I took advantage of having a wide open weekend.
Overall, I like these Mishimoto v-bands a lot better than the junk I was using before. Check it out! No clearancing needed for that number 6 plug. The v-band spaced the pipe perfectly.
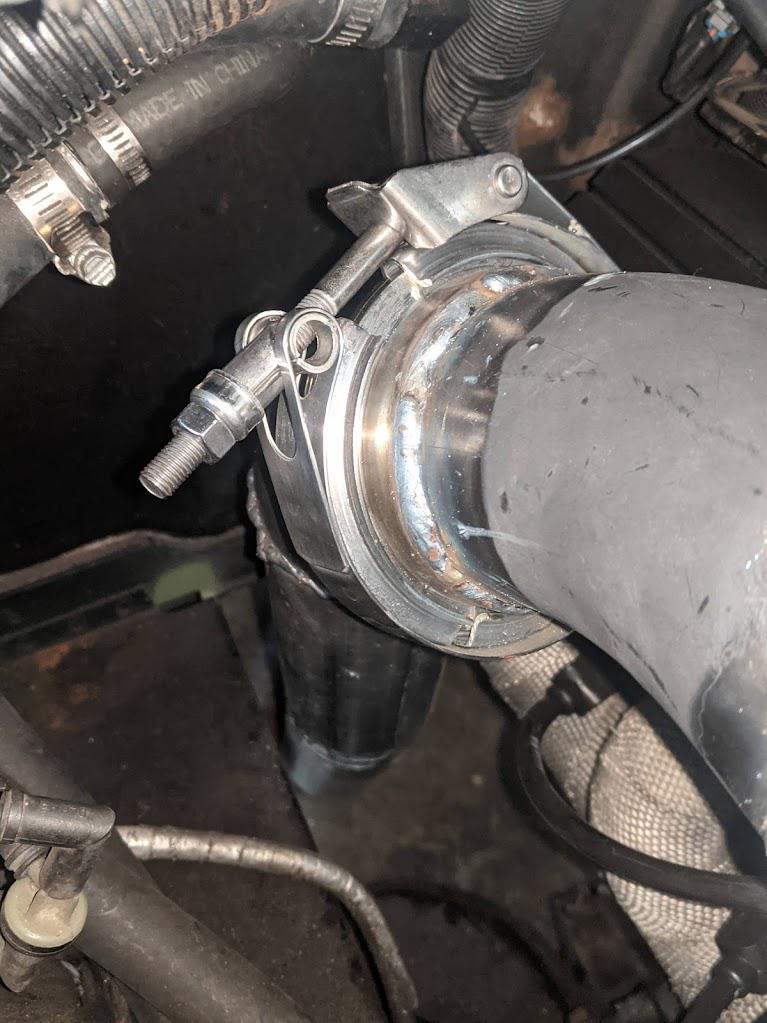
I added a little bend in the middle to smooth out the lower bend to the intermediate pipe.
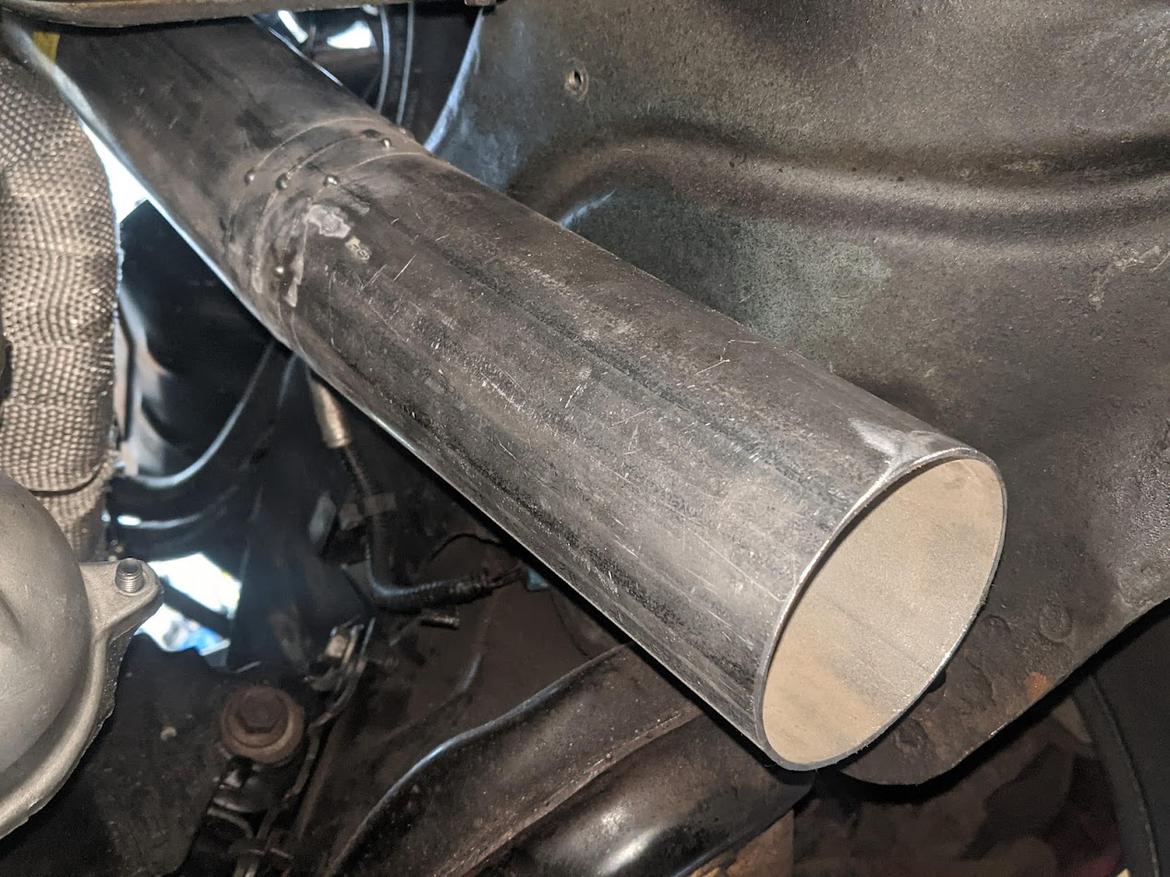
However my only method of making okay bends out of straight pipe is the slice it with the saw enough to bend it by hand and weld it back together. My abrasive chop saw makes a wide kerf but also a big mess out of the pipe and my garage. I would love an actual blade, but that would require a much nicer saw. Maybe some day. Until then, I have to put the grinding stone on my Dremel extension and chip away at these huge burs. It doesn't take long. They're super thin, but still annoying.
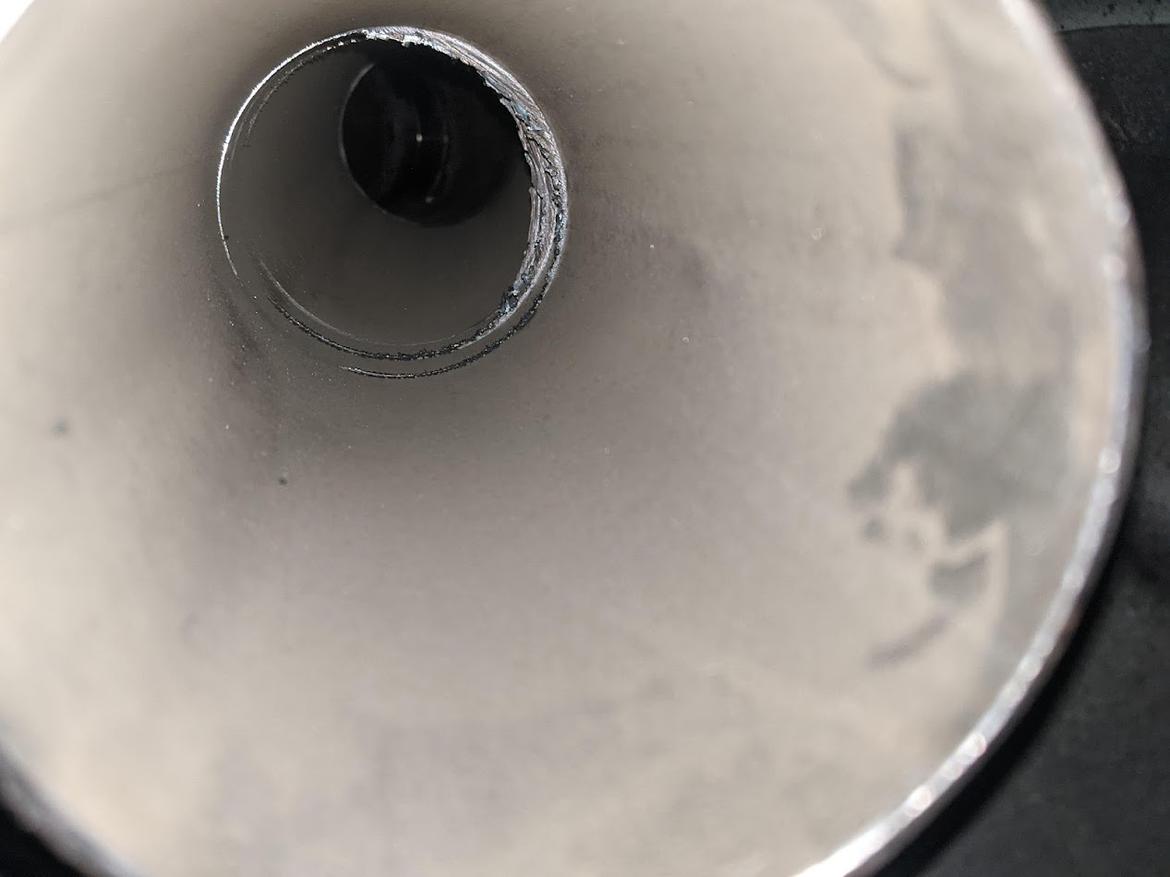
From there I was able to get a good idea of how the intermediate pipe was going to be built. I'm putting a v-band between it and the down pipe, a Z to the 4" system with an adapter and band clamp. There will also be a hanger under the passenger floor board once the plumbing is finalized. I'm not going to bore you too much with progress on this because its hard to get good pictures, and it's not all that exciting anyway. Just know that it will be done soon.
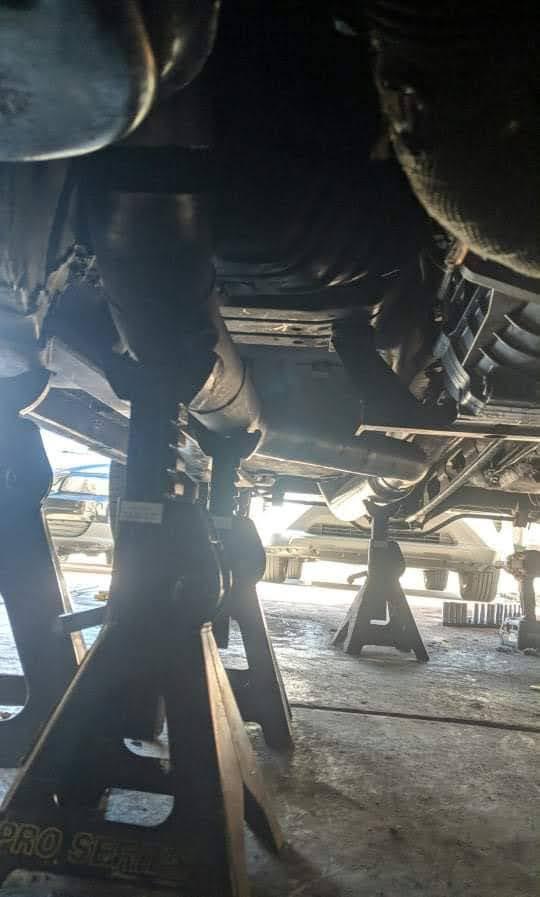
Ever used seven jack stands on one car? lol
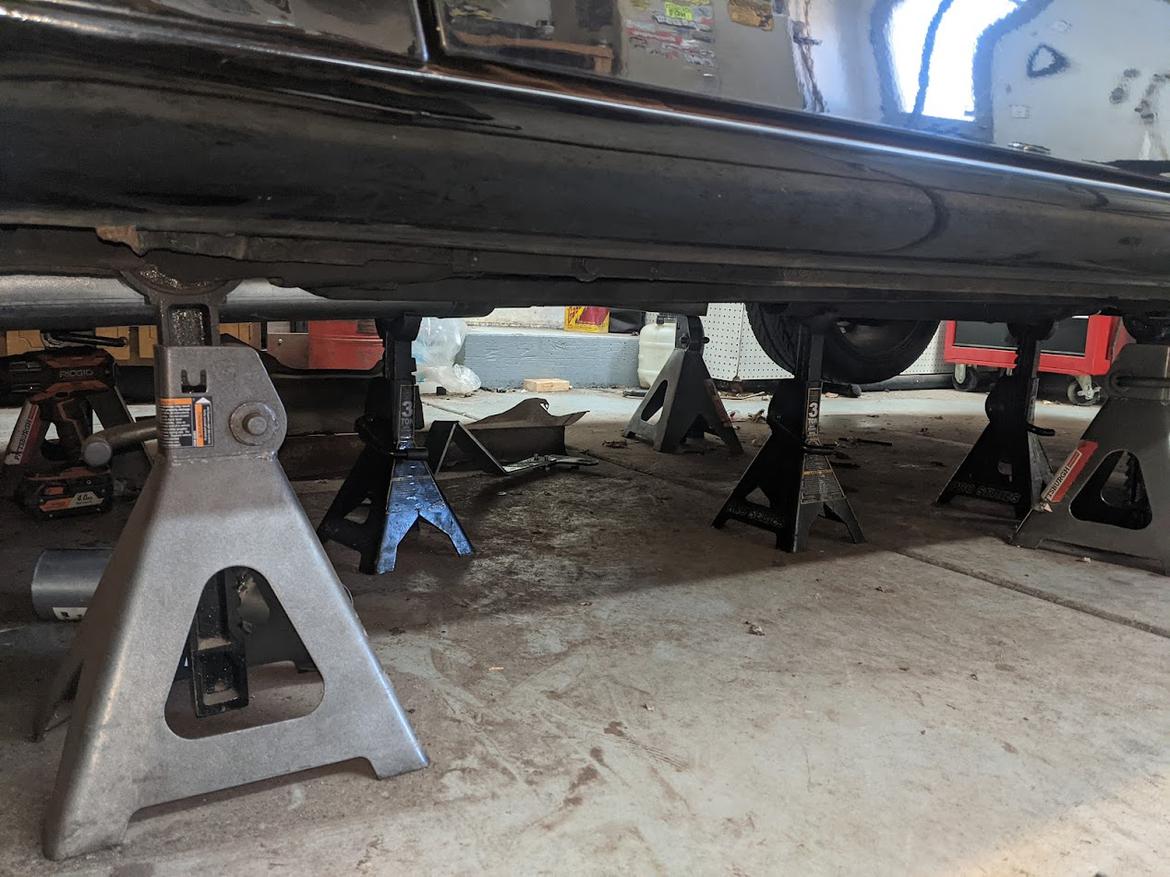
Once I got stuck waiting for parts again, I decided to pull the downpipe off again, weld on the O2 bung, and tease myself a bit with (nearly) final form views. I am so in love with how this thing looks.
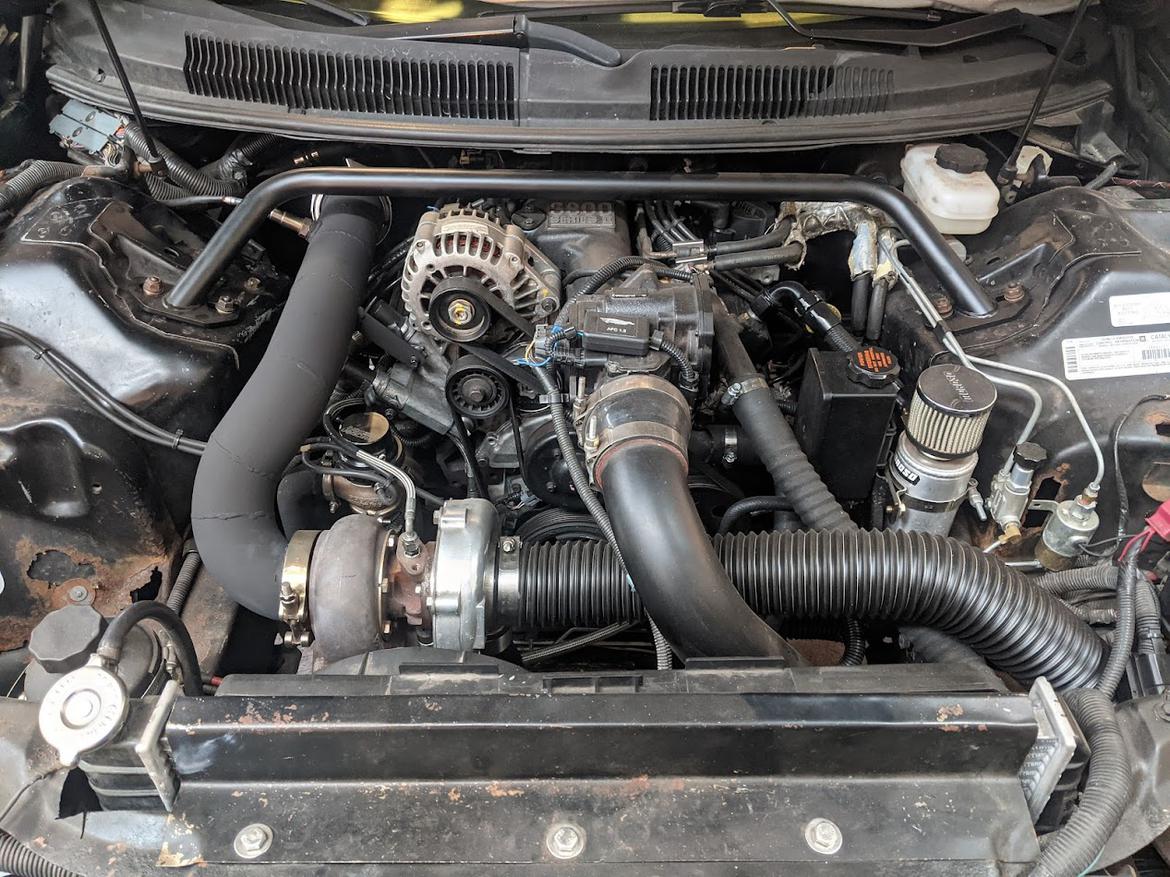
I ordered some parts that should be here this afternoon, but I was still motivated to continue progress. Did I mention that I bought a Lakewood driveshaft mount/tunnel brace? Well I did. I don't have pictures of it, but it's basically a very ugly bent up piece of zinc plated steel with a lot of bolts in it for easy removal. The mofo about it is that it mounts to the factory tunnel brace brace mounts which I cut out of the car years ago during floor repairs and never replaced. Now I get to make them. Ireally just hope that I can get away with welding them in without removing the carpet or setting it on fire.
I'm starting on the driver side because I know exactly where the original mount used to be. It was integrated into the end of the frame channel.
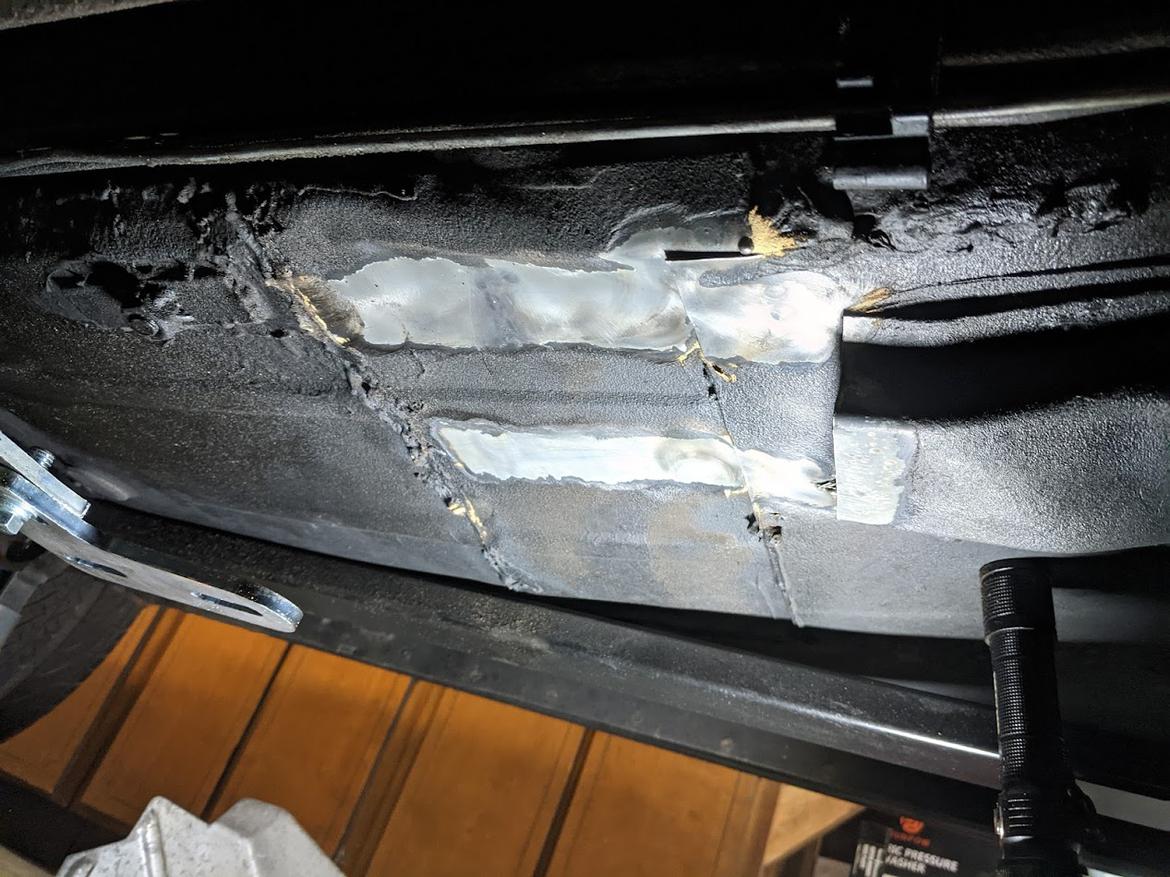
I bent this piece out of some scrap. It fits flawlessly!
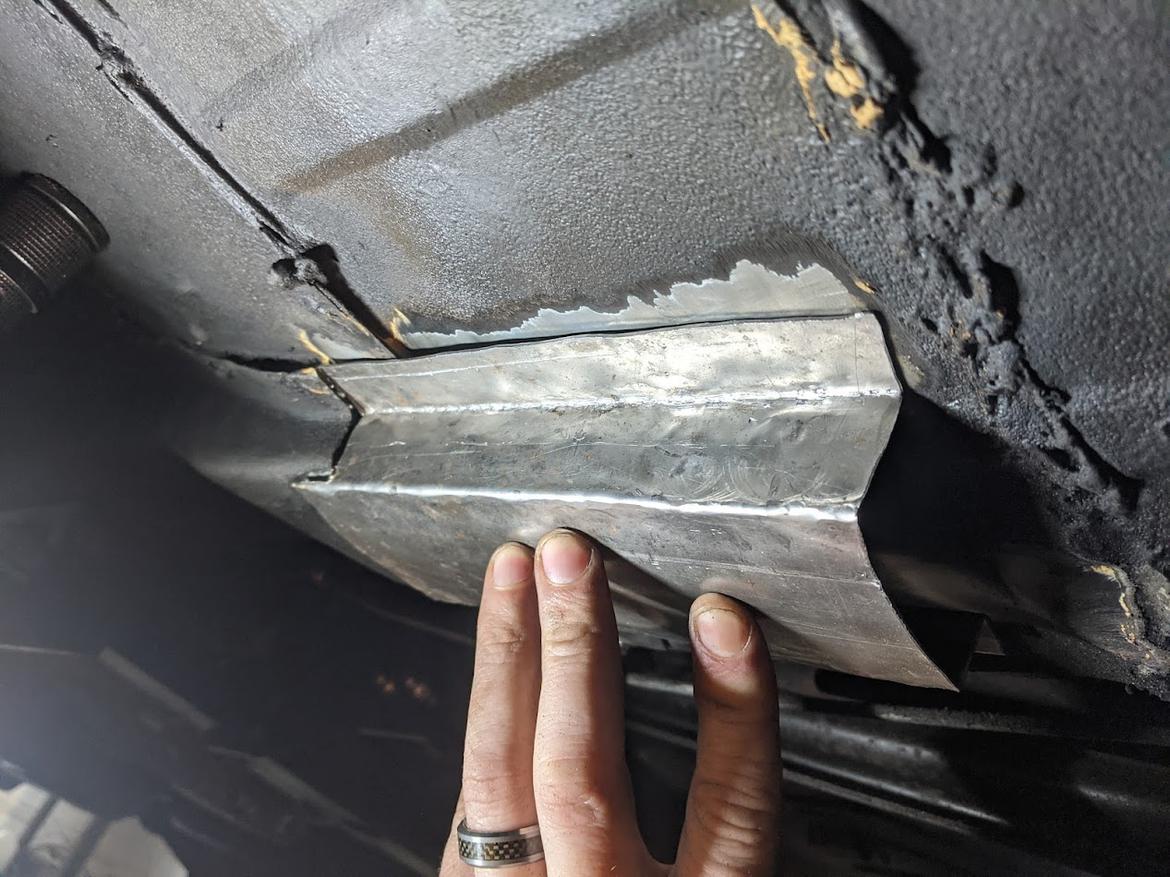
Then I roughly mocked everything up and determined about where my bolt holes needed to go. The loop has some big slots in it to account for variance, so I don't really even need to get close.
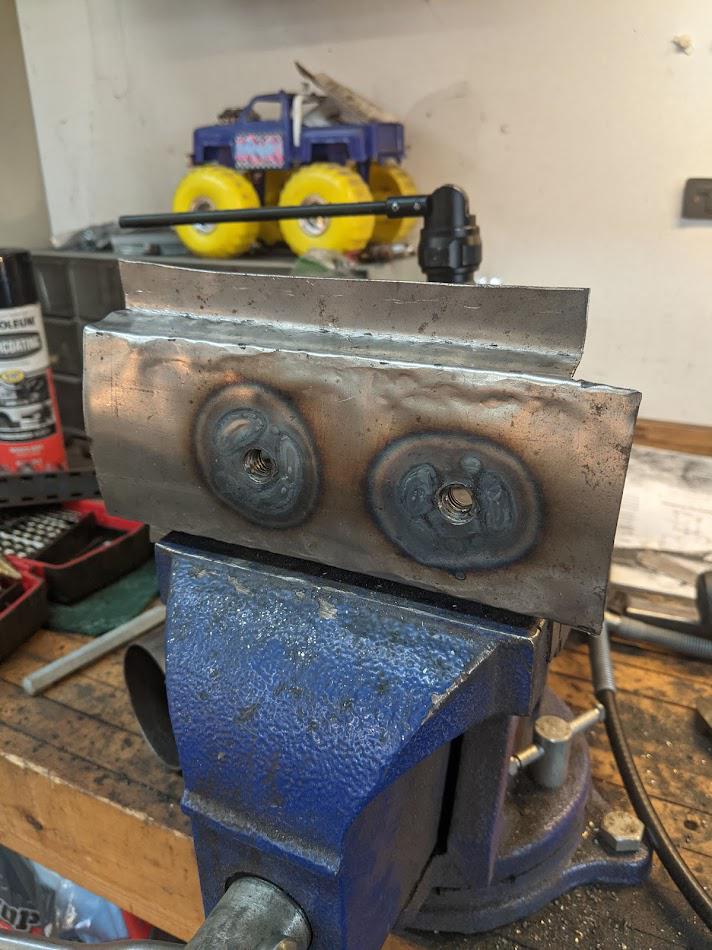
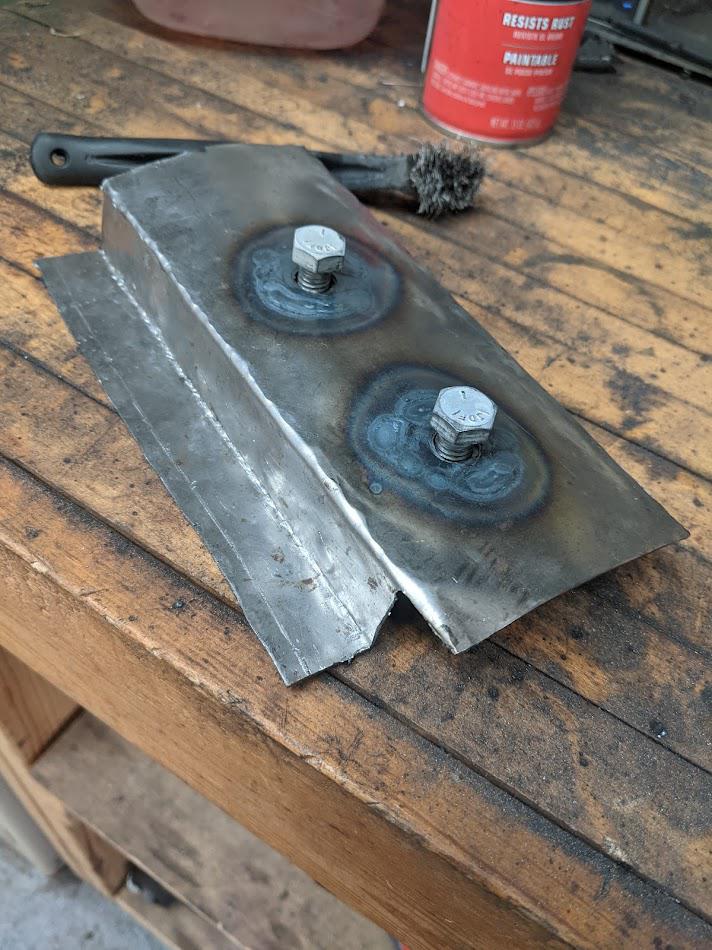
I'm not looking forward to welding this overhead on the floor, but no pain no gain. Right?