Looking to beef up my resume and add some skills/certifications to make my existing skill set more marketable. Looking at other production management type positions, lots of places looking for Six Sigma certification, or experience with Lean or other TLA manufacturing metrics.
What are people's experience getting said certification?
Most valuable certifications?
How much time and money?
Any recommendations on places/programs to go through for getting certified?
Thanks in advance.
My impression of most of these systems that I look up like Lean or Kanban is that they're really just codified common sense, and I could easily learn on the job whichever one a company wants to work with. If they were complicated, they wouldn't be useful. But the people I need to get past are corporate HR or business-degree people who have never actually worked production, and this is the kind of thing they think is special, so I need the paper to impress them.
Hi Beer Baron,
I received my Lean / Six Sigma Master Black Belt certification about 12 years ago.
I'm headed off to interview somebody right now but please feel free to PM me or I'll respond to your post later today.
Brett
I received my black belt in 2019 through the Air Force, cant say I enjoyed the process which was AF specific. Also a certified scrum master.
If I recall correctly, you are in the brewing industry right? I would look at project management , marketing , and quality management certifications.
I frequent Udemy and LinkedIn Learning but that's because the Air Force has teamed with those organizations to provide free training etc. Could you ask your employer if they have similar situations.
In reply to yupididit :
In the brewing industry now. Strongly considering shifting into other industries that provide more pay and benefits. Figuring out how best to market my transferrable skills. I figured "Production Management" was the most logical shift. Could probably get certifications in specific food health and safety standards if I want to stay in wider food and beverage.
"Project management"... sounds really broad. What would that be? What certifications would help? How would I market my skills? I mean... I regularly develop and produce new beers in collaboration with other groups (like sports team supporters groups). I suppose I usually manage those projects. Someone in sales or marketing learns a group wants a special beer release. They put them in contact with me. I set up the meetings to figure out the specs on the beer, creative direction, timeline, and get a sense of how we're going to brand it. I take care of the actual production and packaging, and someone else handles label design.
What certifications do I get to show that I can handle those jobs?
My sort of issue I'm running into is that I wear a TON of hats being the most central person leading operations at a small company, but I'm not specialized in anything except brewing. Figuring out how to market my skills as a generalist with broad skills at understanding and getting things done.
Current employer doesn't have anything set up for me to get any skills or training. I would just be taking advantage of having free time.
Driven5
UberDork
10/24/22 3:10 p.m.
Beer Baron said:
My impression of most of these systems that I look up like Lean or Kanban is that they're really just codified common sense, and I could easily learn on the job whichever one a company wants to work with. If they were complicated, they wouldn't be useful. But the people I need to get past are corporate HR or business-degree people who have never actually worked production, and this is the kind of thing they think is special, so I need the paper to impress them.
Yep.
These companies all fall somewhere along a spectrum. On one end is the company that has not embraced it at all culturally yet, and thus wouldn't be able to effectively train you on it. The other is that they have embraced it culturally, and while they could train you on it, would prefer to know you're already drinking the kool-aid. The interview process can help indicated where on this spectrum the company in question lies.
Either way, an ASQ Lean Six Sigma Green Belt certification is just another way of baselining that you at least possess the capacity to fundamentally understand how to do things intelligently, regardless of whether or not you actually do so in practice. Unlike a Black Belt, the Green Belt never expires nor requires any certification maintenance. It sounds to me like this is probably the droid you're looking for on the production management side. If you don't have a current employer funding it, look to see if any community/technical colleges near you offer this certification. I know of at least one near me that does.
In reply to Driven5 :
Yep, yep,
I just PM'd the Baron also recommending ASQ and I offered to sponsor his project assuming they'll let me which I'm pretty sure they would since I hold a current CQE with them.
Okay. Just looked up ASQ and submitted a query about Green Belt certification. I think that's the animal I'm looking for.
I don't know about what's involved in funding or what a required project would look like.
Regarding employer funding... the owner would probably be supportive of me getting additional training and certification, even if the goal is to leave for a better job. (He is a supportive friend.) But I would expect him to whine about how the company doesn't have enough money to pay for any kind of training.
In reply to Beer Baron :
BoK (Body of Knowledge)...
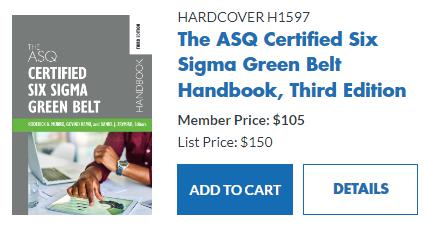
+ $438 for the exam.
You can also get a free one-month trial for MiniTab statistical software.
Required Project = Apply the five step DMAIC process and use the applicable tools to improve a process at your work.
Benefit can be measured in absolute terms (50K annual hard savings) or relative terms (25% reduction in time to markek) or both....spoiler alert, you'll want both.
Will
UberDork
10/24/22 7:43 p.m.
I roll my eyes at the Navy SEAL-esque naming conventions, but at the same time it's fairly brilliant marketing.
I am not a fan, at least where I work. It just does not apply.
When I went to class I signed my name on the roster and tossed the pen into the trash in front of the instructor. Told him I'd not need it for a bit so it was not worth keeping in my inventory. He was not terribly impressed.
I went through it when I worked for a manufacturing company years ago.
It might look good on a resume, but in reality, it was common sense stuff that folks like us already know.
I hate to say it but probably not even relevant anymore. Unfortunately quality "fixes" come and go like all trends. Personally I found the Deming view of quality and customer satisfaction to be the best for my career. But I didn't preach it or force on others. Just used it as my personal coach.
So... this thread is 2 years old...
I'm not job hunting anymore.
If I end up job hunting again and they ask me if I understand things like "Kanban" and whatnot, I could honestly say, "Yes. Better than you do, if you're asking me if I understand it. Because anyone who has actually studied these methods know that they were designed for specific companies with unique cultures and situations. That any functional company will have its own unique system that I will only truly understand by actually working within their process flow."
Although I doubt an HR drone would appreciate being told they don't know what they're talking about.
Gary
PowerDork
12/26/24 9:17 p.m.
In reply to Beer Baron ๐บ :
Annie and I worked in corporate America. We recognized that this was just another BS money-making program as it was being implemented into our company. We played the game but continued to do our jobs the best we knew how to do. It's just BS but it seems that the ISO culture has gained control over corporate America. Hire good people and you don't need it. "Root cause" be damned. Good people on the job never let the root cause happen in the first place.
They make sense within a large company. Mega corp x may embrace Lean or Agile or whatever to ensure consistency across the organization. Sure most of the steps within are common sense, but it applying them in a consistent manner is far more likely to be effective. For continuous improvement to be effective it must be driven from the top, and in order to do that you need to communicate it down via some standard language.
I work at a megacorp that has put together bits and pieces of a few to created their own system, but it's basically the same stuff.
Experience with ANY of them should transfer to another corp even if they use a different process.
@BeerBaron I'm sure if you had to job hunt again you could phrase your statement in a little more friendly way and it would go over just fine :)
TravisTheHuman said:
@BeerBaron I'm sure if you had to job hunt again you could phrase your statement in a little more friendly way and it would go over just fine :)
Yeah. I was being slightly facetious. I wouldn't phrase it like that. That's just what my inner monologue would be.
What you said about top-down consistent procedures is right. I roll my eyes because those things get *called* "Lean" or "Agile" or "Kanban" or whatever, but almost never actually *are* what they're called. That every company ends up creating its own unique system.
In reply to Gary :
It's not just hire good people, it's making sure the managers enforced all of the design guides and processes that have been put in place over time. I came from both ISO and 6 sigma as reasons to get away with not doing it. Ironically, ISO is just "Say what you do, do what you say" with proof. It's amazing we put so much training in that.
The number of times we saw clear warranty problems when people dropped a step in the process or managers didn't require specific tests that would have changed things or whatever- it's astounding. It costs F more than one billion a year, all to get things done "on time" as opposed to right.
I'm so glad I'm done.
Peabody
MegaDork
12/27/24 10:23 a.m.
Gary said:
Annie and I worked in corporate America. We recognized that this was just another BS money-making program as it was being implemented into our company. We played the game but continued to do our jobs the best we knew how to do. It's just BS but it seems that the ISO culture has gained control over corporate America. Hire good people and you don't need it. "Root cause" be damned. Good people on the job never let the root cause happen in the first place.
And you see, that 's the problem. It's precisely the opposite of what you said. These systems and protocols work very, very well and are huge cost savers - if everybody buys in.
I worked in automotive almost my entire career, and in every company, even the non-automotive ones, these kind of programs were introduced. We were trained, they were implemented, and promptly ignored. That's why they don't work, and end being very costly exercises due to both the efforts involved in the implementation, and the losses incurred by not following the protocols.
When management allows people to skip a step, or ignore protocol, it costs companies billions.
I used to roll my eyes whenever these 'new' programs were preached, we'd go through all the training and implementation, only to completely ignore it and go back to doing things like we always had within a few months. A couple years later we'd go through it again.
In reply to Peabody :
All these things are just codified common sense. The problem is how often people don't want to use common sense.
A person who recognizes and uses common sense doesn't need fancy TLA training, and TLA training does no good if people refuse to follow common sense.
I got frustrated because I've not been formally trained in specific TLA systems, but I understand the importance of having clearly defined best practice systems and following them. I'm also probably going to do a better job than other people who follow them to the letter, because I'm smart enough to understand the reasoning *behind* the methodology and be able to adapt to novel problems or adjust processes to make them more efficient.
But no certification will ever be able to show that.
In reply to Peabody :
It's not the systems that are the problem, it's the management. As far as I could tell, there were systems in place already that made the "new" programs very redundant and and sometimes less effective. But many of the original systems were overlooked due to cost and/or time. So every one already knew that the new systems would be ignored when the time came that they were needed the most.
Even worse when a year or two later, those instances where the current process was ignored came back to bite in multi billion dollar recalls and warranty costs. And no leader in the company would bother to connect the dots. I am not aware of any significant problem that would not have been dealt with if all systems were enforced. The cost of saving millions were billions.
Basically, every single worker saw the new systems as a waste of time and money because the cost and time in training would be ignored at the first time where program cost and/or time were at risk. So why bother paying attention to these new things when the old things were already regularly ignored?
Peabody
MegaDork
12/27/24 10:56 a.m.
alfadriver said:
In reply to Peabody :
It's not the systems that are the problem, it's the management.
Basically, every single worker saw the new systems as a waste of time and money because the cost and time in training would be ignored at the first time where program cost and/or time were at risk. So why bother paying attention to these new things when the old things were already regularly ignored?
I'm pretty sure that's what I said.
And like BB said, these systems are really just common sense. But since you can't teach common sense, and many people just don't have it, you are given standardized rules and procedures to follow that will replicate a common sense decision.
In reply to Peabody :
You mention that everyone needs to buy in, and then later point out managers. As far as I can see, it should be the other way. Managers build the processes and controls in as a culture, and the everyone just does it automatically.
Managers are the key. They need to hold their teams accountable and support the processes. They also flow down the targets/goals accordingly.
Beer Baron ๐บ said:
In reply to Peabody :
All these things are just codified common sense. The problem is how often people don't want to use common sense.
A person who recognizes and uses common sense doesn't need fancy TLA training, and TLA training does no good if people refuse to follow common sense.
I got frustrated because I've not been formally trained in specific TLA systems, but I understand the importance of having clearly defined best practice systems and following them. I'm also probably going to do a better job than other people who follow them to the letter, because I'm smart enough to understand the reasoning *behind* the methodology and be able to adapt to novel problems or adjust processes to make them more efficient.
But no certification will ever be able to show that.
It's common sense if you have done it enough times and know what needs to be done. The problem is when there is people churn and it's no longer common sense. Or that someone see is so easy that they skip something.
It's actually a part of The Martian that I really appreciate when the management intentionally skips checks for time reasons and gets burnt. But I bet people don't see it as a management failure.
Beer Baron ๐บ said:
In reply to Peabody :
All these things are just codified common sense. The problem is how often people don't want to use common sense.
A person who recognizes and uses common sense doesn't need fancy TLA training, and TLA training does no good if people refuse to follow common sense.
I got frustrated because I've not been formally trained in specific TLA systems, but I understand the importance of having clearly defined best practice systems and following them. I'm also probably going to do a better job than other people who follow them to the letter, because I'm smart enough to understand the reasoning *behind* the methodology and be able to adapt to novel problems or adjust processes to make them more efficient.
But no certification will ever be able to show that.
It's common sense if you have done it enough times and know what needs to be done. The problem is when there is people churn and it's no longer common sense. Or that someone see is so easy that they skip something.
It's actually a part of The Martian that I really appreciate when the management intentionally skips checks for time reasons and gets burnt. But I bet people don't see it as a management failure.