Anyone ever built a retaining wall? I need to build one about 50'x6'. I was thinking to do it in terraces. One 3' high set back 3-4 feet then another 3' made out of Sackreet/ Quickrete. Just lay the sacks end to end in a staggered run and then hose them down and let them set up. I could run rebar thru them to help tie them together.
Most cement plants are producing huge concrete Lego blocks that are ideal for walls and pretty competitively priced. Sacks of quickrete will never be close to cost effective on that scale. Even cinder blocks will cost less.
How big are the "Lego" blocks?
Depends on the plant, usually about 18" tall and thick, and 3-4' long. You would have to call your local place and see which molds the are using.
You might need to check about railing and the law where you live, sometimes the height of a wall required a rail and if it does where you live they will be able to tell you how far the second wall needs to set back from the first.
How much are you holding back and how tall do they have to be? Reason I ask, if it's a big wall you'll need to add French drains and drain pipes. Otherwise, the first big rain will really mess up all your hard work!
Also, the curve of the wall is important. If the center of the wall bows out, it won't be very strong. Like this:
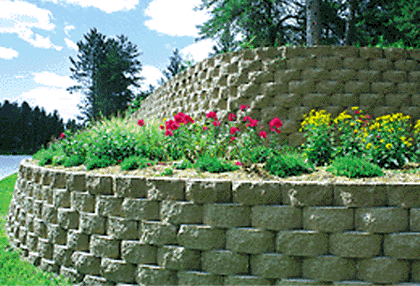
It's done all the time in sorta light duty applications.
It might work in your case. If the center of the wall bows in, that adds tremendous strength, since concrete blocks are hard to compress. Like this:
<img
Any retaining wall over 36" in my area needs a building permit. Be carefull.
SVreX
SuperDork
8/3/08 10:48 p.m.
What are you retaining?
The soil type, water content, drainage, proximity to structures, shape of the wall, aspect ratio of the grade differential, plantings, all have a lot to do with the strength of the wall.
6' tall is high enough that you need to be thinking this one through.
Sakrete bags are probably not a good idea on this one.
Example: a straight wall, with 2 terraces, built out of sakrete like you described holding back moist soil with minimal plantings and a building above it 10' away from the wall which drains water toward the wall- won't last through the first rainfall.
a serpentine curved wall with 2 terraces and integrated tie backs with sandy soil and gravel draining through weepholes, lots of plantings and greenscaping, with the top level hardscape draining water away from the terrace built of interlocking blocks with no structure footings nearby- sounds great.
I have the need for a retaining wall myself and simply haven't found a cost effective way to do it so far. I would be very interested in a way that a layman can DIY.
In my situation I have the right shape, bowed in not out, and roughly porksboy's length and width. I will need drainage, but that's easy.
Those Lego blocks are expensive as HELL! Prep work before you can begin to lay those blocks is almost as expensive as other complete walls.
Don't even think about going to Home Depot or Lowes for their trapezoidal blocks since they are roughly $3 apiece and are only about 3" x 9". As Jimmy Durante once said " You'd need a million of um" Dollars he means!
I have been running into costs of tens of thousands which is more than I can spend by about an order of ten.
Yup, walls are expensive. We had a 40' by 2.5' wall installed in our yard last year. Concrete block on a cement foundation, drainage, and faced with natural stone. Along with a 30x15' stone patio, the cost was well into the tens of thousands of dollars. And it was worth every penny.
Make sure you tie the wall into the ground behind it. Put bars perpendicular to the wall, buried within the dirt. This keeps the wall from rocking forward over time.
Jersey barriers pretty enough? 
Duke
Dork
8/4/08 8:57 a.m.
Retaining walls are expensive because they are a PITA to do right. You can do it right, or you can do it several times, and never have it be particularly good even when it hasn't failed. Look around and see how many failing retaining walls you see - lots of 'em.
6 feet is not a particularly low retaining wall, either. You're smart to do it in terraces. Something like this should work. You want an interlocking block that is battered back at a slight angle.
You also want to tie it back with rebar to a series of small footings placed a few feet back inside the earth to be retained. Last but not least, backfill most of the area behind the wall with gravel, and put short lengths of 3" PVC pipes through the wall about every 6 to 8 feet to allow drainage to relieve the hydrostatic pressure. Put geotextile filter cloth over the buried ends of the pipes to stop them silting up.
I need to replace a wall that tapers from 2' to 8' over it's 50' length. It is stacked railroad ties. What I'm considering is 2-3 terraces, poured concrete with a flagstone face. I would pour the walls to include rebar reinforced outriggers that get buried, thus the weight of the dirt is helping to keep the wall upright. I think I want to build the new walls on the downhill side of the current wall, then demo the current wall and use it as backfill.
This would give the yard more character, eliminate an 8' drop, and give some natural places for nice planting beds.
I'm not looking forward to the cost...
Duke
Dork
8/4/08 9:10 a.m.
I'm not a big fan of poured concrete retaining walls unless you have no other choice. They are strong in and of themselves but they can fail where they join the footing, and that's where they really need the strength. It does no good to have a nice flat strong wall that is tipping over because it failed at the knuckle where it sits on the footing.
Battered walls that slope back at ~5 degrees are stronger in the long run and if they are interlocking, loose-laid masonry, they can be much easier to fix if you have localized problems.
We're putting one in on the project I'm currently on (coughCarMaxcough) and while it's only ~7' high at the highest point it had to be designed by a structural engineer and stamped. It uses GeoGrid for the tie-back material rather than rebar, at a 1:1 ratio (7' high = 7' back).
In rough numbers the wall is about 1200 S.F. (150' long total) and $45,000 or so. This is a commercial grade engineered wall using Allan Block "AB Classic" (http://www.allanblock.com/RetainingWalls/Literature/Homeowner/literature.aspx?ta=2 ) and StrataGrid (http://www.geogrid.com/products_sg.html ) and installed by a professional landscaping/retaining wall company.
A wall is only as good as its base. It must be compacted and stable. Your best bet may be to do a poured footing with rebar uprights. Depending on what you are holding back, you will need to tie back into the hill. Then just build a wall with concrete block. be sure to provide adequate drainage. pVC pipe in fabric can work. I would terrace it, for strength and appearance. I would consider this as a grassroots approach, you could spend much more.
Our 2'-7' high wall simply sits on a 6" compacted gravel (304's) leveling pad - no concrete or rebar, just the geogrid material which is laid inbetween every 3rd course or so. But if you don't have an engineer designing your wall then maybe concrete and rebar would be a good idea.... 
45 grand sitting on gravel? What's the profit margin on that job?
SVreX
SuperDork
8/5/08 6:47 p.m.
Duke wrote:
I'm not a big fan of poured concrete retaining walls unless you have no other choice. They are strong in and of themselves but they can fail where they join the footing, and that's where they really need the strength. It does no good to have a nice flat strong wall that is tipping over because it failed at the knuckle where it sits on the footing.
Battered walls that slope back at ~5 degrees are stronger in the long run and if they are interlocking, loose-laid masonry, they can be much easier to fix if you have localized problems.
They won't fall over if they are properly tied to the footing, and braced back into the bank.
Poorly and improperly constructed things will always fail, regardless of the material. It does no good to use really strong components, if you've no idea how to use them.
SVreX wrote:
Duke wrote:
I'm not a big fan of poured concrete retaining walls unless you have no other choice. They are strong in and of themselves but they can fail where they join the footing, and that's where they really need the strength. It does no good to have a nice flat strong wall that is tipping over because it failed at the knuckle where it sits on the footing.
Battered walls that slope back at ~5 degrees are stronger in the long run and if they are interlocking, loose-laid masonry, they can be much easier to fix if you have localized problems.
They won't fall over if they are properly tied to the footing, and braced back into the bank.
Poorly and improperly constructed things will always fail, regardless of the material. It does no good to use really strong components, if you've no idea how to use them.
Amen, brotha. It's much better to go do the homework up front- or hire an engineer if you aren't sure- than to screw up really really bad and have to do the whole frickin' thing two times.
They won't fall over if they are properly tied to the footing, and braced back into the bank.
Poorly and improperly constructed things will always fail, regardless of the material. It does no good to use really strong components, if you've no idea how to use them.
So Paul - what do you think of my plan? The outriggers I described I think ar what you meant by "braced back into the bank".
Is it necessary to pour a seperate footing and wall, or can I just excevate 12-18" below grade and build the forms inside the ditch, such that on the downhill side there is 12-18" of wall below grade and on the uphill side is the buried outriggers?
Duke
Dork
8/6/08 11:23 a.m.
SVreX wrote:
They won't fall over if they are properly tied to the footing, and braced back into the bank.
Poorly and improperly constructed things will always fail, regardless of the material. It does no good to use really strong components, if you've no idea how to use them.
Agreed, and I've found in my experience that the amount of understanding about how to design the bending-moment knuckle that a cast-in-place retaining wall requires to cantilever off the footing is sometimes a little slim, and the prep work required to make one properly is also complicated.
That's why I recommended a masonry retaining wall - usually cheaper and easier to build in a low height.
Duke
Dork
8/6/08 11:37 a.m.
DILYSI Dave wrote:
So Paul - what do you think of my plan? The outriggers I described I think ar what you meant by "braced back into the bank".
Is it necessary to pour a seperate footing and wall, or can I just excevate 12-18" below grade and build the forms inside the ditch, such that on the downhill side there is 12-18" of wall below grade and on the uphill side is the buried outriggers?
I realize you're not talking to me directly, but you'll need more than 12"-18" below grade if you live somewhere with any kind of winter. In the Mid-atlantic region 32" below grade is considered adequate. Also, you'll want a separate footing that is wider than a typical house footing, extending farther back into the uphill side and with a small underhang on the downhill side. There should be rebar in the footing (both directions) that also turns up into the vertical portion of the wall.
Pour the footing first and press a 2x4 into it (wide face down) when it is wet. This creates a key that the vertical portion of the wall pours into to help stop it from getting pushed off the footing by the pressure behind it.
Click here for a PDF on retaining walls.
Concrete walls start on page 15.
SVreX
SuperDork
8/6/08 5:46 p.m.
He lives in ATL, so freeze is not a real issue. 12"-18" is more than adequate.
DILYSI: I basically like your idea, though please understand that I certainly can't give engineering advice over the internet.
Your outriggers idea is right in theory. In practice, they could be a royal pain to form.
Duke's idea of the offset footing is an interesting one. The footing would essentially be the outriggers. I think I'd try it in 1 pour, however. The footings and stem wall could be pouted at the same time as a monolithic pour, but the formwork would be rough.
What I dislike the most is that neither of you said anything about drainage, which is probably the most important part. The walls should include good sized drains (maybe 3" PVC) at the bottom to allow water to escape that builds up behind them. These drains are called weepholes. The wall should then be backfilled with gravel to allow the water to migrate to the drains. Top off the gravel with landscape cloth to prevent the gravel from clogging with soil and silt, then a few inches of topsoil on top of that.
The wall will not hold back the hydraulic pressure if water builds up against the back of it. If you don't plan for the water, the wall could fail.
Also, regarding the rubble of the old wall, I don't mind you burying it, but don't mix it with your drainage gravel, and don't leave all those big pieces in a big underground pile. They won't contribute to your drainage system, and they won't compact well. They should be mixed in with your fill.
You also didn't address the thickness of the wall. I'm not going to answer that one, because it is an engineering question. I'll just say that it is not 4" thick. It is also not 6" thick.
SVreX
SuperDork
8/6/08 5:53 p.m.
Oh, one other thing. If you pour the footings separate from the wall, the 2x4 thing Duke suggested is nice in theory, pretty rough in real life. It's much more practical to run re-bar vertically sticking out of the footing.