Today I finished up the throttle cable brackets. When I reversed the TB cam to make cable pull down and forward vs OE C4 up and back, I made the cable pull down and a little bit back, instead of mimicking the angle from the C4. So instead of having max leverage only for a few degrees before beginning to get harder, it had max leverage for about 45 degrees. This gave very little force feedback through the gas pedal, and made tip-in smoothness unpossible. Was:
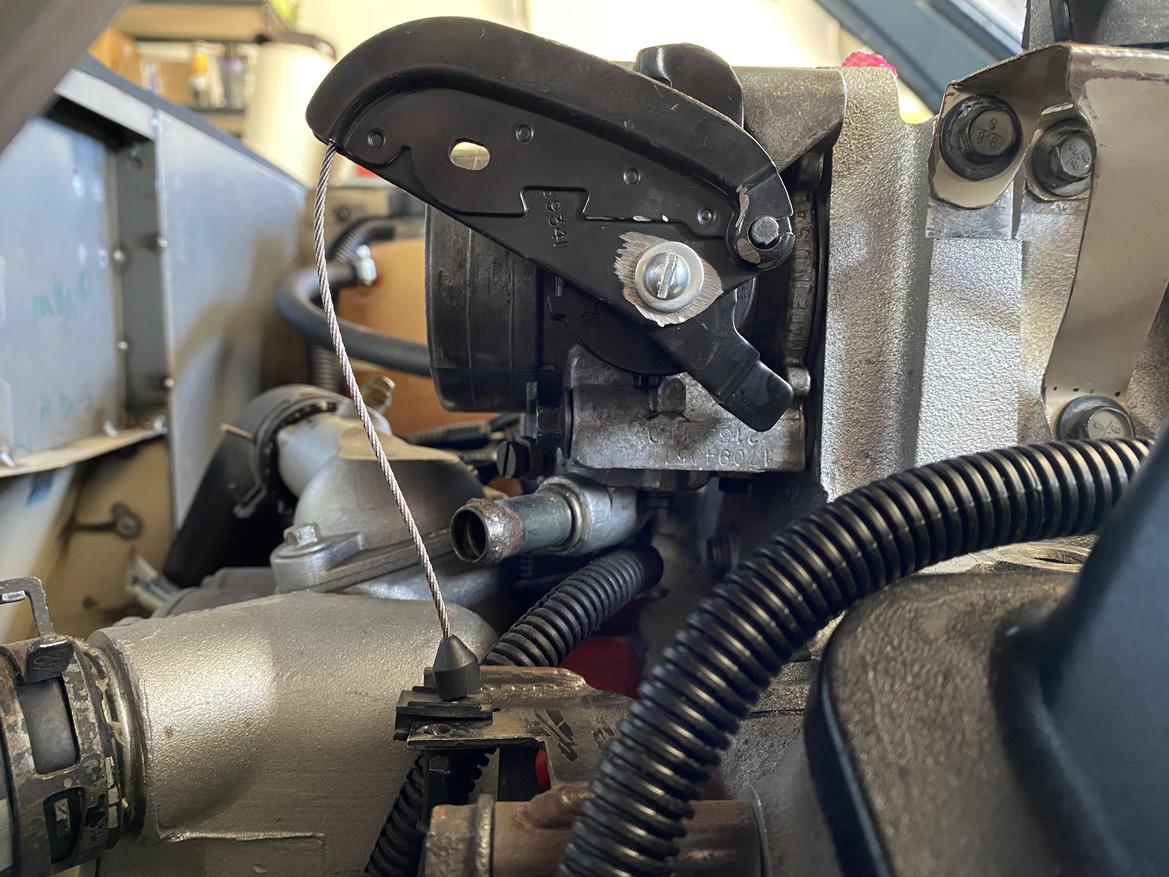
So I moved the housing attachment up and forward, so now the cable angle coming off the TB cam is pretty close to what it was on the C4. These changes made the bracket very floppy, and I could see it bending as it approached WOT. Interim config:
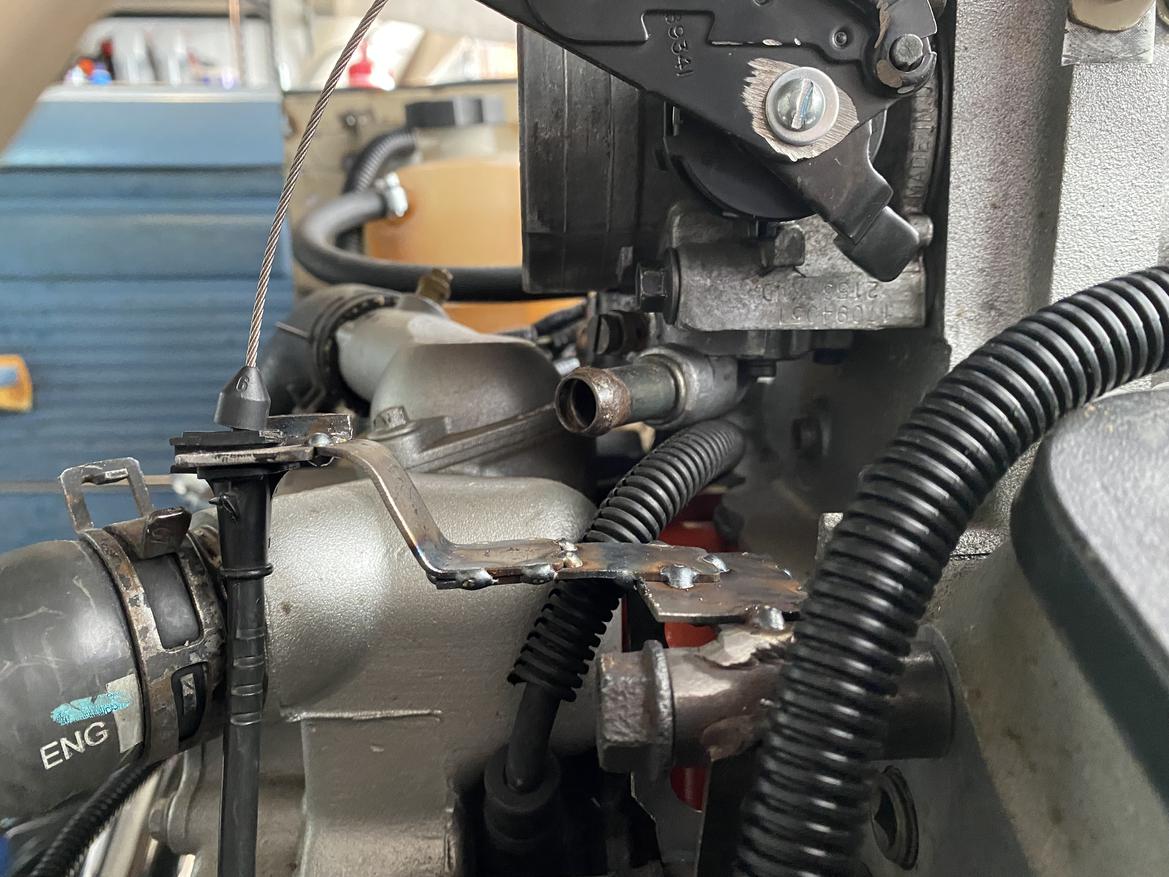
so I fired up the CAD and added a stiffener:
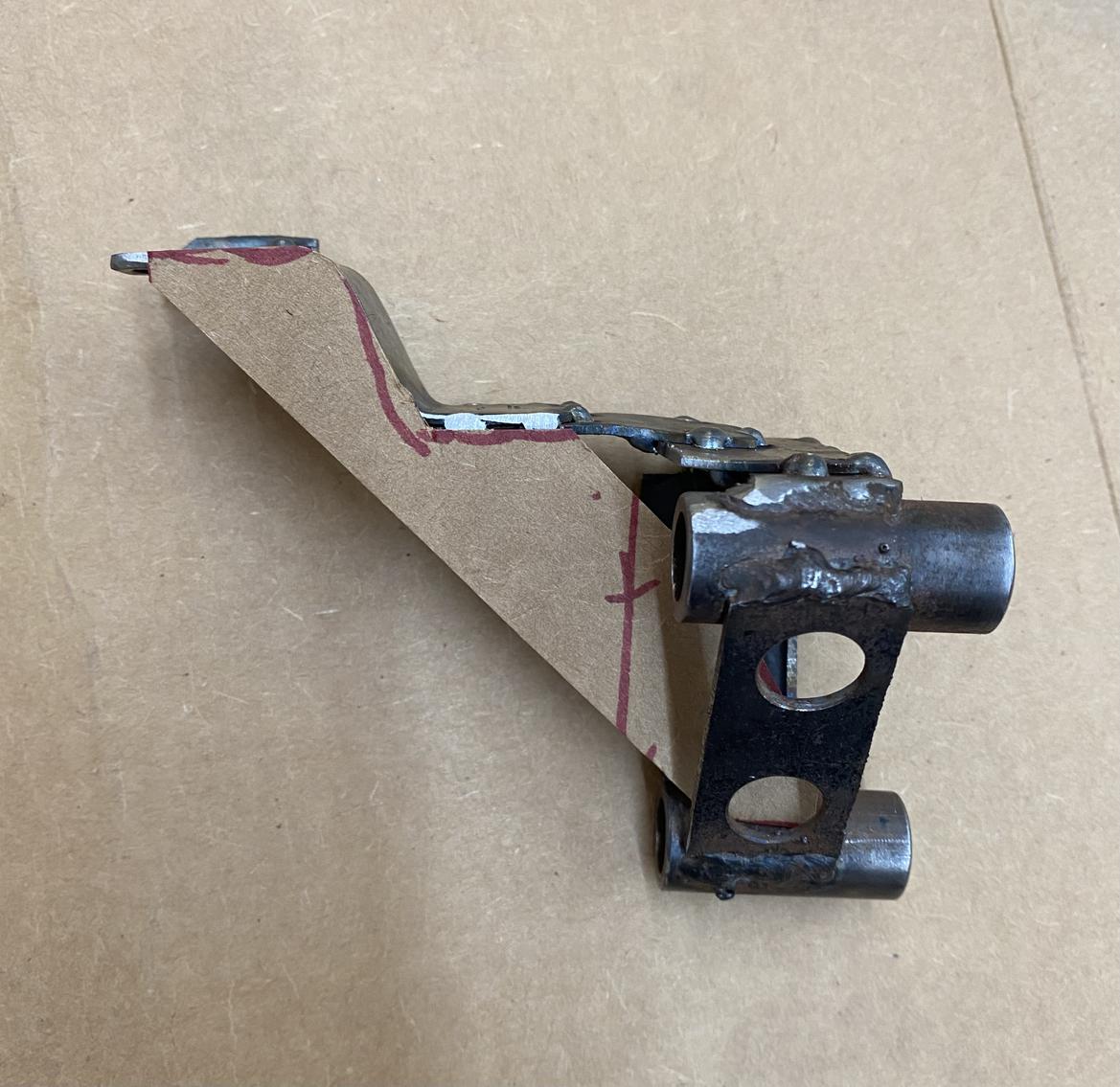
and now it is, as my Dad would have said, stiffer than a honeymoon dick:
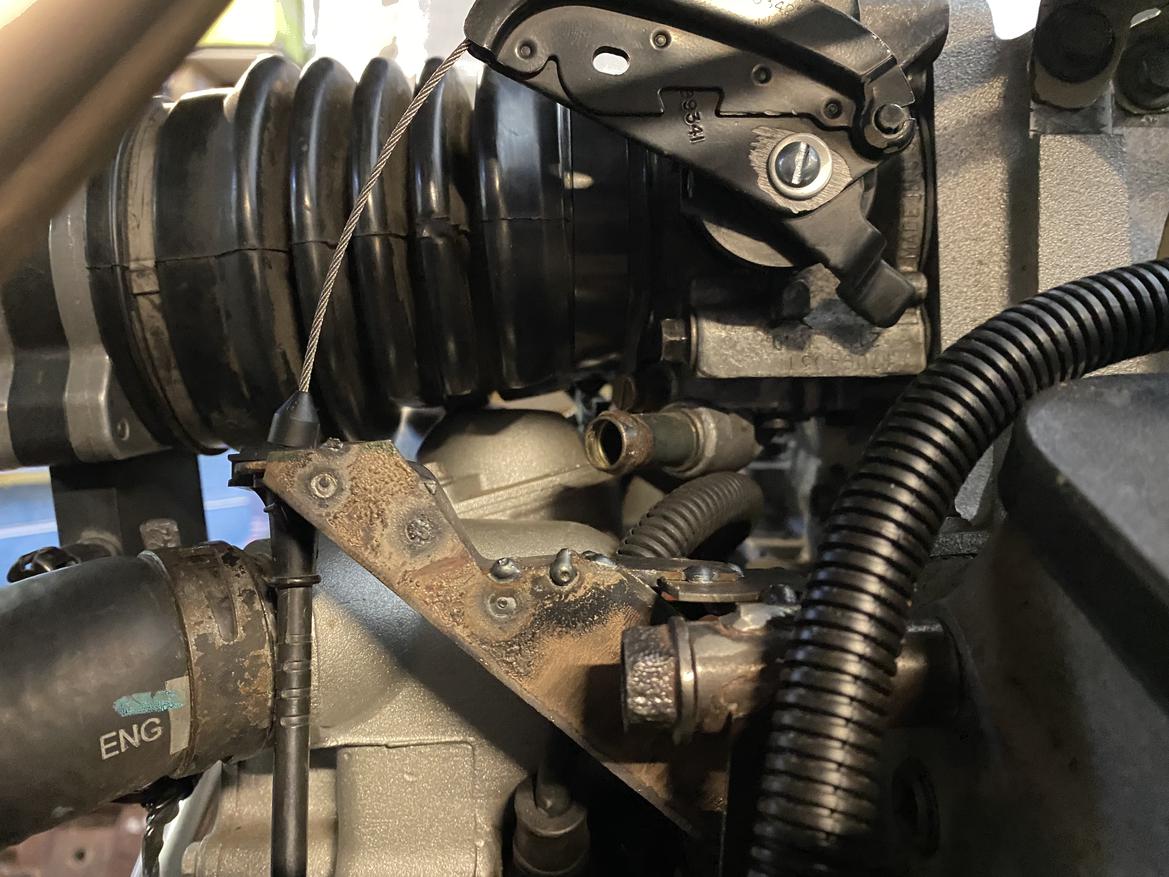
Under the car, I made two changes to the bellcrank. First I made the cable attachment more robust, by basically hacking together a copy of the attachment at the TB cam. How, you might ask? First I measured stuff. Cable end diameter is about 0.230". Cable diameter is about 0.060". Then I clamped two pieces of 14ga together and drilled a 1/4" hole through them. Then I cut a slot in one of them, 180 degrees from the direction the cable will pull as installed. Then I slipped a piece of 16ga between them and tacked the sandwich together. Here's a few pix:
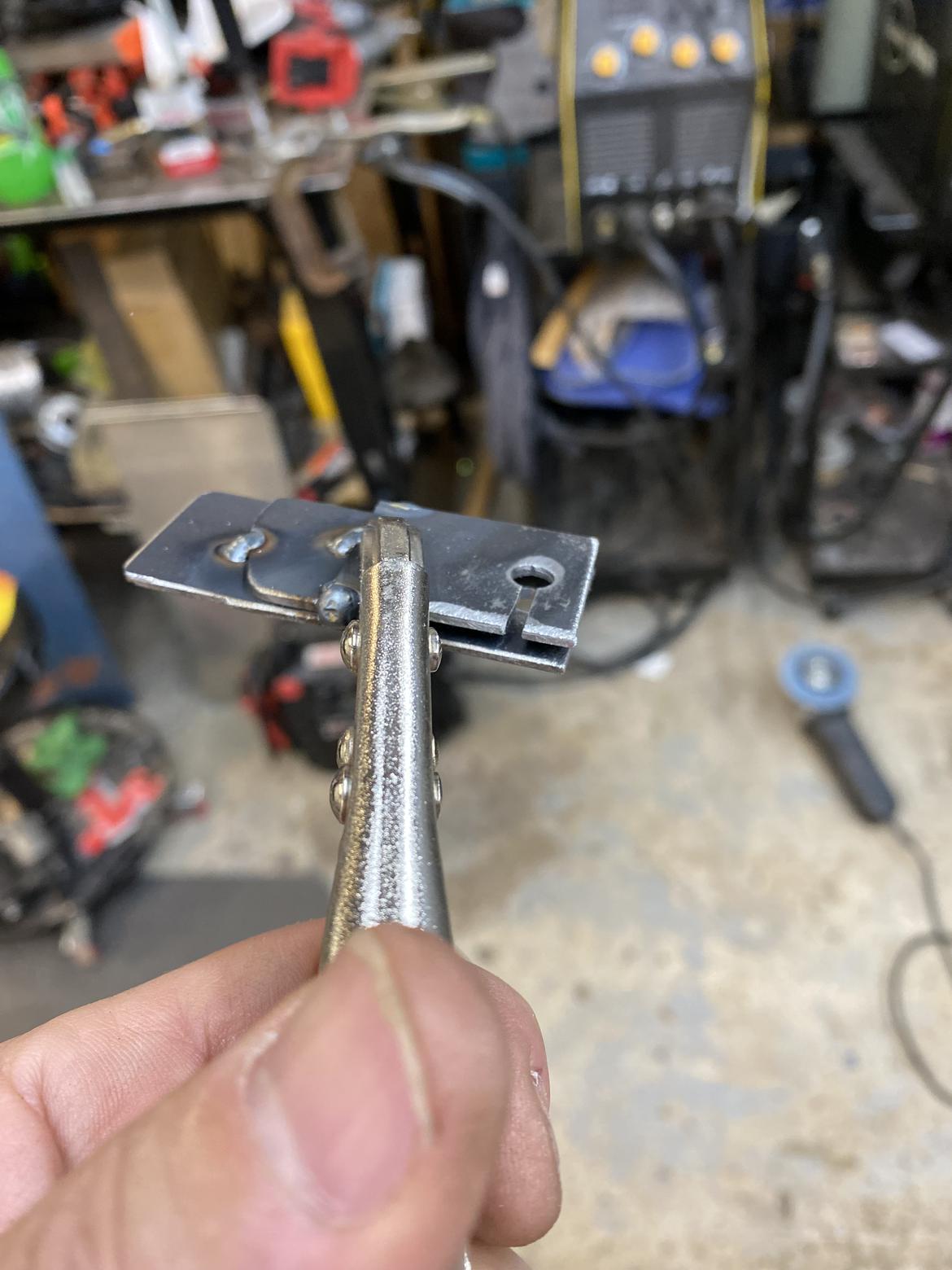
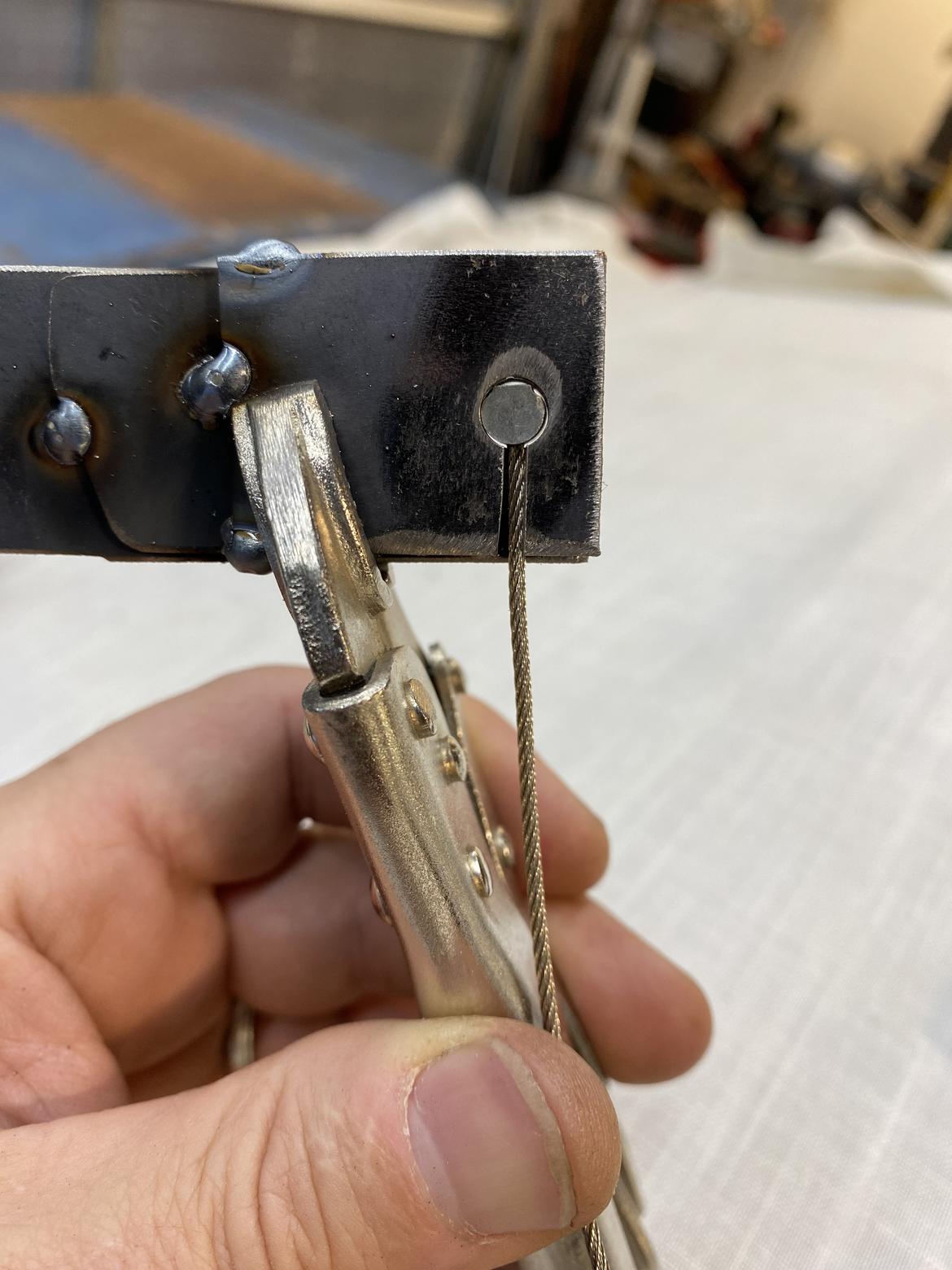
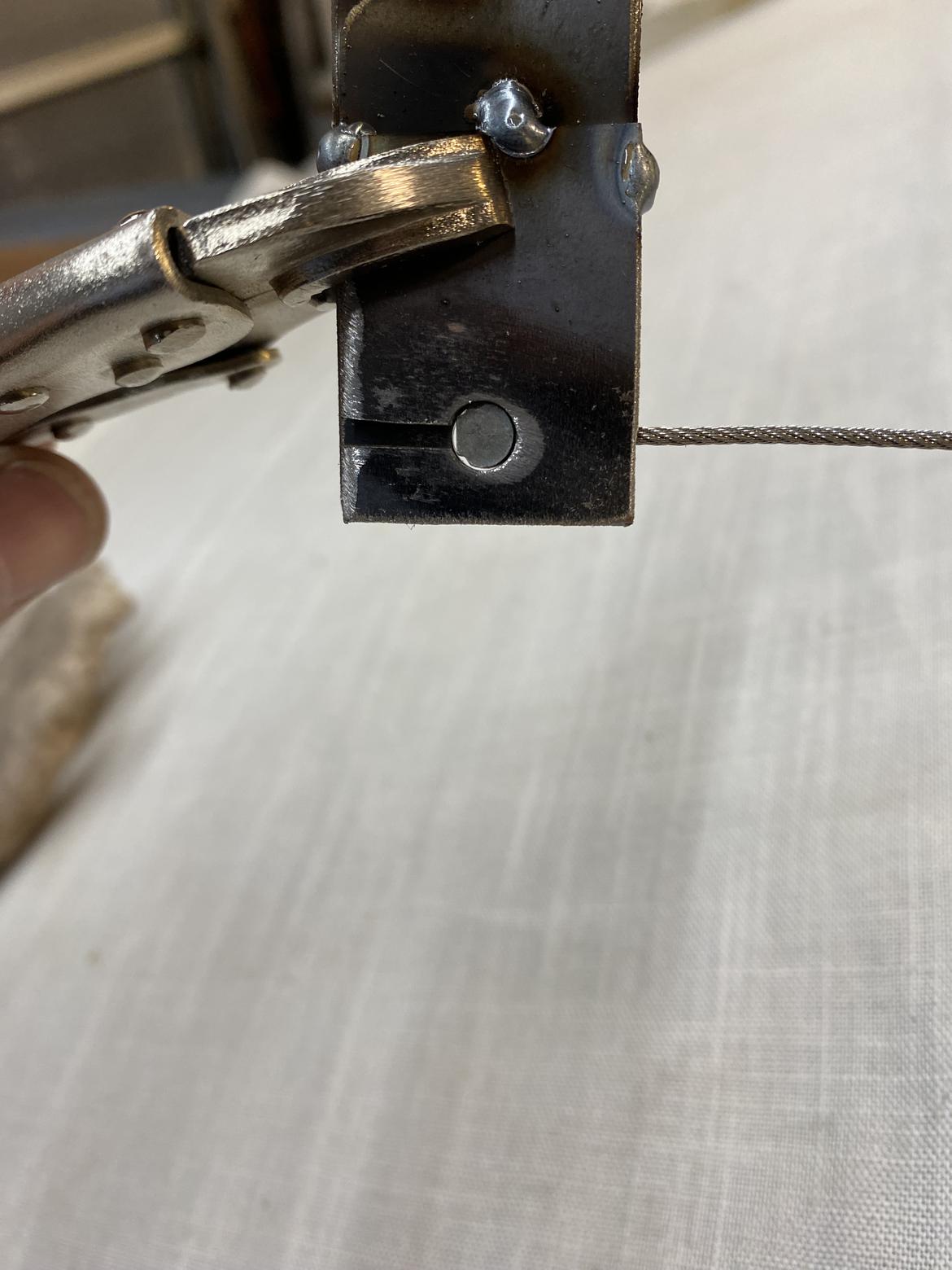
Then I cut a scrap of 16ga 3/4" square tube to make a height spacer, so the cable was aligned with the housing, because efficiency. Then I added a 5/16" nut in between the spacer and the cable attachment because I can't measure E36 M3 right. I blocked the TB at WOT, pulled the cable tight below the car, set the pedal at the floor, hooked the cable to the attachment, and clamped it to the bellcrank off the gas pedal rod. I increased the lever ratio slightly so the gas pedal would sit a little closer to the floor at idle vs how it was at the challenge. Tacked it all together and here's how it is now, ugly but functional. Definitely good enough.
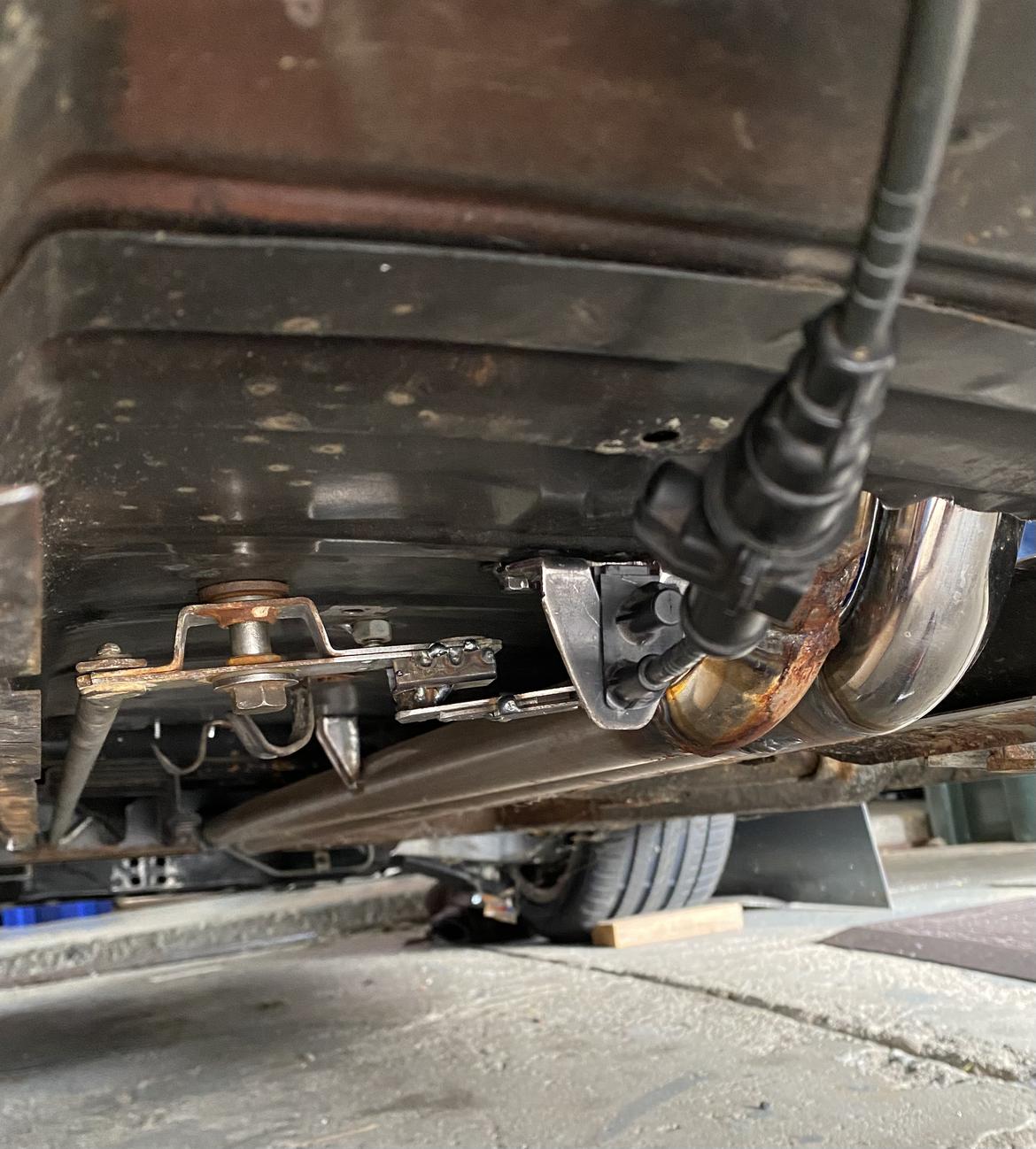
Then I went to install the LR wheel and noticed some slop at the UBJ, which I discovered was because the taper is machined a little too deep, and the nut bottoms on the thread before the taper is tight in the knuckle. So, with a 1/2" bit in the drill press I drilled something like 1/8" of the threads out and now it clamps up just like it should. No pix of that.
tomorrow, if the weather is good, I'll put the firewall in place and go back to tuning. I'd like to at least nail the idle so I can try to drive it again and collect some data.