TL;dr - starter issue seems to be whipped, now working on minor mods and reassembly.
Longer version, some of which is a little repetitive, so please forgive me. back in the day, to minimize the thickness (and therefore the cost) of the bellhousing adapter plate, i chose to use the Audi starter and flywheel ring gear. I designed the drive gear to ring gear interface a little too tight, and it was obvious that the drive gear teeth were crashing into the aluminum behind the ring gear.
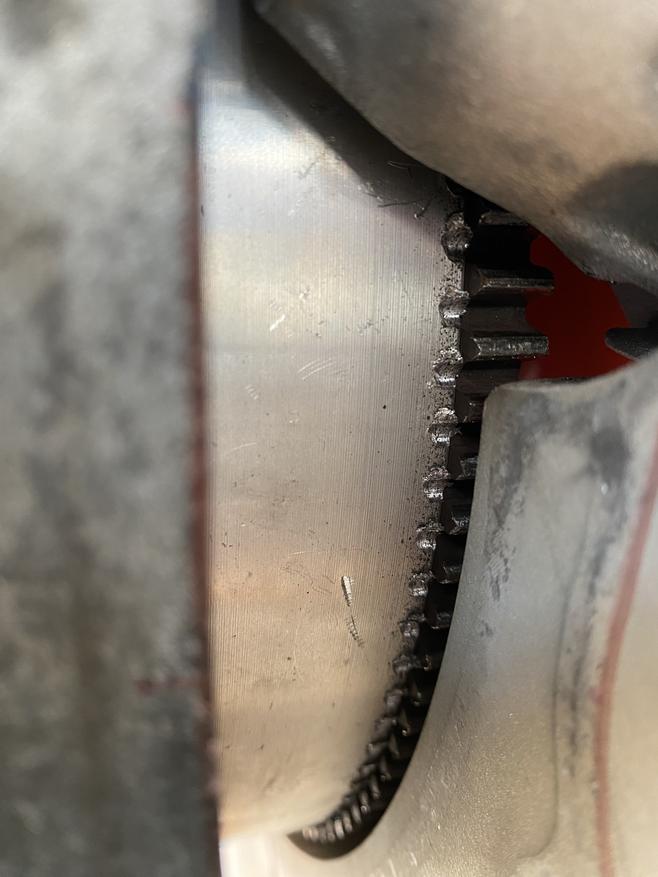
here's some pertinent starting system math:
- Audi: starter power = 1.2 kW; ring gear teeth = 116; starter drive gear teeth = 9. so 1.2 * 116 / 9 = 15.47
- LT1: starter power = 1.4 kW; ring gear teeth = 153; starter drive gear teeth = 10. so 1.4 * 153 / 10 = 21.42
so by comparison, the Audi starting system was at a [ 1 - ( 15.47 / 21.42 ) ], or 28% disadvantage relative to the LT1 system. berkeley that.
i removed the adapter plate and got an LT1 starter and flexplate and mocked things up. this ring gear is proud of the back of the block by almost a full inch, which is exactly the thickness of the adapter plate. That's no bueno, because opening up the adapter plate for the 13" diameter x 1" depth would remove all the threaded holes and I couldn't attach the transaxle anymore. Trans bolts are M12, and minimum thread engagement should be 1x diameter. This means I can hog about 1/2" deep into the plate. OK, so I need to space the plate away from the block by 1/2". Fortunately, it's no big deal to make (or buy, copy, and return) a 1/2" spacer, so I bought 2x 1/4" spacers and longer bellhousing alignment dowels. note to self: get adapter bolts 1/2" longer than current.
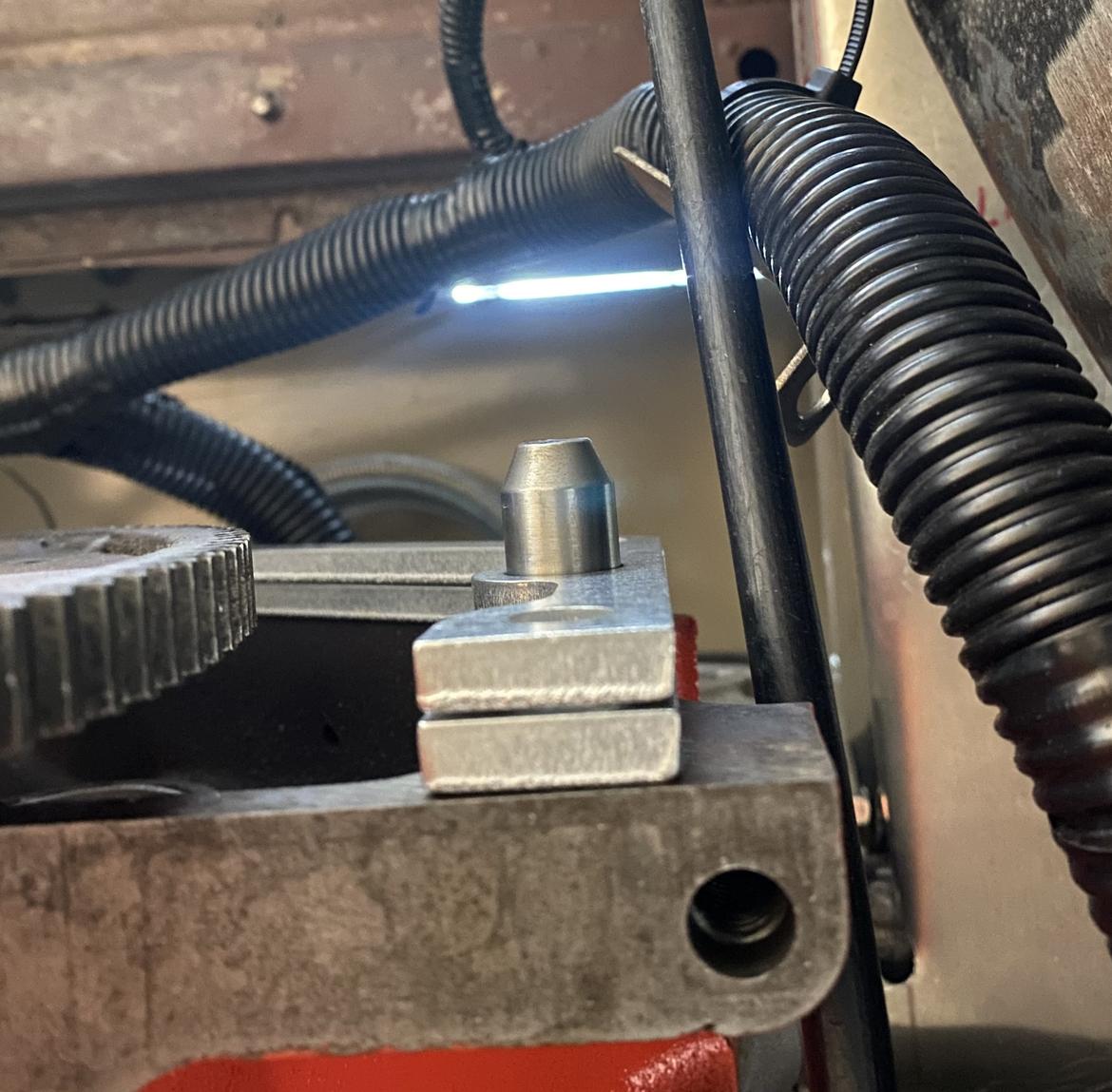
Next hurdle: the throwout bearing needs to be in the same place relative to the clutch fork, which is now 1/2" farther rearward. this will require spacing the Audi flywheel rearward by 1/2" minus the thickness of the LT1 flexplate, or 3/8". This is also no big deal, either to stack readily available shims or machine one up. For now, I bought 2 variety packs of shims. Even when i'm not making parts, there's a bit of CAD going on.
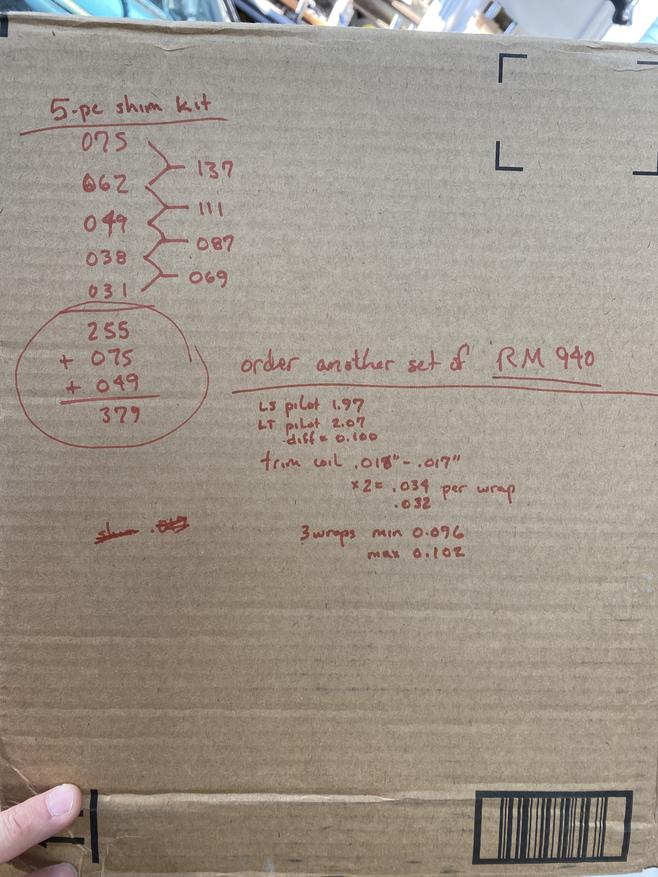
Next hurdle: those shims need a pilot, as does the Audi flywheel. Again no big deal, I bought a crank pilot extension, but to make it sufficiently janky i bought one for an LS, which is the same diameter into the crank, but is about 0.100" smaller OD. Good thing we are having the siding replaced on AngryHouse, and I've got a dumpster of scrap siding and trim in the driveway.
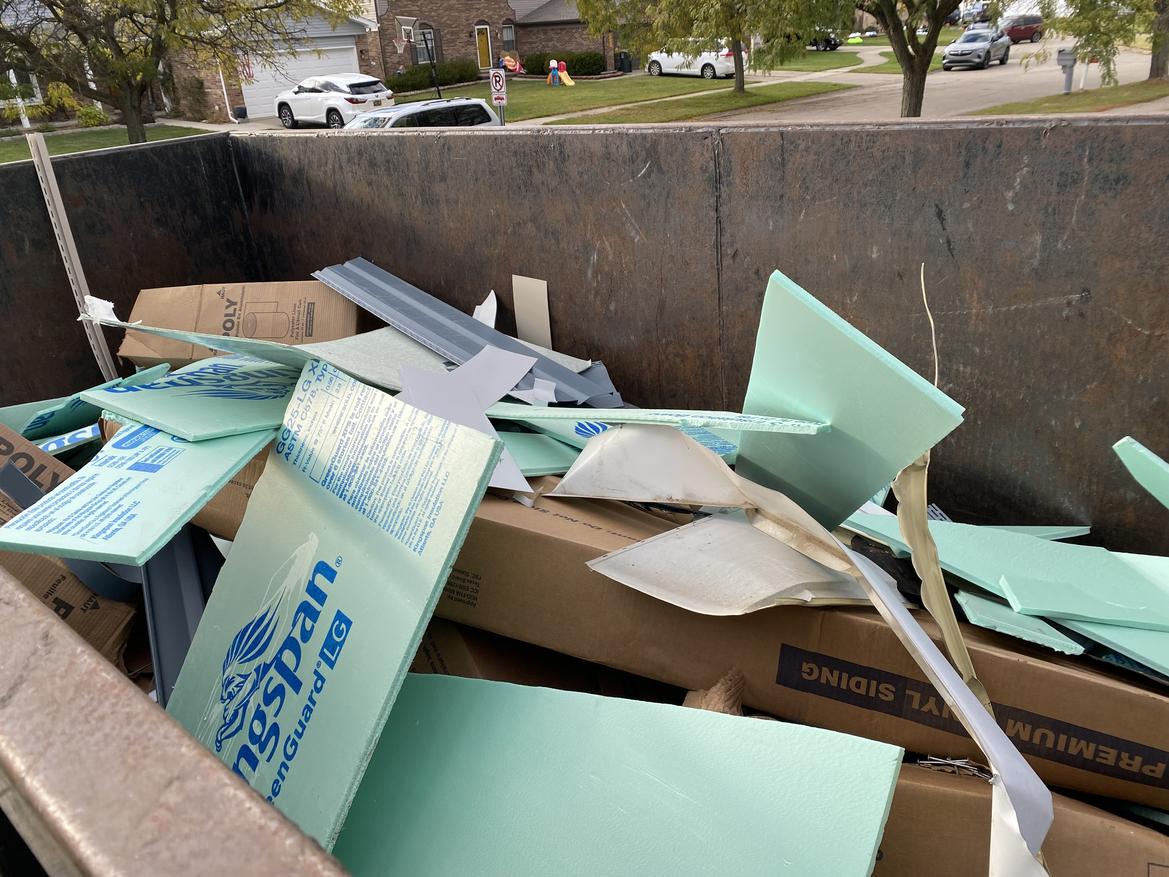
Turns out the flashing is 0.016"-0.017" thick, so three wraps gives 0.096"-0.102". With a combination square and tin snips, i made the required shims and all the bits are a nice slip fit.
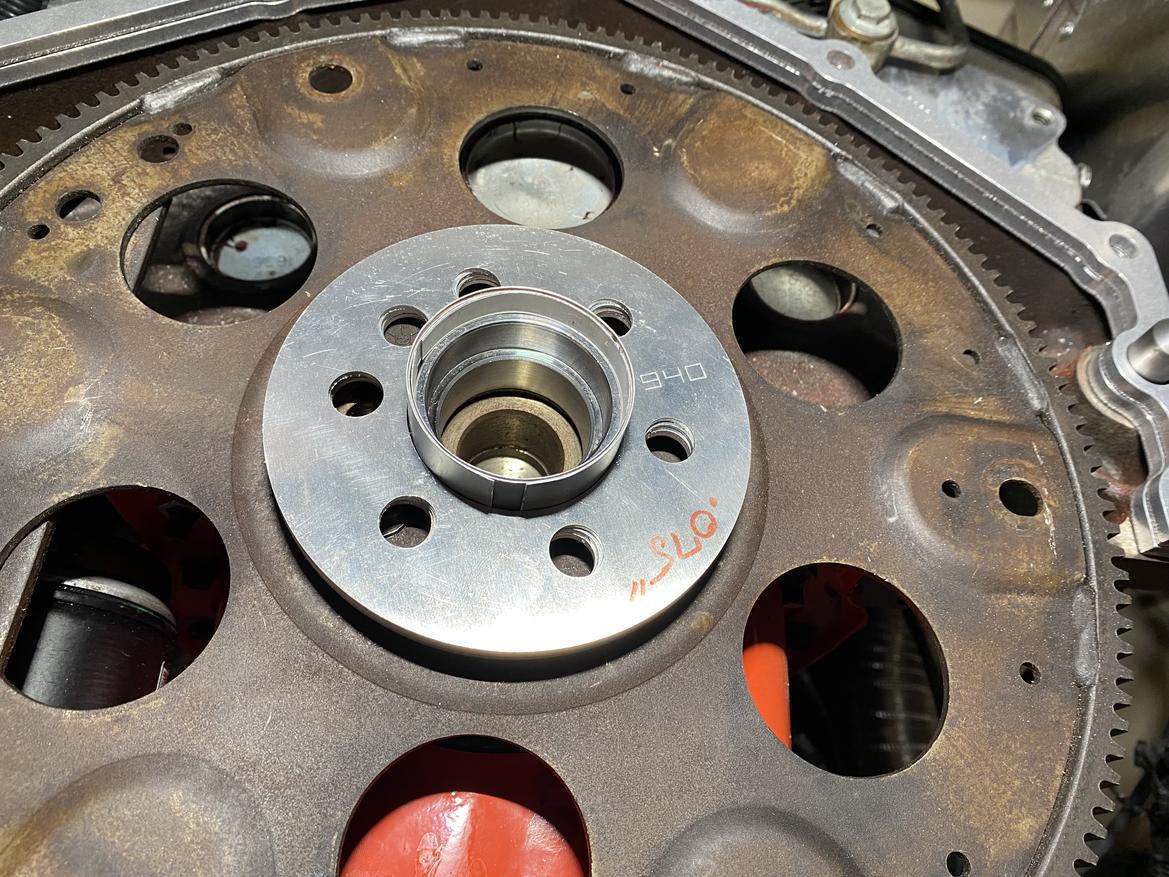
next step is to meet up with whiskey_business and get some quality time on his Bridgeport. Mod to adapter plate should not be too difficult. Note to self: i still need to get flywheel bolts and an alignment pin 1/2" longer than current. Next step after that will be to relocate trans mount 1/2" rearward.