pheller
UltimaDork
5/19/21 4:35 p.m.
I know many of you work in construction industries and/or are very knowledgeable when it comes to market mechanisms.
What the heck is going to end this deal with lumber prices being through the roof? Do we need more production? More trees?
What indicators might the public be able to use to say "ah, yes, several wood mills are coming online in my area, that means prices might soon be normal?"
I've got a 11x20 deck I want to build but the materials will actually cost more than the labor. My wife wanted the deck built yesterday, but $20k for a simple deck seems pretty outrageous.
When supply and demand get balanced out again. The past year has been a great illustration of how production is balanced against demand and the length of the supply chain both in distance and time. We're still dealing with perturbations from last summer.
As for trees, a lot of US lumber comes from Canada. And Canada has been (and remains) more restricted in production than the US for a bunch of reasons. On top of that, crossing the border has been a problem for the past year. So there's your supply. I'd keep an eye on the status of things in Canada, then add a few months for supplies to fill up again.
As for the demand, don't ask me why the construction industry suddenly went berserk :)
My deck cost more in materials than labor when I built it last year, but that's because I don't get paid to swing a hammer!
I may be either misquoting or misunderstanding the gist of what my friend and architect of my new shop told me, but to some extent he expected that we're never going back to the sort of depressed prices we had right beforehand.
The part I'm really probably garbling is that prior to the 2007ish downturn, with all the construction going gangbusters, the lumber folks got super-ramped up. Then the bottom fell out, and everyone had too much inventory, too much storage, too many resources they were paying for and no longer had the business to meet. The upshot being that they're probably not going to bet on ramping up to that scale again.
I don't think this entirely explains why building supplies were nominally undervalued that whole run, as I'm sure everybody who stayed around scaled their businesses to meet the post-2009ish reality over the ensuing decade. But it does explain that when current supply chains had Covid-related issues AND everybody decided to remodel the family room at once, we had a radical supply/demand issue and pursuant price mayhem, and it also explains why nobody's going to scale up a ton to meet this demand: By the time they did, it'd be over. So prices will probably come down some when the current spike dies down, but per my friend's guess, they'll probably never get back to 2019 prices.
Anyhow, that's my flawed understanding, explained badly.
I'm just trying to be philosophical about it while I start construction on the new shop... I spent $25 on an 8' 2x12 to use as a wheelbarrow ramp.
A great deal of Canadian lumber comes from British Columbia, and they have locked down really hard through Covid. Lotsa stuff shut down out there.
The cross border thought might contribute a bit, but lumber is horribly pricey up here too.
In reply to rustybugkiller :
Hey, whatever floats your deck.
I'm currently replacing all of the soffits, siding, and trim in prep for a new roof. Really, really bad previous structural repairs and poor roofing install resulted in subsequent water damage and termite damage, so I also have to replace a lot of the framework. The prices are killing me and I have no option to wait because hurricane season is approaching and there's already sections of roof missing.
[URL=https://app.photobucket.com/u/NOTATA/a/83944394-df08-49c6-b28a-2b3db87696e7/p/baa6ba62-2fcf-4505-ae8d-4f9f89c54e3b]
[/URL]
[URL=https://app.photobucket.com/u/NOTATA/a/83944394-df08-49c6-b28a-2b3db87696e7/p/160c675d-fd9d-43ce-b2d7-9ea53c9bbd6b]
[/URL]
I WISH lumber was our only problem... steel, concrete, glass, copper, PVC, fixtures... ALL building materials prices have skyrocketed.
We have vendors who priced jobs when 3/4 ply was $32 per sheet, and now it's $58 (on a good day). That hurts a lot when you've got 1000 sheets in a job.
Our vendors won't hold prices at all. Hard to bid jobs when vendors won't lock in prices.
Duke
MegaDork
5/19/21 9:01 p.m.
The government dumped several metric buttloads of printed money into capital improvement projects for every agency that ever had a budget. This isn't going away until most of that money is spent.
In reply to SVreX (Forum Supporter) :
Crappy 1/2" plywood (well 15/32 now) was $67.00 a sheet at HD here this week, up $5.00 from last week. I bought 3 sheets (200.00!) yesterday and will probably need at least 15 more. Hopefully the price doesn't continue to go up.
For an example, that's more expensive than concrete by the sqft just for materials.
As for the OP, do a concrete pad. It'll be cheaper and better in every way
Duke said:
The government dumped several metric buttloads of printed money into capital investment projects for every agency that ever had a budget. This isn't going away until most of that money is spent.
Say it with me, in-fla-tion.
If it makes you feel better, aggregate prices are staying steady.
In reply to Keith Tanner :
However the price of aggregate is often way lower than the delivery charge. concerning lumber there's been pine beetle kill, wild fires, and other external factors that have reduced the fibre supply so there has been mill closures even in the last few monthes.
There is also a national pallet shortage going on at the same time. Pine wood is hard to come by, the workforce that makes the pallets have dropped almost 50 percent and they can't even get the nails to build them if they could.
In reply to Placemotorsports :
Are those two things connected? Pallets are almost universally made out of oak, not pine.
STM317
UberDork
5/20/21 6:47 a.m.
There are plenty of trees, and they're cheap to buy. There isn't enough capacity at the saw mills (in the US) to meet current demand. Border closures, tariffs, and COVID shutdowns in Canada have made importing more difficult. That means huge profits for the saw mills right now. They're expecting more domestic milling capacity to come online in the next year or two, COVID related shutdowns and border closures won't last forever. When those two things happen, the supply should increase to more sane levels. I've read some people that plan for construction businesses guesstimate that we're looking at elevated prices for at least another 18 months.
https://www.bloomberg.com/news/articles/2021-04-20/lumber-s-version-of-a-crack-spread-is-exploding-from-cheap-trees
But, lumber futures have actually dropped more than 25% in the last few days too, so perhaps there's hope on the horizon
I started learning what an interest rate was when they were above 10%. And I thought I understood inflation in relation to that cycle as I grew older. But now I'm not sure I did. I do understand supply and demand but I'm not sure I get how that relates to long term inflation.
From a few weeks back.
3/4” Plywood Standard:
March 2020 - $37.98 /sheet
February 2021 - $72.49 /sheet
March 2021 - $83.49 /sheet
April 2021 - $95.98 /sheet
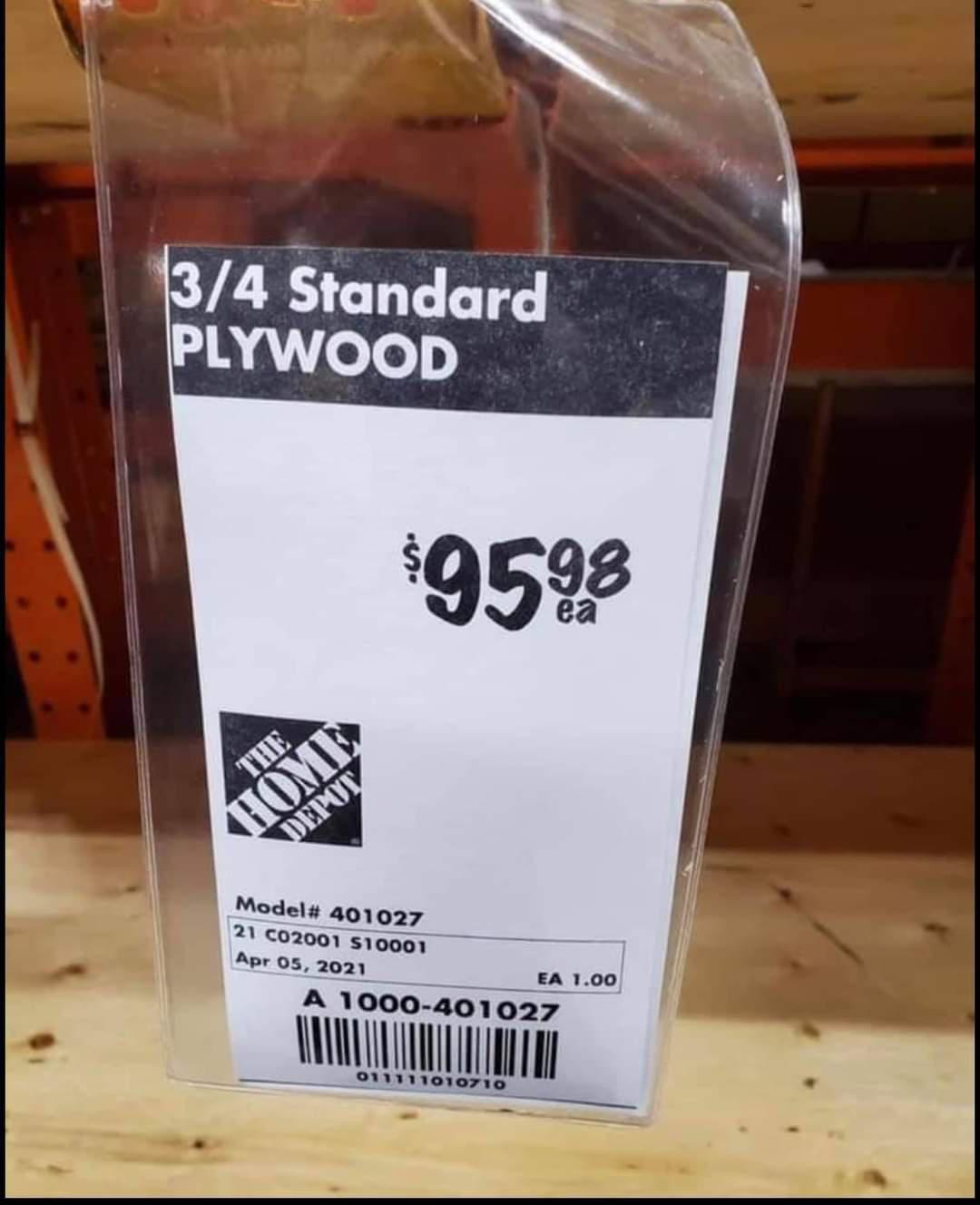
Is building demand that inelastic that materials prices don't matter to builders? I think that's what's most confusing to me.
In reply to lotusseven7 (Forum Supporter) :
I had a friend cleaning out his garage. He had 50 sheets of 3/4" plywood.
I asked him how much he wanted. He said I could have the whole pile for $350. I handed him the money.
SVreX (Forum Supporter) said:
In reply to lotusseven7 (Forum Supporter) :
I had a friend cleaning out his garage. He had 50 sheets of 3/4" plywood.
I asked him how much he wanted. He said I could have the whole pile for $350. I handed him the money.
Holy cats! $7/sheet would have been a screaming deal 30 years ago, let alone today.
mazdeuce - Seth said:
Is building demand that inelastic that materials prices don't matter to builders? I think that's what's most confusing to me.
I don't think I understand inflation either. As a builder, I don't think we control the market at this time.
Our problem is that we bid jobs based on certain prices, and there is a time lag. The lag between contracting a price with a customer, and actually buying the material is significant. In residential, it's 2-3 months. In commercial, it can be over a year. We are locked into our selling price LONG before we buy the product.
I would think that would control inflation to some extent. It doesn't, so I would say that means builders have very little influence on inflation and pricing.
Right now, lumber and residential building products prices are being driven by consumers- buying at a rate they never have, with no knowledge of historical pricing whatsoever. They are walking into places like Home Depot and buying 1/2" OSB for $50 a sheet and saying "Gee... construction really is expensive". They have no idea that the right price should be $7-10.
Builders don't get hurt here. Residential builders typically have really weak contracts. They go to their customers and say, "We didn't figure prices would be this high. We need to charge you more", and their customers bend over and write the check. Commercial builders typically have extremely strong contracts, and hold their subcontractors to the letter of their contract and make them perform at the price they agreed to months earlier. Subs are swallowing the costs because they want to be in business next year, and retain their relationship with their general contractor customers.
I'm not sure how this effects inflation, but I know it's a false economy. There is money in circulation that shouldn't be, and consumers are driving a false inflationary spiral that is not sustainable. But some companies will not survive.
In reply to stuart in mn :
Yep.
I don't even need the darned stuff, but I bought it anyway!