat stock. It WILL twist in a collision.
In reply to DeadSkunk (Warren) :
Thats why i was asking about round stock for stiffening instead of angle. Its going to be close, and will probably make contact over large bumps that cause tire scrub and bottoming
Mr_Asa
Reader
1/16/20 8:30 a.m.
In reply to Dusterbd13-michael :
Two layers of steel plate with basically an I-beam construction in between? Be a serious PITA to get it all welded without some trickery, and would raise the seat an inch or so, but you'd get that strength you need and you'd have the clearance between the seat bottom and the plate
You can weld some steel in the "y" plane to increase stiffness.
I would probably do an x or similar shape to support torsion, bending, etc forces.
I have a seat and some sliders I need to weld up in my garage. I can send you some pictures.
You definitely need support in 3 dimensions. That can be as easy as using angle iron, creating angle iron by welding a strip of steel, or incorporating some other geometry.
A solid round bar could work, but it's probably going to act like angle iron once solidly welded in place and will be WAY heavier.
A couple of 1/2 inch ribs welded on perpendicular to the seat mounts would most likely provide all the strength you need. Strategic placement will make that quite strong.