I took appart the OEM Subaru steering column and turned it into the world's shortest column. I was going to reuse the top and make a short stub in the middle to weld them together. But then I realized that the upper section of shaft was exactly 3/4" so I just made a extension all the way through the upper bushing. Which Subaru uses a needle roller bearing. I then just cut the top and bottom off the column and welded them together. They aren't exactly the same size but close enough.
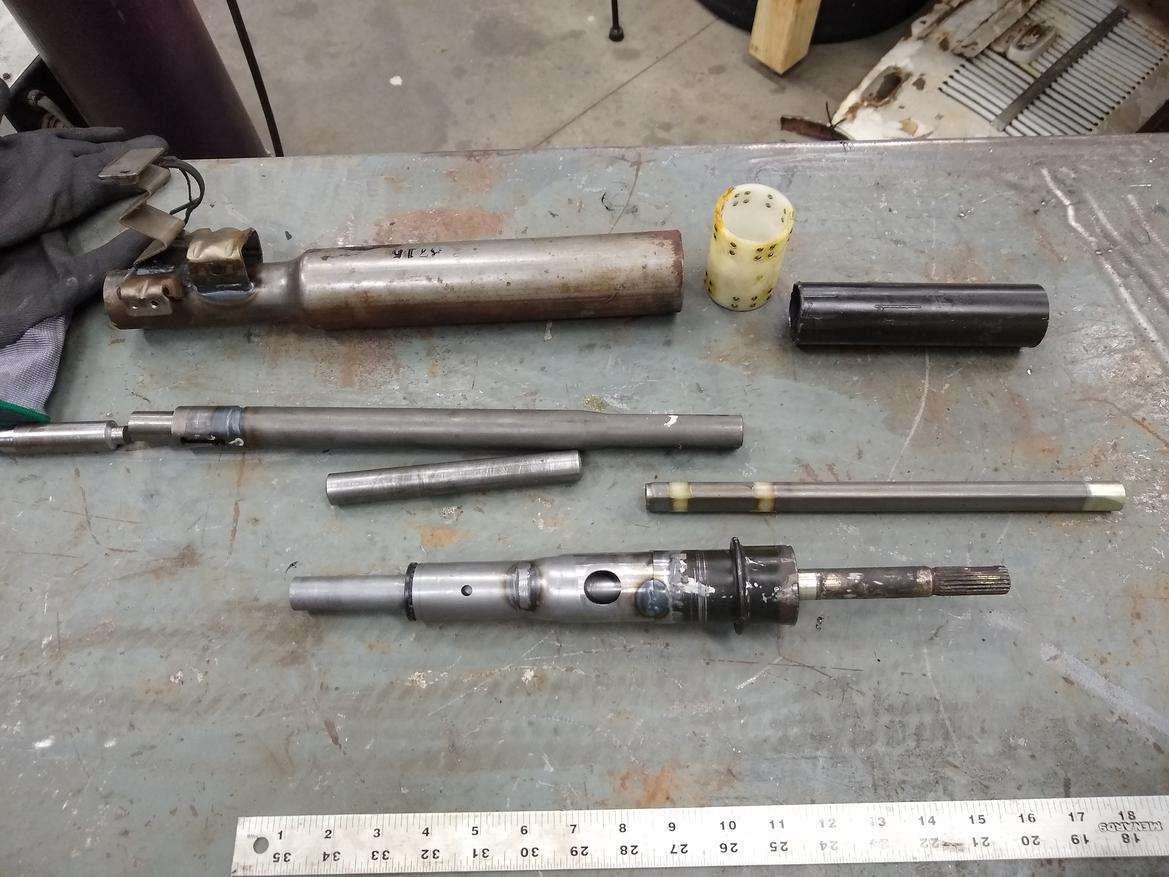
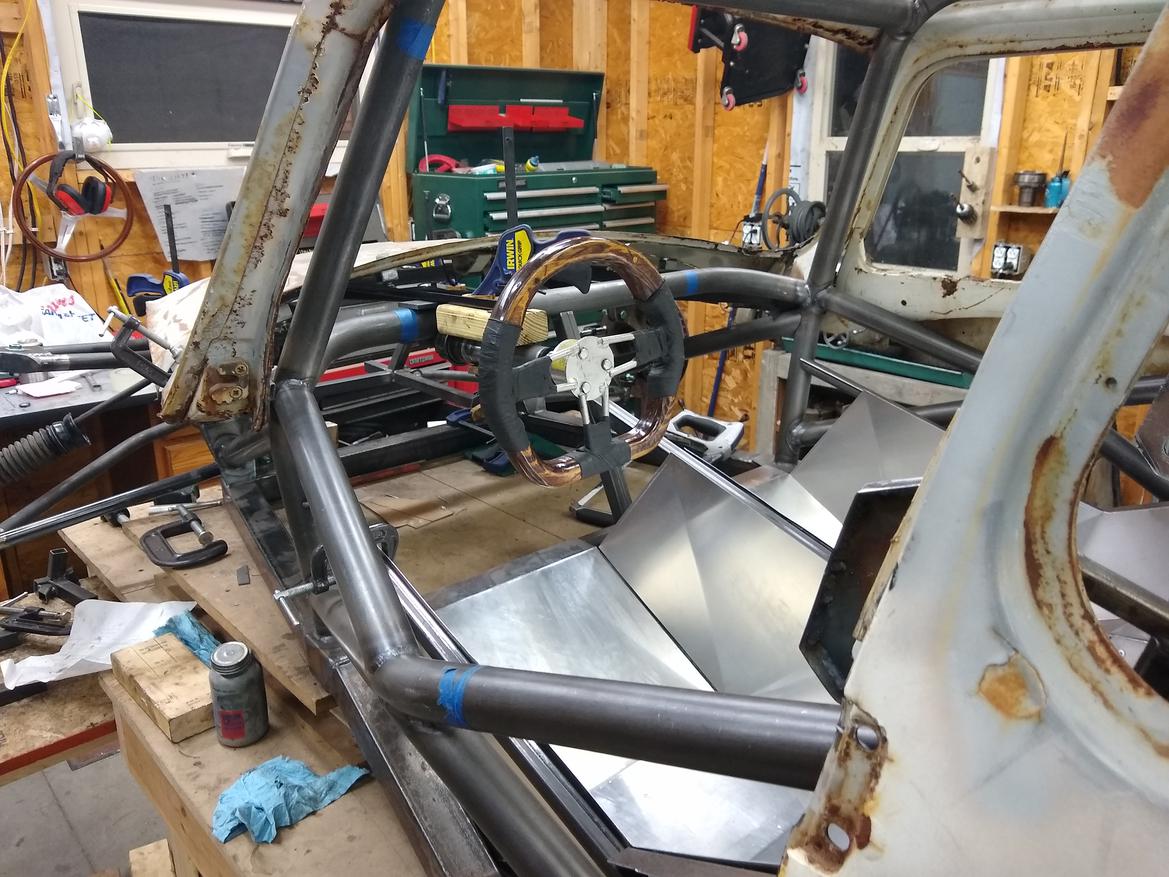
mke
Dork
5/3/21 10:35 a.m.
Tell me the steering wheel stays through the challenge 
Took a quick hour and CAD templated a steering column mount. I considered welding the column in directly but decided removeable may be the best long term for service. I will just weld the cross tubes to the colum and then have the 3 bolts (1 through bolt, and 2 shorter tapped bolts).
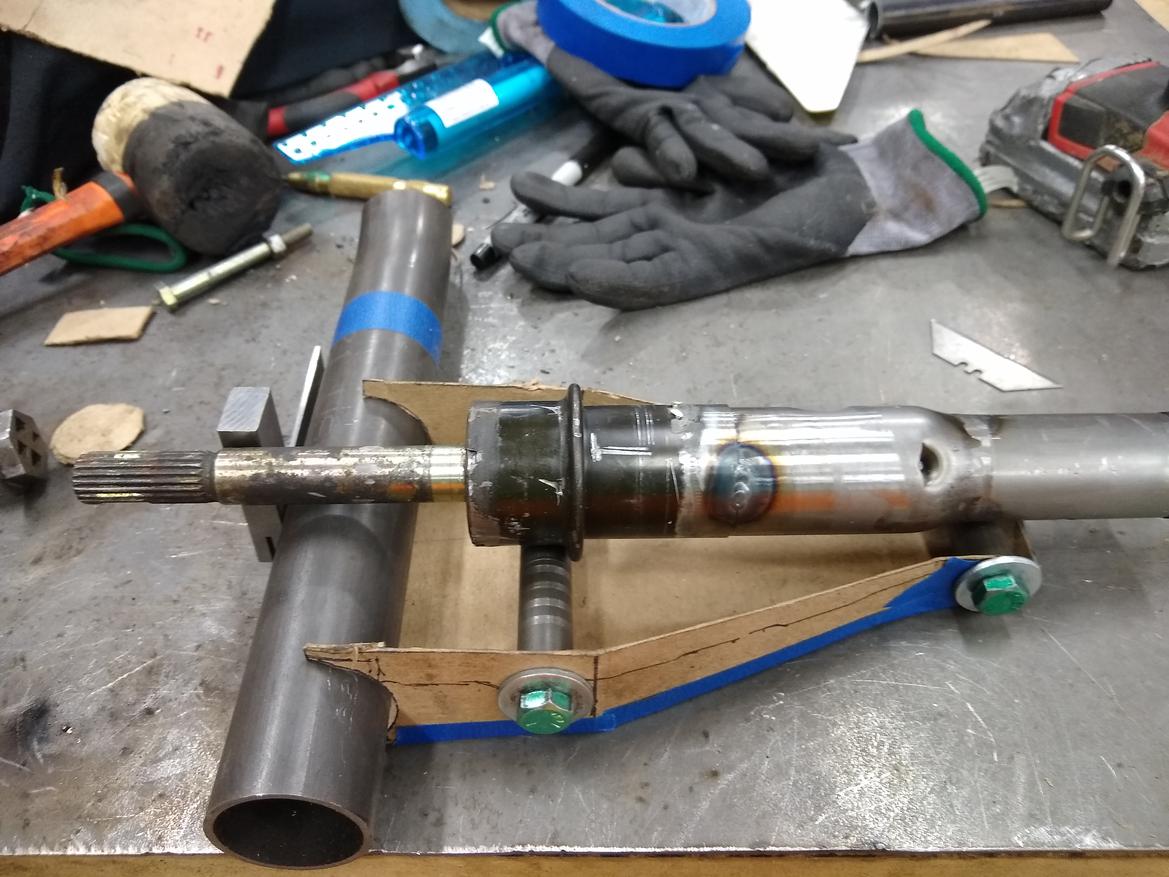
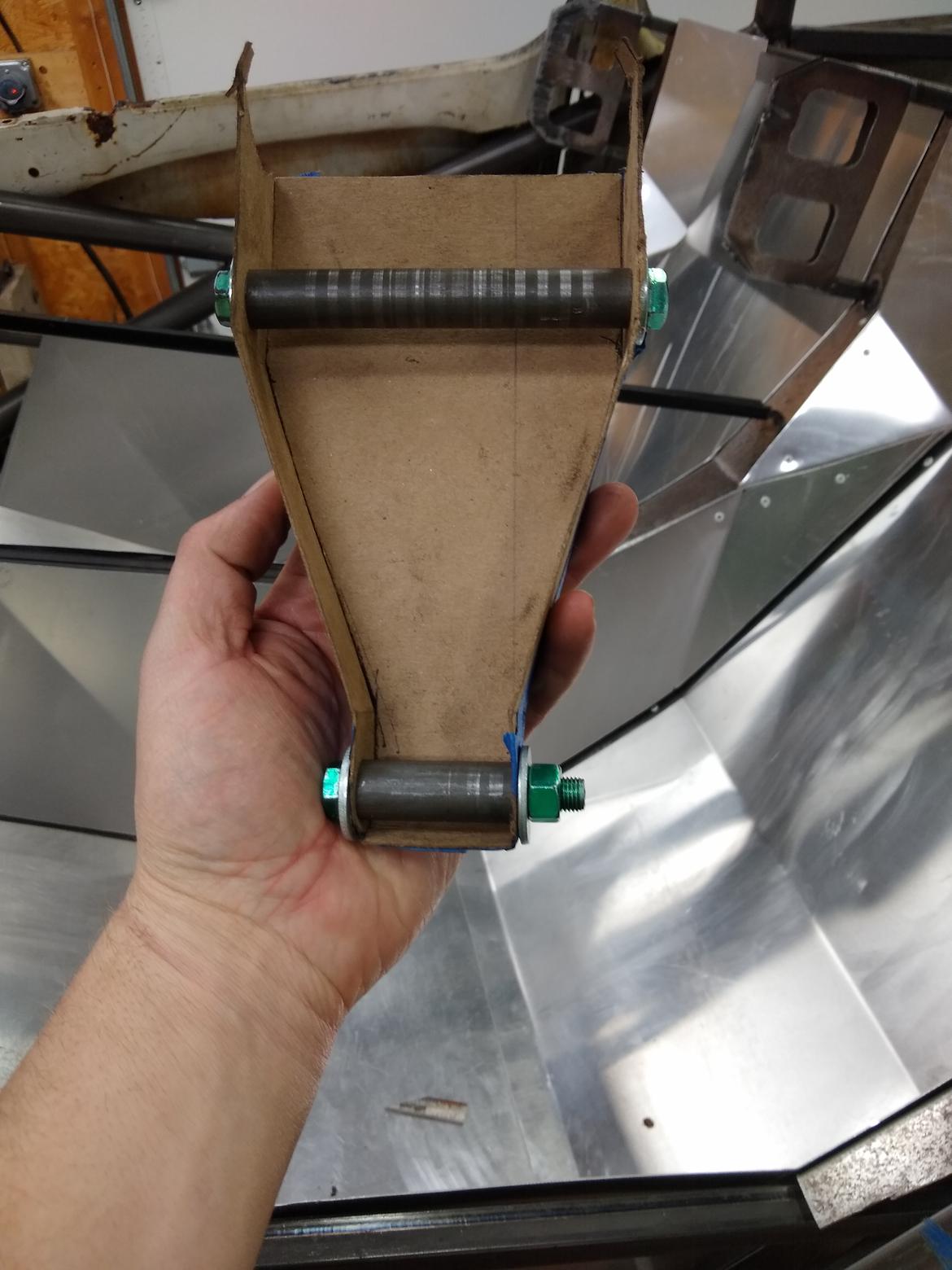
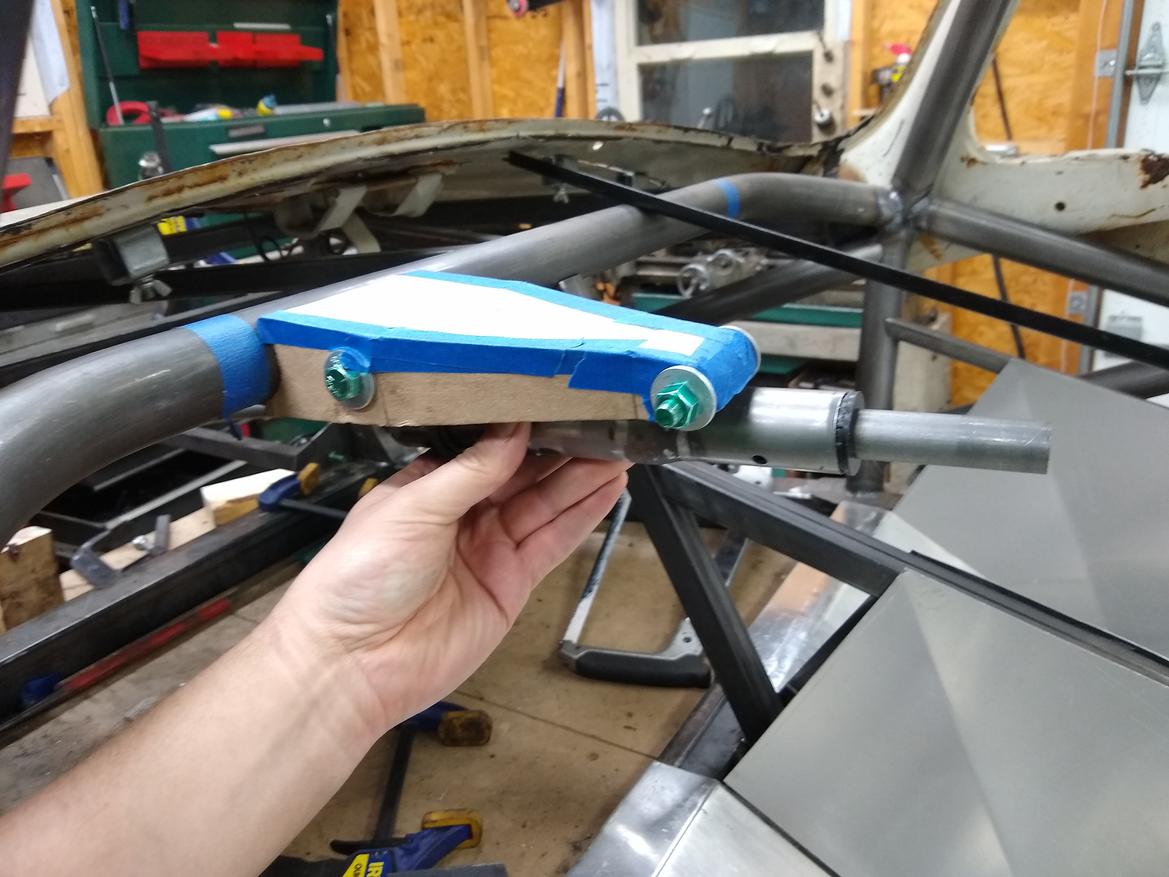
It's probably way overbuilt compared to what it has to be but steering column strength and rigidity seems important..
Rigante
New Reader
5/3/21 11:16 a.m.
cool work as ever, just ensure that it won't spear you in an accident, as you have a very beefy mount pointing at you currently
In reply to mke :
That steering wheel was built for the MG and is an outlaw and can't be used.. technically. It's made without a metal rim so the world says it's "Dangerous". It's made from 2 sheets of BC plywood glued together. I've stood on it and it doesn't even creak. It's fine. But the rules are the rules so it's a garage ornament.
I've thought about routering a pocket in it and embedding a 1/8th rod of metal around it to "legalize" it. But I have a different concept for this cars wheel that I'm going to build (This time with metal rim).
It's inspired by the control yoke of mid 60's/70's aircraft. I figured it would be the most "Period correct" interpretation of what a modern LMP1 steering wheel is. Has the modern D-shape (which I love, I know some hate) but draws inspiration from the time period I'm trying to target. It's going to be a metal tubes on top and botom, welded to flat metal plates where the handgrips are. The grips are going to be laminated wood, probably the same Cedar I'm going to make the Aero parts out of. The hub will probably just be fiberglass covered foam (Over an actual metal plate hub obviously). And I am planning to try to resin cast or 3D print a second original Subaru symbol from the hood for the center. 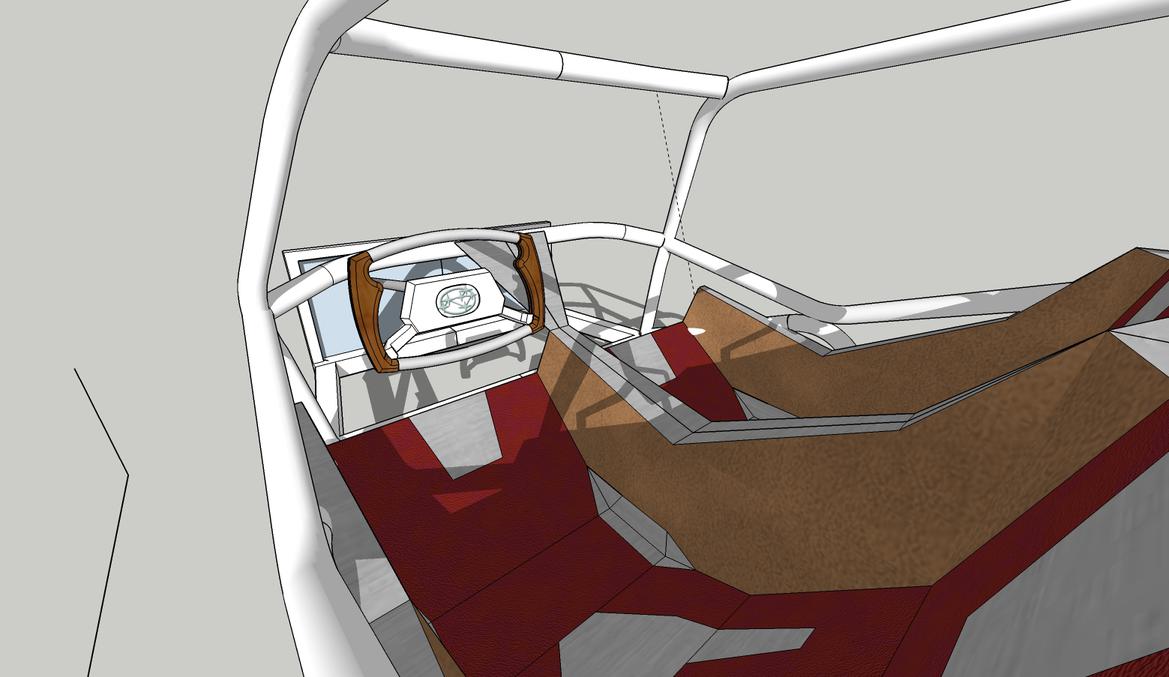
I'm very hopeful that this car will blur the line between a functional very fast car, and almost themed art. We will see how close I get and how well I do. I don't think it will be "complete" this year. Which I'm kinda bummed about because I don't want this car to be like the MG in that It's known for being Unfinished. At this point I feel like the MG has a "look" that I love and that I want to keep. That said I don't need 2 "Rat Rod" track cars. I want this one to be painted and stuff. I know if I bring it unfinished just like the MG 50% of people will love it as is and never want to see it painted, and 50% will say it will look good once it's painted. The vision I have is to be "complete" with this one. That said if it can drive around it's coming to the challenge this year. And if I then finish it next year and people hate that I "ruined" the unfinished look that's too bad.
Sorry that turned into a emotional journey about cars as an artistic vision.
Rigante said:
cool work as ever, just ensure that it won't spear you in an accident, as you have a very beefy mount pointing at you currently
Hmm.. I'll have to put some thought into that.. I'm tempted to say that If my torso ever arrives at the steering colum in this vehicle something very very bad has happened and being speared by the steering column is the least of my concerns. But saying that being speared by the steering column sounds horrible.
I could make the actual column break away or at least be able to move relatively easily.. I could slot the rear holes in the bracket some and make the front tube mount a U rather then a full tube. That way the steering wheel would move forward in a large impact. I can't really make the columng mount bracket break away.. Though I could cut part of it away to maintain rigidity but make it so it would collapse if really really impacted.. The steering shaft it self will have the ability to fold out of the way (Multiple u-joints) so it's not going to force the steering shaft backward into me while I'm still in the harness.
The stock MG midget column (A shining beacon of occupant safety if there ever was one) has metal bushings that allow for about 1" of column forward movement (This is in addition to the actually collapsible shaft and lower column). So in an impact the shaft would collapse and the actual steering wheel would move forward about 1" if an occupant slammed into it. In the stock Subaru the steering column mount was solid at the wheel because it is the base for the airbag to work. In an impact the column would collapse but the steering wheel itself would stay rigid.
I think the actual wheel end of the colum staying basically rigid is a pretty common layout? Most race cars I've seen use a 3/4" non-collapsible steel shaft with 2 or more U-joints to prevent spearing. That shaft is rigidly supported by a 3/4" rod end anchored usually to a tube welded to the roll cage, or they use a stock upper column with stock mounting. Unless I am missing something the actual steering wheel and it's mounting are designed to stay in place, with all the design work spent to prevent them from being pushed into the driver.
These are good conversations. Please keep having them. I'm trying to think of Everything.. But everything is big. If you see something that's a concern I love when people point it out and we can discuss it. I'm fine with re-doing work if it makes it better/faster/safer.
mke
Dork
5/3/21 1:19 p.m.
In reply to nocones :
I like it.
Question, how many degrees or turns lock to lock? Something like that work great at 180deg, 240 maybe, 270 about it as there is no way to move your hands. Just all fresh on my mind after just adding a 2:1 quickener to my car.
5 point harnesses, right? Current setup should be fine. Note, I am not an engineer. Please correct me if I'm wrong.
Yes, as ever, epic work. Do carry on.
wheelsmithy (Joe-with-an-L) said:
5 point harnesses, right? Current setup should be fine. Note, I am not an engineer. Please correct me if I'm wrong.
Yes, as ever, epic work. Do carry on.
The issue isn't with you moving to meet the steering column, but the front of the car getting smushed, and the column coming to meet you.
Rigante
New Reader
5/3/21 3:23 p.m.
looking at it again, you do have some serous structure in front of you, so guess it's possibly not too bad, and as you say many race cars are this way
If you can get a good Z shape into the linkage between the column and the rack I think you will be Ok
Cardboard is now steel. I could spend another half hour cutting more holes in it.. But I think it's achieved the right amount of "I care about lightness" but not gone to far.
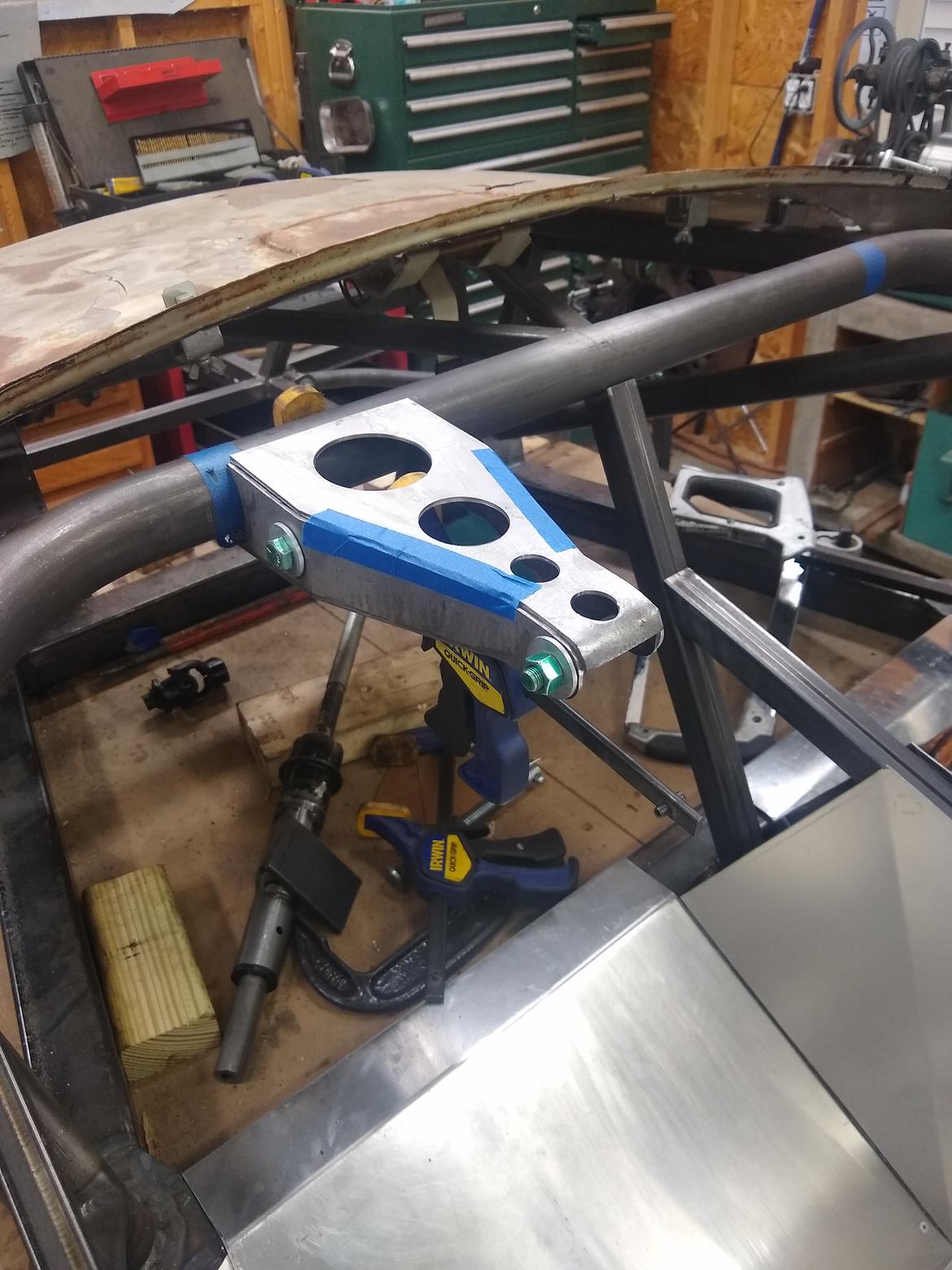
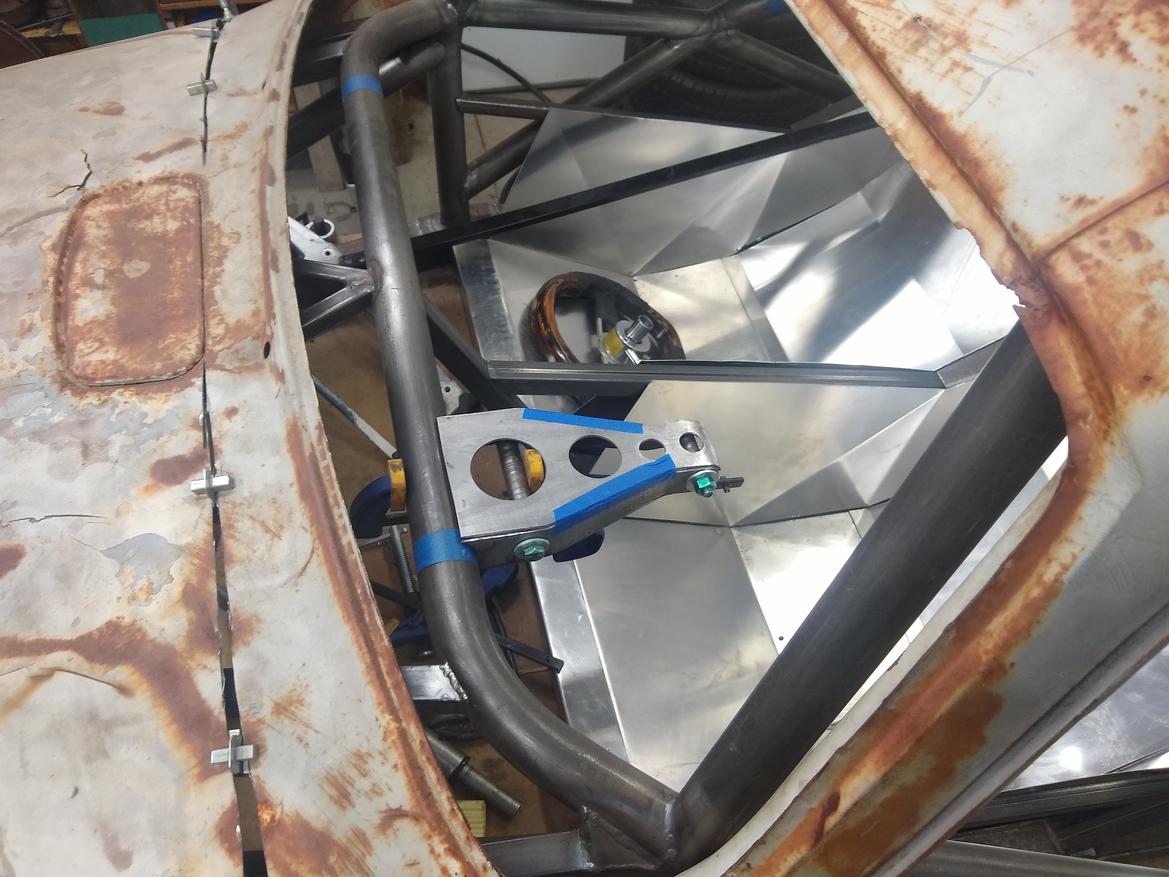
+$3.77 for the shortened column and mount.
mke said:
In reply to nocones :
I like it.
Question, how many degrees or turns lock to lock? Something like that work great at 180deg, 240 maybe, 270 about it as there is no way to move your hands. Just all fresh on my mind after just adding a 2:1 quickener to my car.
I don't actually know. This is one of those areas of the car I just don't really design I just let happen. My goal is to make the steering arms a length such that the wheels turn about the same per 1/2 rotation as the MG does. On the track I never use more then about 1/4 turn. Even at Autox I rarely have to move my hands. So it's a pretty good effective ratio. I can probably get away with a little more ratio then the MG because the front will be lighter on this car.
I know I should do the math for the travel per turn of the rack, then the radius of the steering links and the wheelbase of the car, but I just kind of wing it.
I wish steering "ratios" were just the travel of the steering shaft per turn. It's the only meaningful measure for a builder. The midget is 2-1/8" per turn. Coupled with Miata a arms it becomes pretty quick.
Karplus2 came over again and yesterday evening we got the collumn mounted, steering arms cut, and tack welded in. I more Ridgidly clamped the rack in place and made with the turning of the wheels from a remote distance.
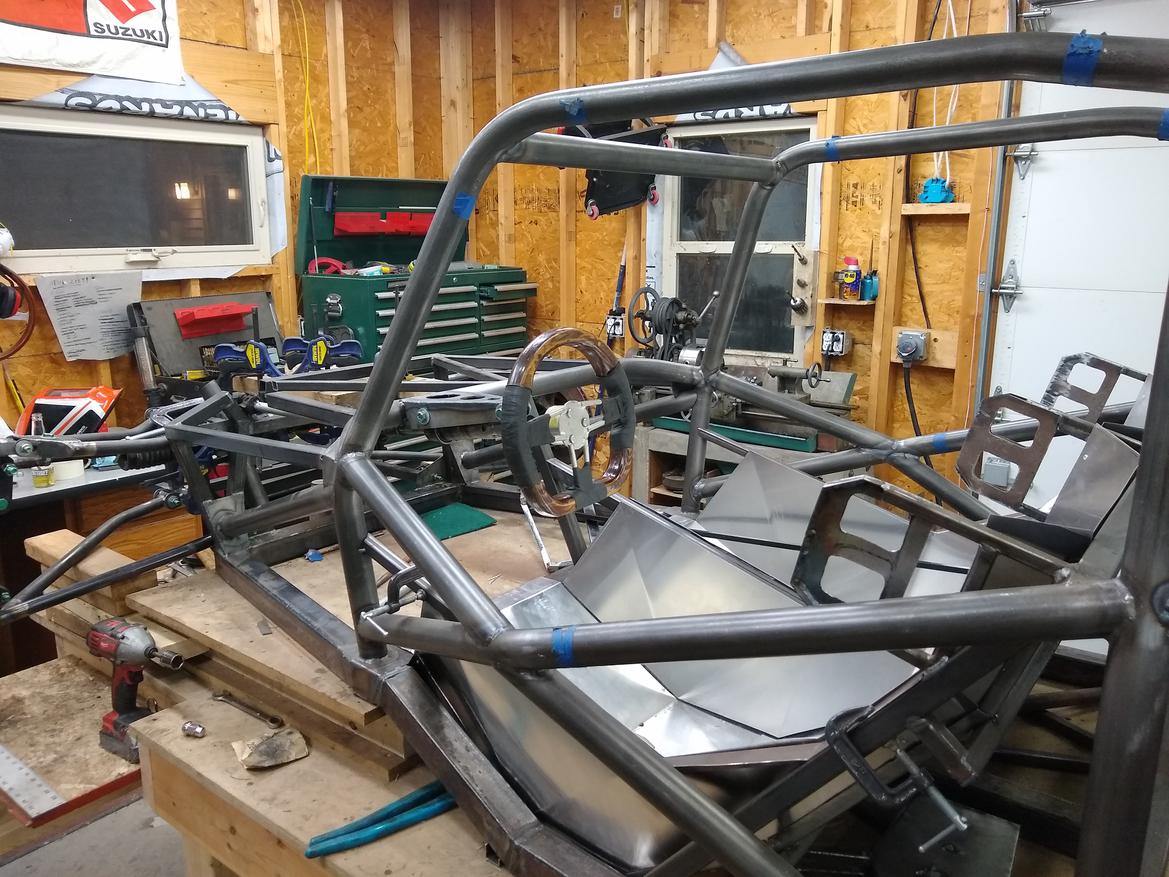
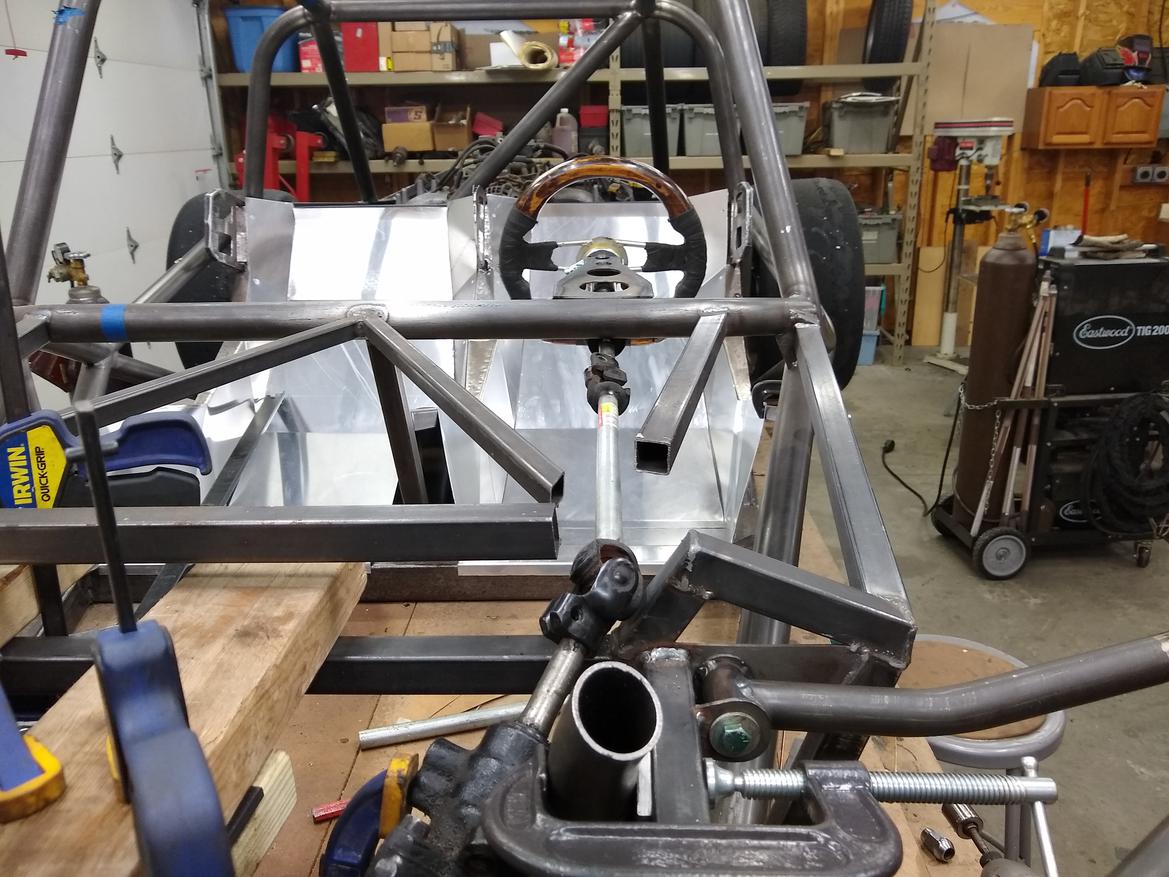
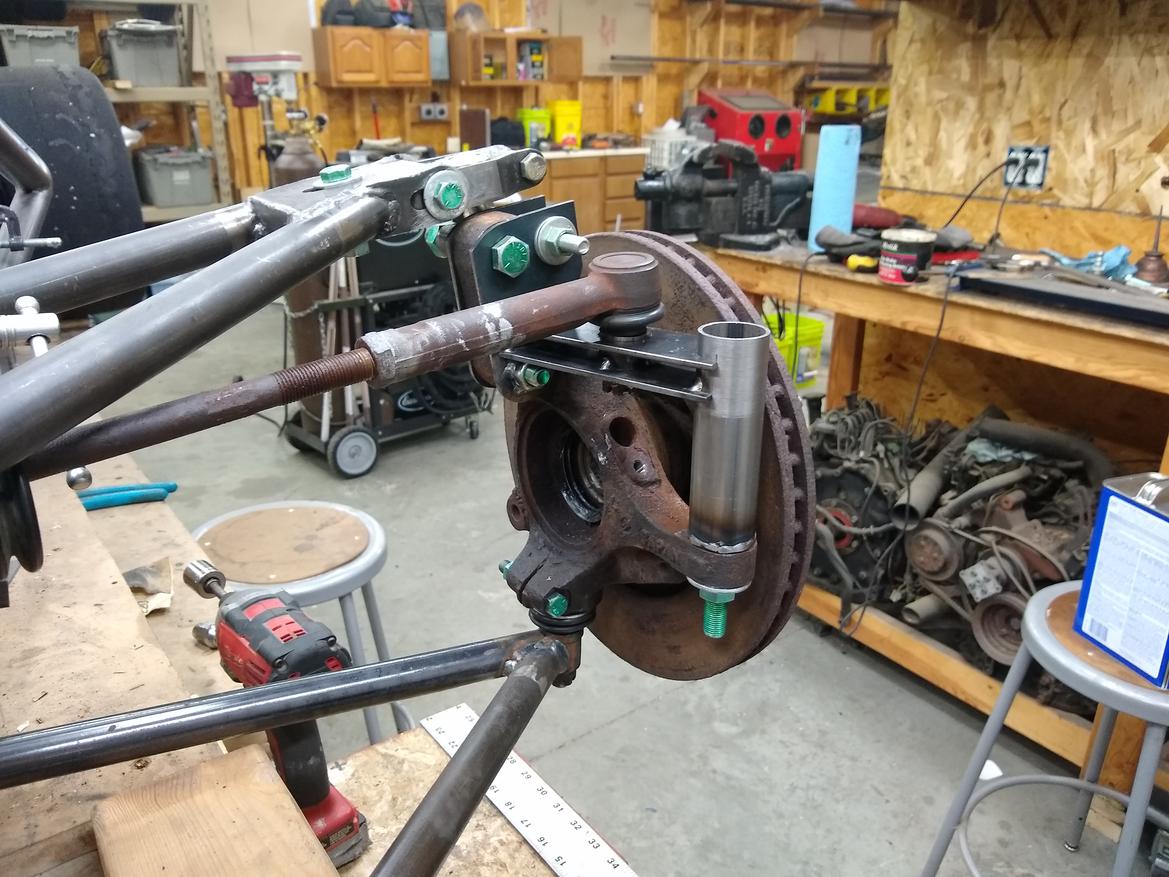
I also learned I did a bad at math. My current effective steering ratio is 16:1 which per this chart I found (https://sites.google.com/site/mitostile/vehicle-dynamics/simulation/databases/steering-ratio) is pretty mediocre. The steering arm on the car is 4.75" long. I compared 90* and 180* turns to the MG and was getting about 66% of the steering angle the MG achieved for the same turns. The MG has ~11:1 and is pretty good. I would be happy with that ratio in the 360.
The Subaru rack I have moves 1.75" per turn. For my desired steering range of ~400* total for all possible autox turns I will have to calculate the new steering arm length. The minimum I can run without changing big things is about 3.25". Just based on the fact that the current ratio is 16:1 and 3.25/4.75 = .68 I should get right around 11:1 steering ratio. I will validate that that produces a wheel steer angle sufficient to turn the car around an Autox min radius turn at ~200* steering travel. I know from onboards I rarely ever exceed 150* and the Max I've used is ~200. Road course unless I'm sideways it's all <90* steering angle. So I think I will be ok if I can get to ~11:1 with moving the steering arms in more. We will see. I own a welder. If it needs quicker steering after use I can either find a rack that moves father per turn or redo the steering arms again.
I will put together a spreadsheet that takes rack travel per turn, desired steering wheel rotation, vehicle wheelbase, and steering arm length and spits out turn radius and steering ratio. Once that's done I'll post some results and share it for everyone. I didn't want to do more math but after failing it's time to do some math.
The good thing is I can compare the MG and the 3 additional racks I have accumulated to see if any of them would be worth trying. I have anothe MG rack, a geo metro, and a 1995 Miata. Initial inspection shows they all are around 1-3/4 to maybe 2" per rotation. I would need more like 2.5" to make a swap have enough benefit to have to carry a rack In the budget.
Ok. Tons of thinking and some fabricating have resulted in this.
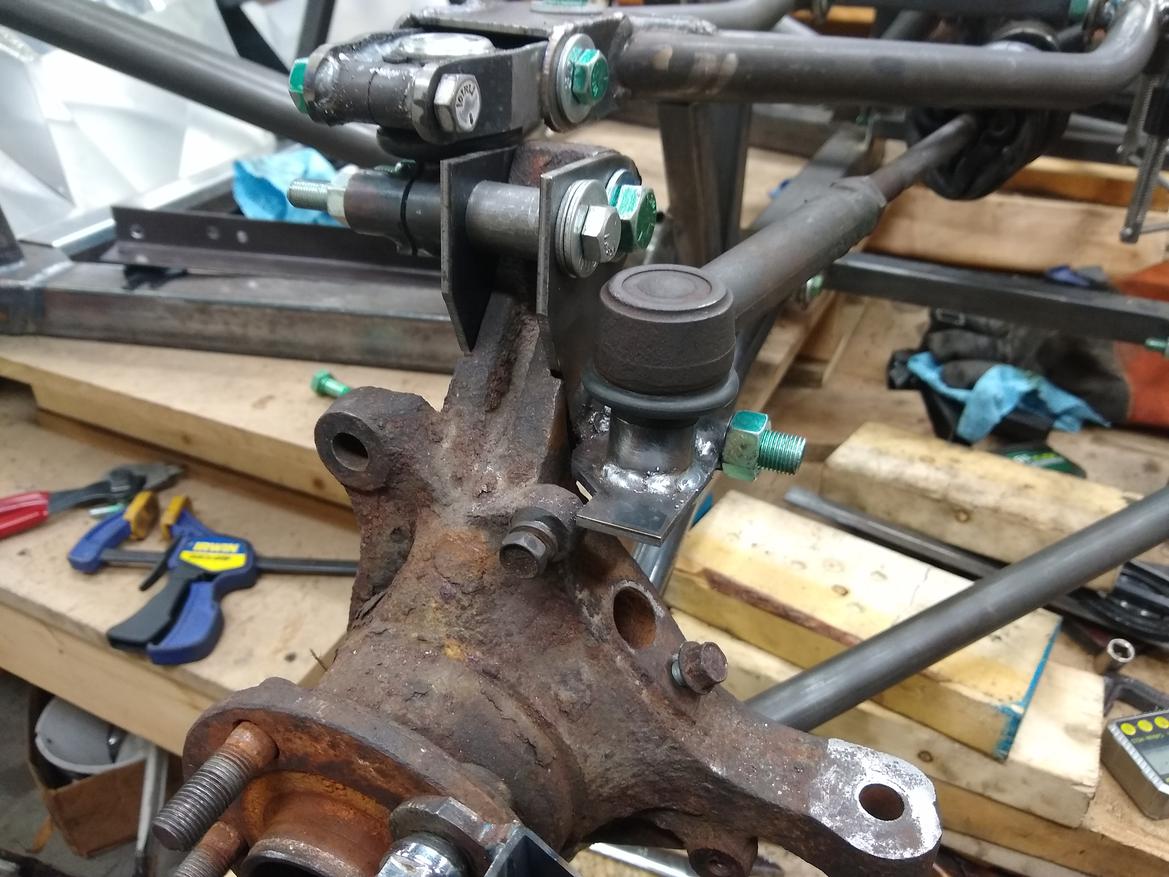
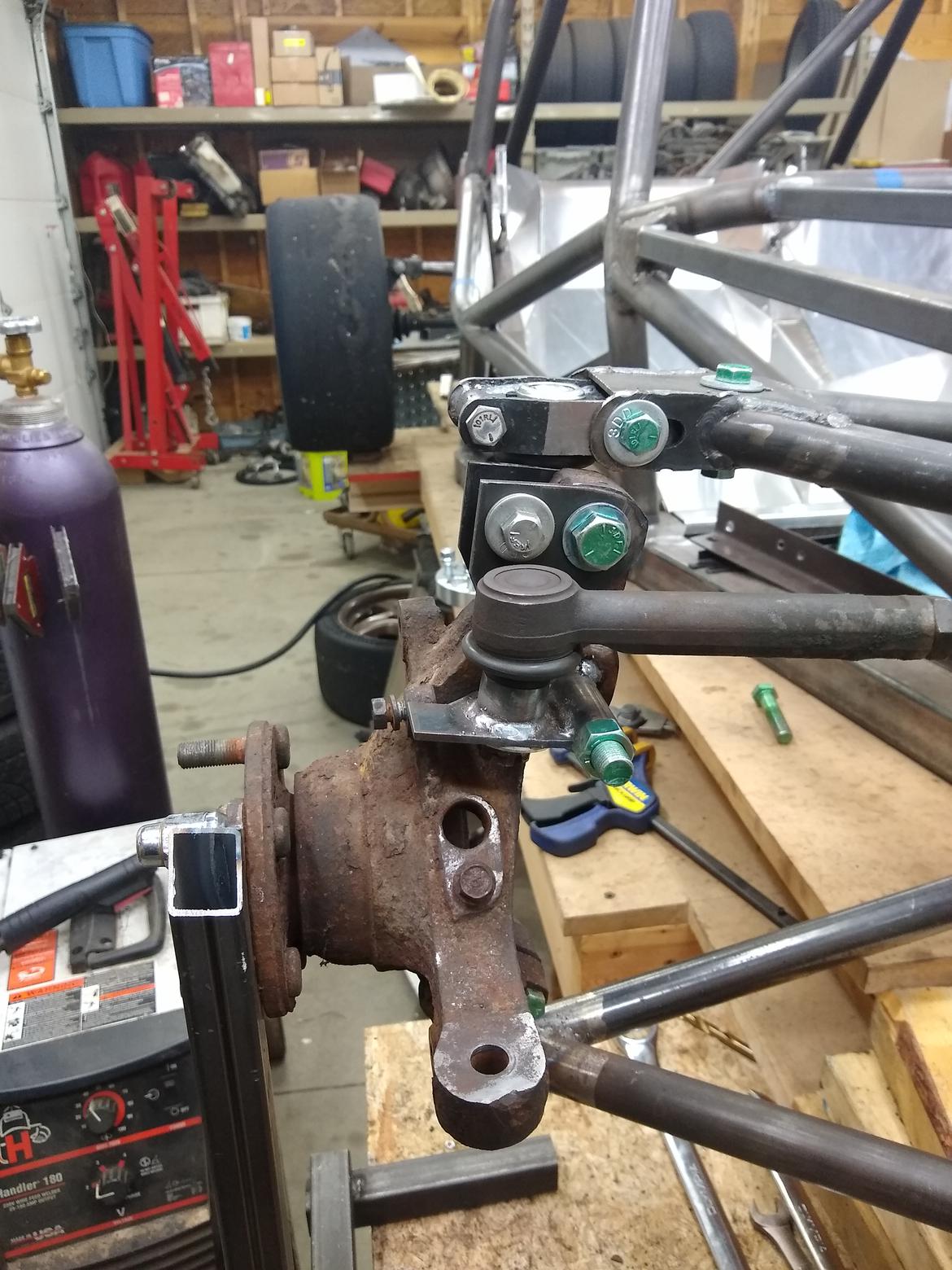
The plan is to add a second plate and then tie it into the two bolts in the upright. These aren't huge bolts but they should still take a few hundred lbs of load.
This gives a final ratio of ~10.5:1. I should be able to navigate a 25' radius corner at a bit under 200* of steering rotation. Looking at the math for corner radius this puts 90% of track corners at 0-90* of turn, with autox likely only being 0-150.
Ackerman is just "100%".
The spreadsheet I made still would need a little cleanup to make sense to anyone else, but looks sort of like this.
You input rack movement per turn, wheelbase, and desired steering rotation and it spits out corner radius and average wheel angle for multiple steering arm lengths and steering angles. It also calculates the minimum radius and Max steering angle for whatever your Max range is.
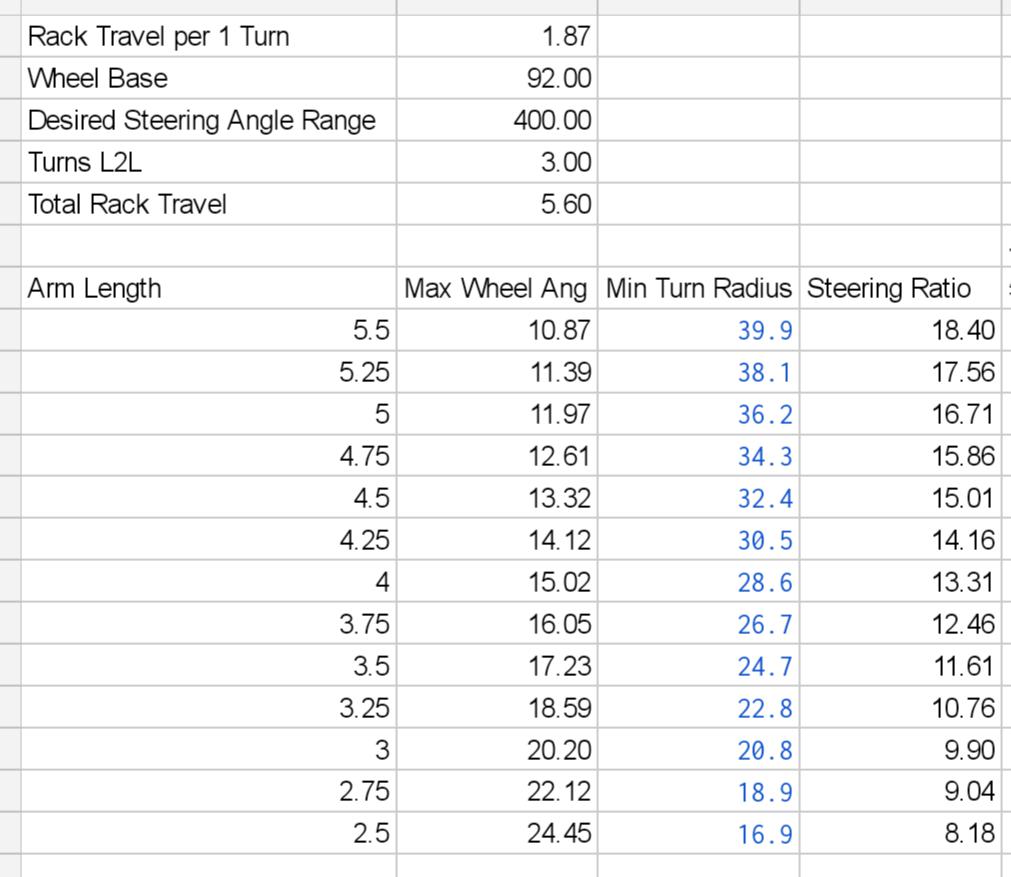
Interestingly enough like most things with vehicle dynamics you wind up with one dimension that fairly well captures the system in one easy to understand way, and ironically despite my protesting earlier that's steering ratio. Steering ratio does not directly account for wheelbase, so you have to do math to figure out exactly how the result of steering ratio will impact dynamics. That said with ratio and wheelbase you can easily determine the corner radius you can navigate with different steering angles.
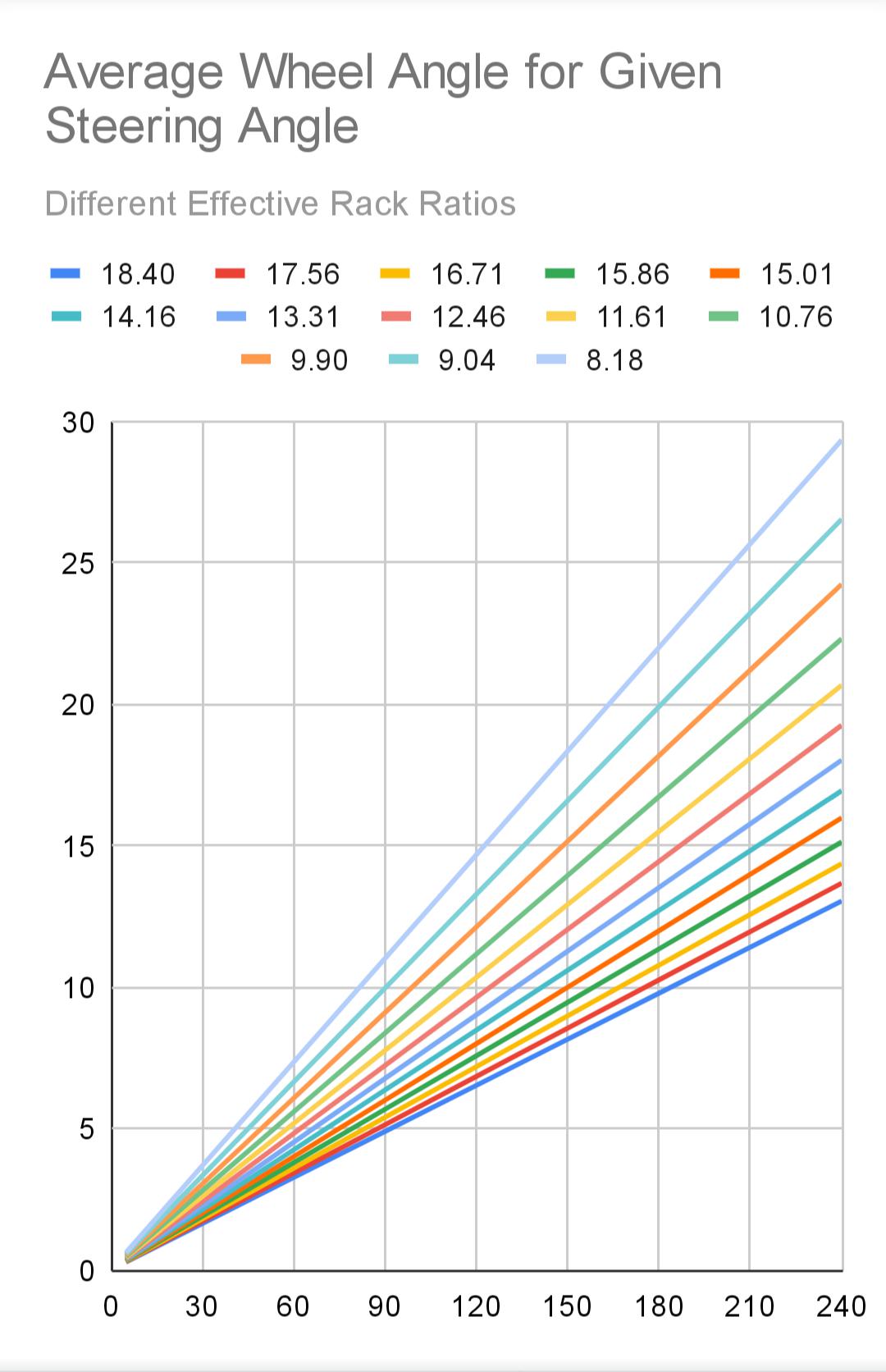
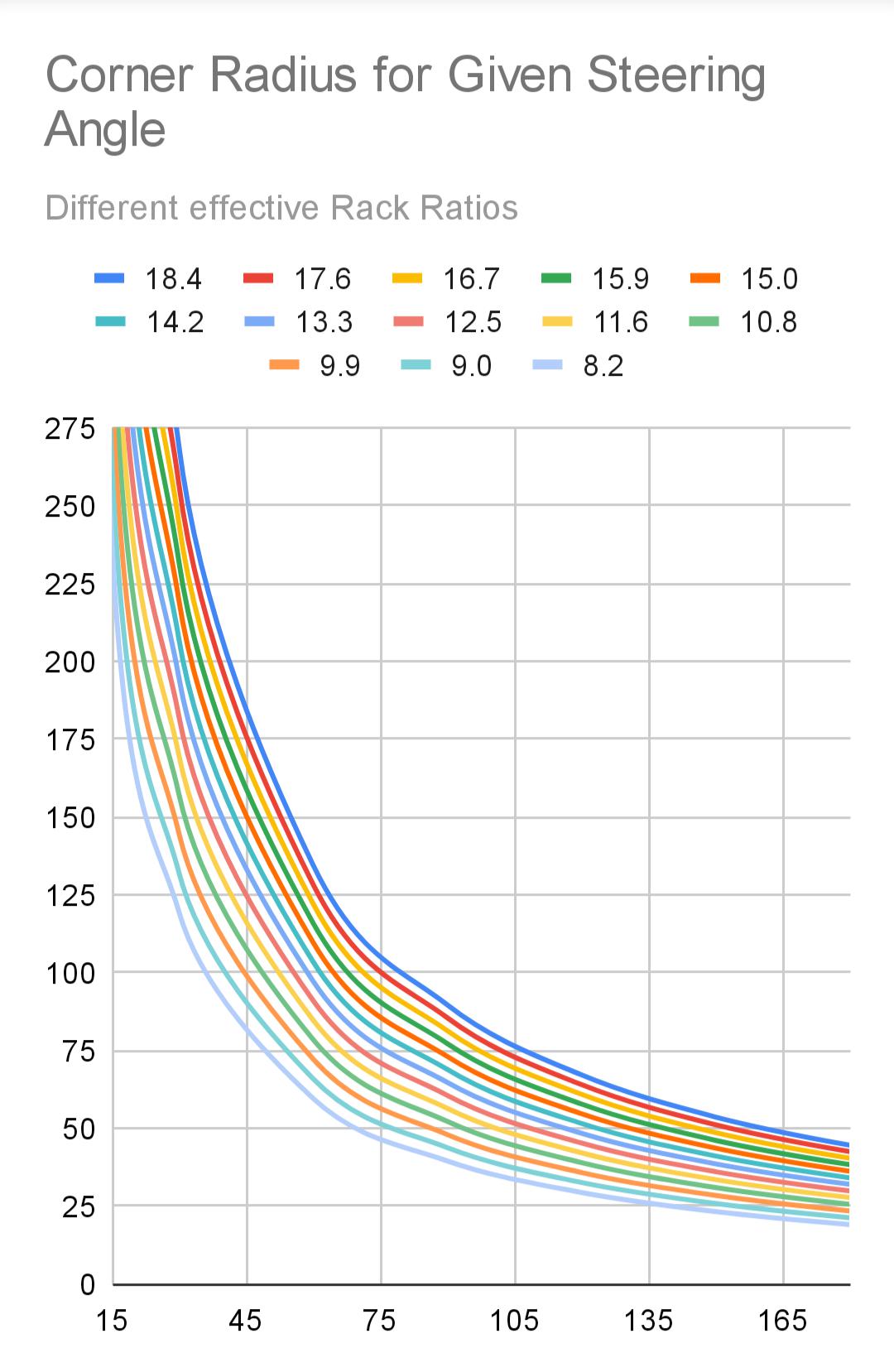
Looking at the internet it seems steering ratios typical for go-karts are 1:1, Formula cars are 6-10:1, Sports cars are 10-14:1.
Corner radius for road course use looks like typically 75'+, road use you may need 30-40'+ for actual road navigation, Autox/Parking lot manuvers 22-25'.
It looks like most production vehicles top out with ~30* of steering and I will probably limit this to around 28 just to keep the steering from being able to rotate more then about 270* off center turn which would be 1.5 turns L2L. The MG is 2 turns L2L but goes to about the same ~30* as if is 11:1.
Bit more progress. Got the top plates on and came up with a design for the tie ins.
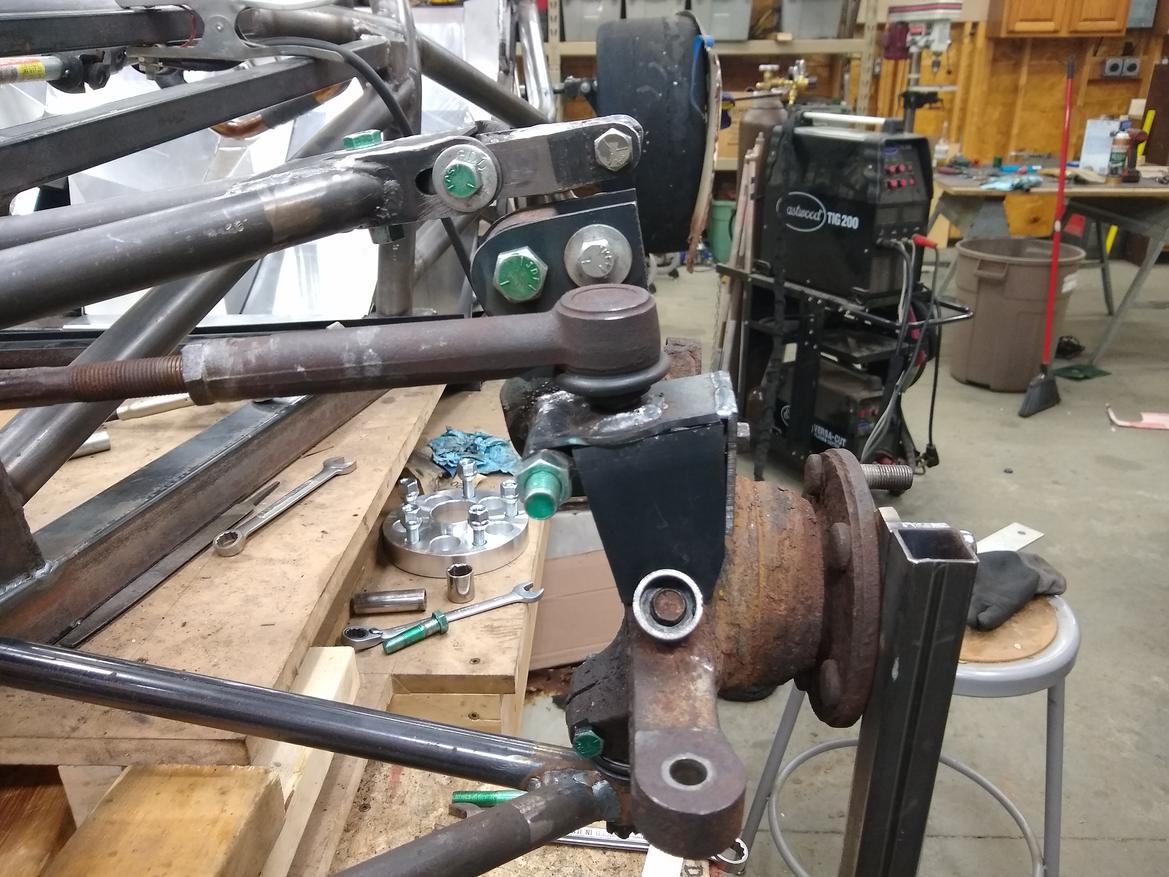
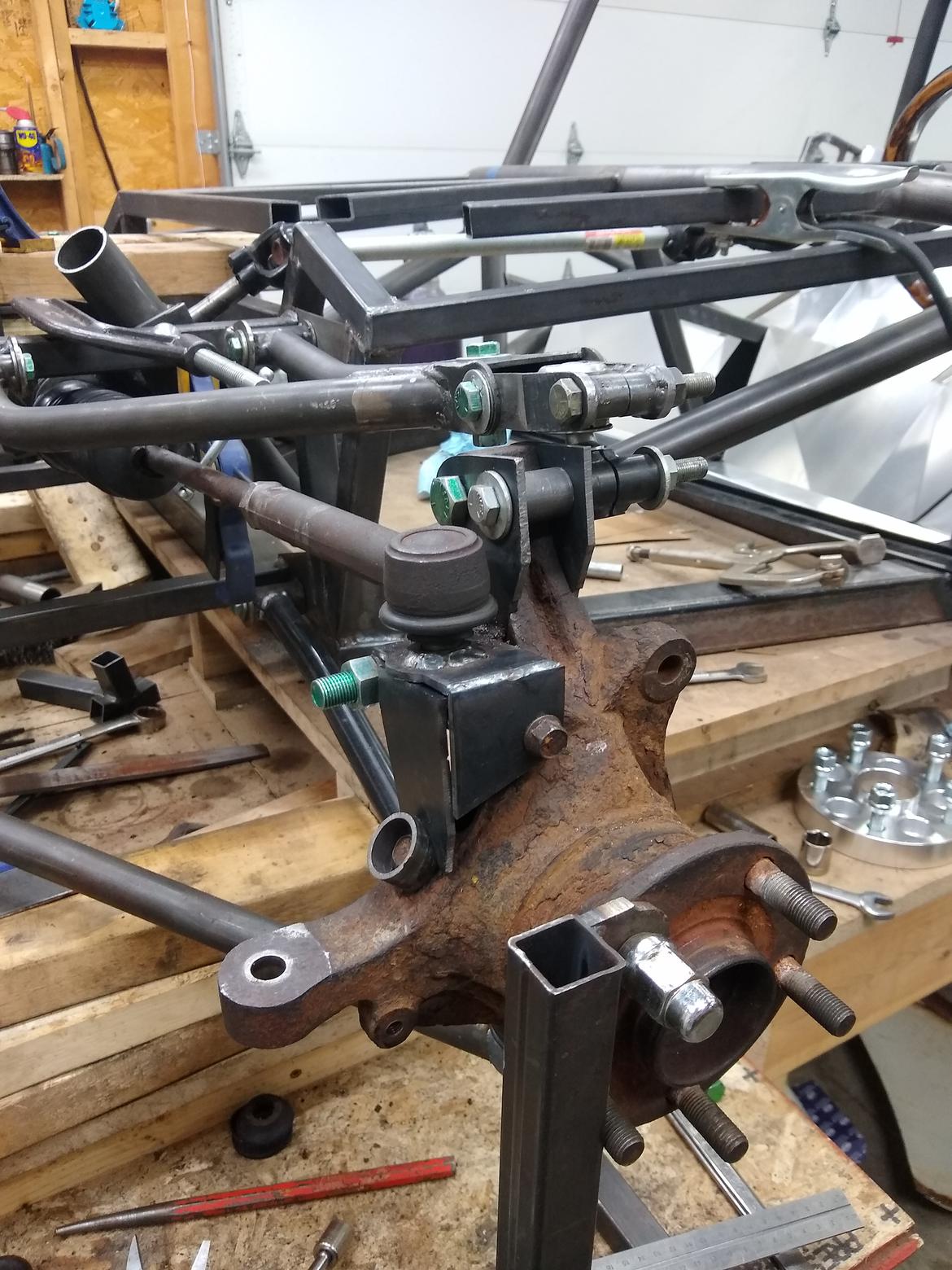
I will likely cut off the stock steering arms eventually when I clean up the uprights. The only thing left for the uprights is to weld the upper ball joint adapter on and add a small reinforcement triangle bellow it.
the engineering being done is amazing both for its furious pace, and for its justification for your build decisions.
I see your angles and turning radius, and raise you a query on steering effort. This pickup location on the knuckle appears to have quite a short lever with which to act. Is this a manual setup, or are you adding power assist?
In reply to gumby :
It is short. The overall ratios is about 7% higher then the MG which is driveable but firm. The 360 will have lower front weight, slightly higher offset but also lower mechanical trail. We will see if it is a steering ratio of regret. I wish I knew a way to accurately estimate actual steering effort.
I know it isn't going to be simple to turn. If it's to much I will look at extending the arms or adding power steering.
The rack is powered... I could look at running lines from the engine or a electric pump...
mke
Dork
5/11/21 5:32 p.m.
In reply to nocones :
stronger, lighter, better. well done!
If you are going to run a power rack without assist, I definitely recommend fully de-powering it which will preclude the possibility of adding hydraulic assist at a later date.
Doesn't mean you couldn't add an EPAS unit to the column if you decide you want the assist, like all the cool kids. 
In reply to gumby :
That's a good point about full depower and I will for the rack that ends up in the car.
I may have just bought a second Subaru Outback 5 speed Car today for $200 that will give the LMP360 a 2.5L and give me a second rack to really truly depower. Or at least give options moving forward. I'm kinda wondering what size 12V motor could be rigged to run the stock hydraulic pump. Flow requirements would be reduced relative to stock because the rack only has to move 1.5 turns total.
The options are truly endless when you own a welder..
Meh. I think if the wheel is too hard to turn you aren't going fast enough!
Rigante
New Reader
5/12/21 3:45 a.m.
there are lots of cars with electric power steering pumps. Not sure what you have locally,
But, pretty sure BMW minis, Mercedes A class, PSA [citroen, peugeot] all have fairly self contained electric pump/ reservoir units. However, it should be ok in this application, but don't seem to be up to powering heavier cars with fat tyres.
Quick google shows Jeep grand cherokee have electric pumps, so that should be up to this application
Here's a Jeep one on EBAY