Helping a friend build a 7.3 powerstroke for his ambulance/camper conversion. He bought some Felpro head bolts for the build, the engine has single use bolts for the heads.
We were going through the torque sequence and one of the bolts broke on the final step to 95ftlbs. The threads were chased, bolts were dipped in oil before installing.
I have drilled a pretty accurate centered hole and have good bite with an easy out, but no movement. I tried some heat with a propane torch on the side of the block with no luck and then busted out the acetylene torch and tried the side of the block a little and the bolt itself a little.
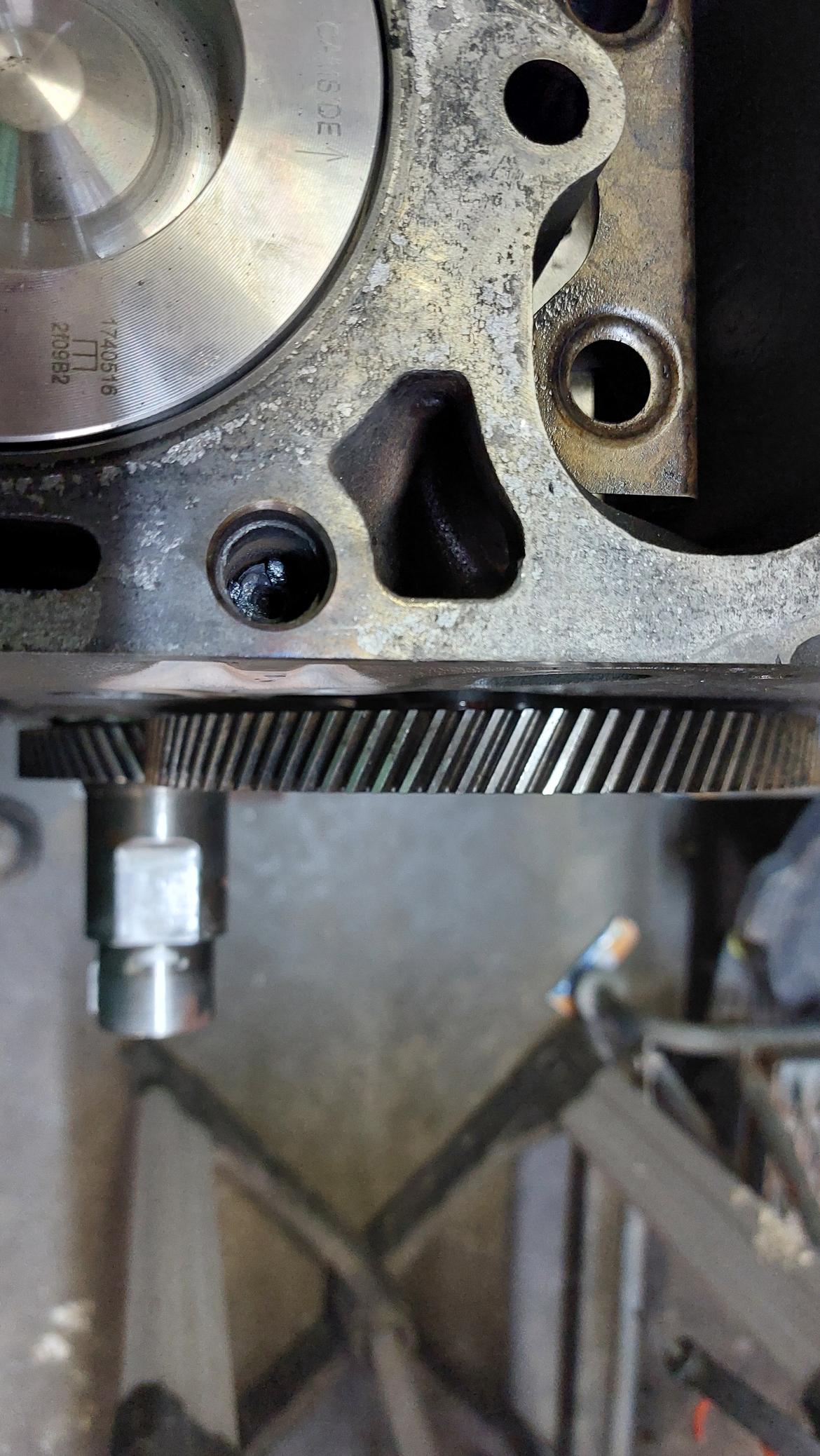
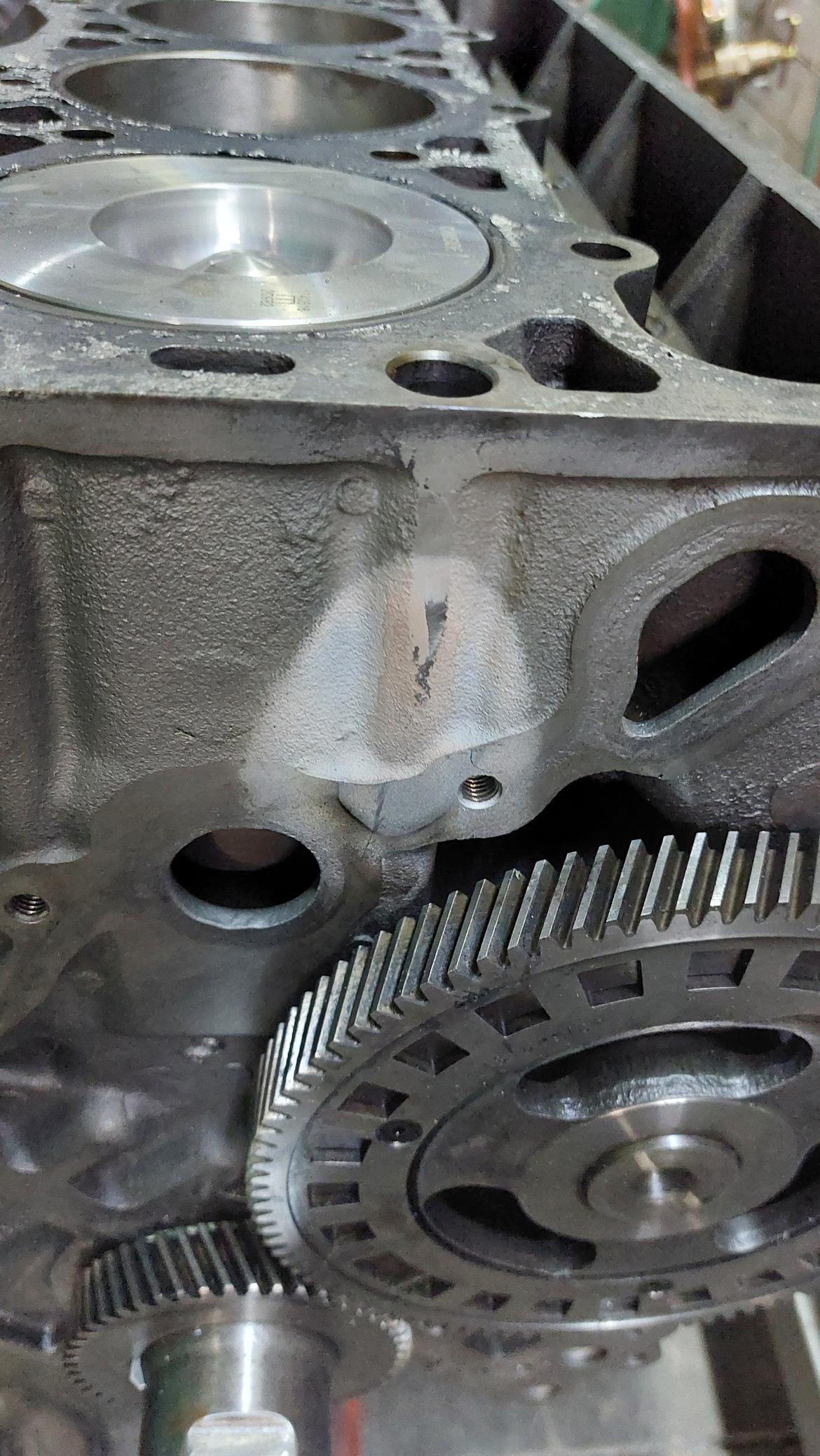
What say the collective? More heat on the block? More heat on the bolt? Both? One then the other? How hot can I get the block before it is a problem?
I warned him the worst case scenario is we empty the block of rotating stuff and take it to the machine shop. I just don't want to add a broken easy out stuck in the bolt to the mix.
IME heat is used to break loose rust/corrosion. You don't seem to have that issue. Post a pic of the end of the bolt that came out.
I can get one tonight. It broke about 6 turns from the end of the threads but at the start of the threads in the block.
My thought on using heat was to loosen the grip the block has with expansion. The next thought when that did nothing was to try to take the bolt down a few grades from 10.9 hoping that would help it lose some of the tension that is in the threads right now.
Well, just got to the shop and tried one last time with everything cooled off. Gave it a twist and heard a crack! Thought it was the easy out until a tried to pull it out. I shined a light in the hole as I turned it and saw the bolt was spinning!
Gonna buy a lottery ticket on the way home in case I still got some luck in me
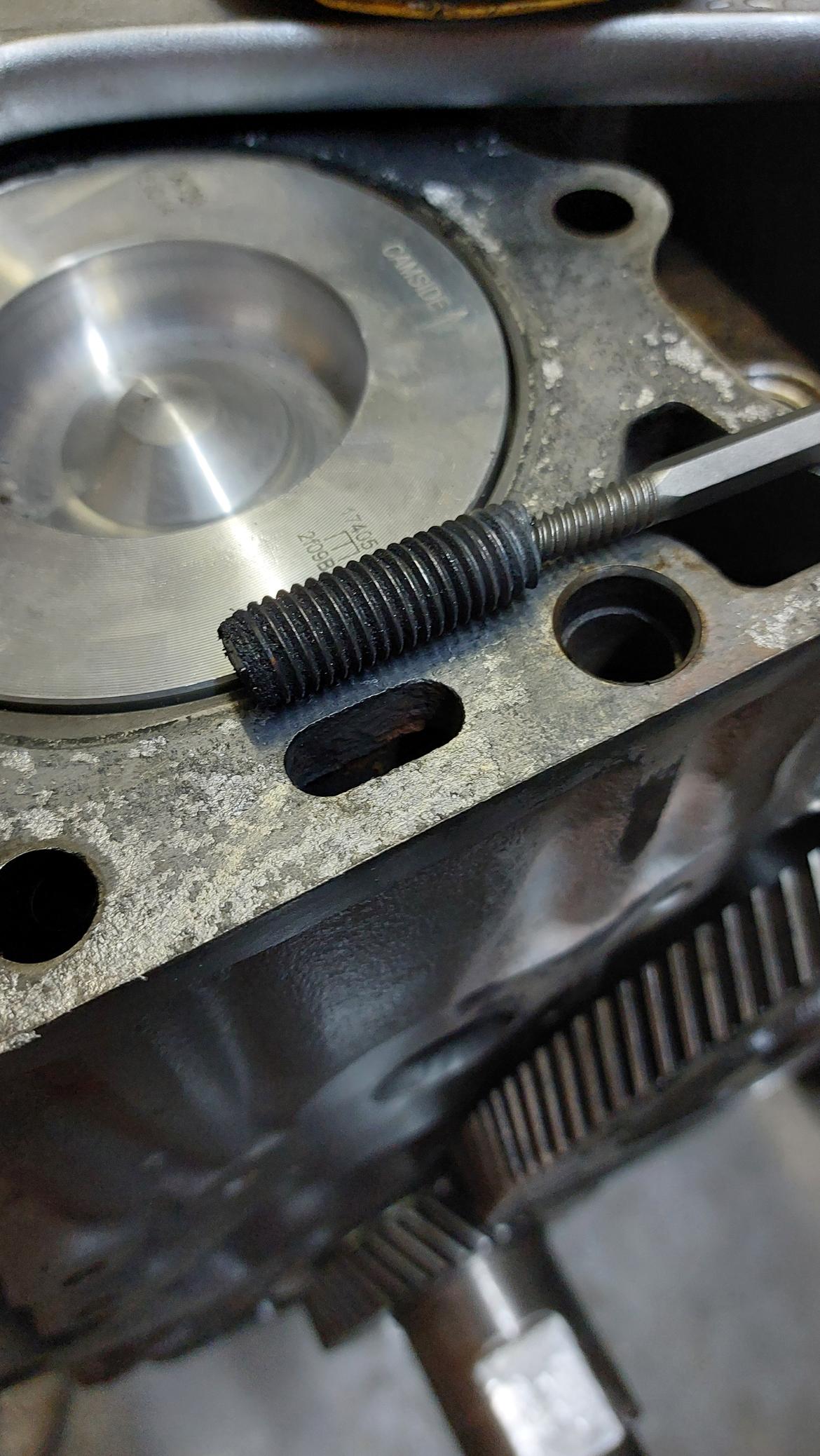
I'd look really hard at the length of the bolt, and if they are correct, I'd chase the threads. That really should not have happened, and if it was just a crap bolt, it should have spun out with no issues. It was bottomed in the hole, or jammed in a bad thread.
I've removed head bolts that have broken 200,000km into the life of the vehicle with almost no effort.
I think it was a crap bolt. They are all the same length and every hole was chased to the bottom. I even took my torque wrench to my snap on guy and had him test it.
Im guessing the torque to yield design caused the slight jam in the threads near the break.
We have a fresh set of Mahle bolts to go back in. I'm happy it is only going to cost a set of bolts and head gaskets.
Also glad we weren't working on it in the vehicle.
It did cost me a fingernail on my right ring finger, the torque wrench bashed it against the head when the bolt broke.
Quite a bit of stretch with the broken one. 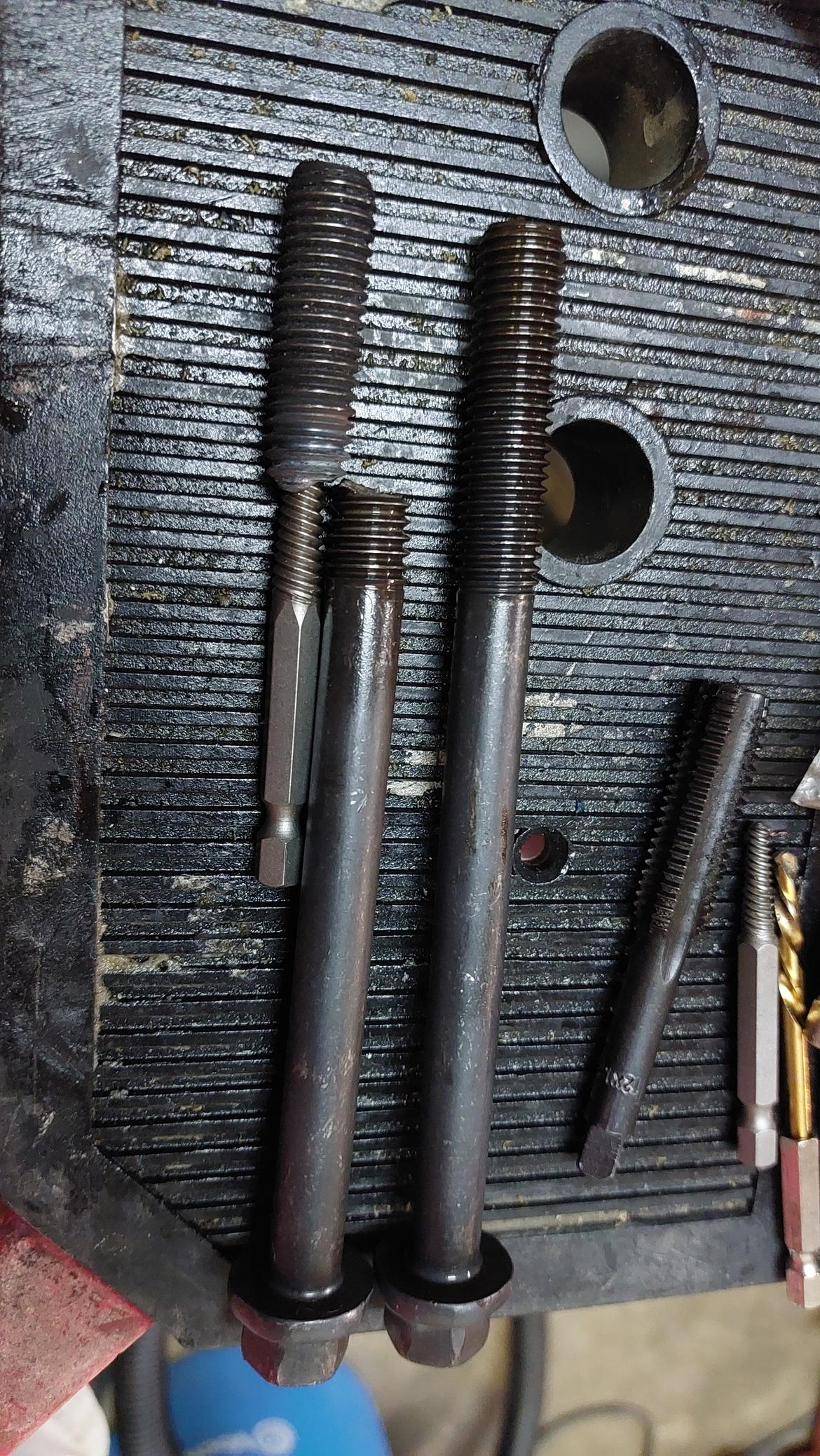
NOHOME
MegaDork
8/30/24 9:41 p.m.
In reply to jgrewe :
We were going through the torque sequence and one of the bolts broke on the final step to 95ftlbs. The threads were chased, bolts were dipped in oil before installing.
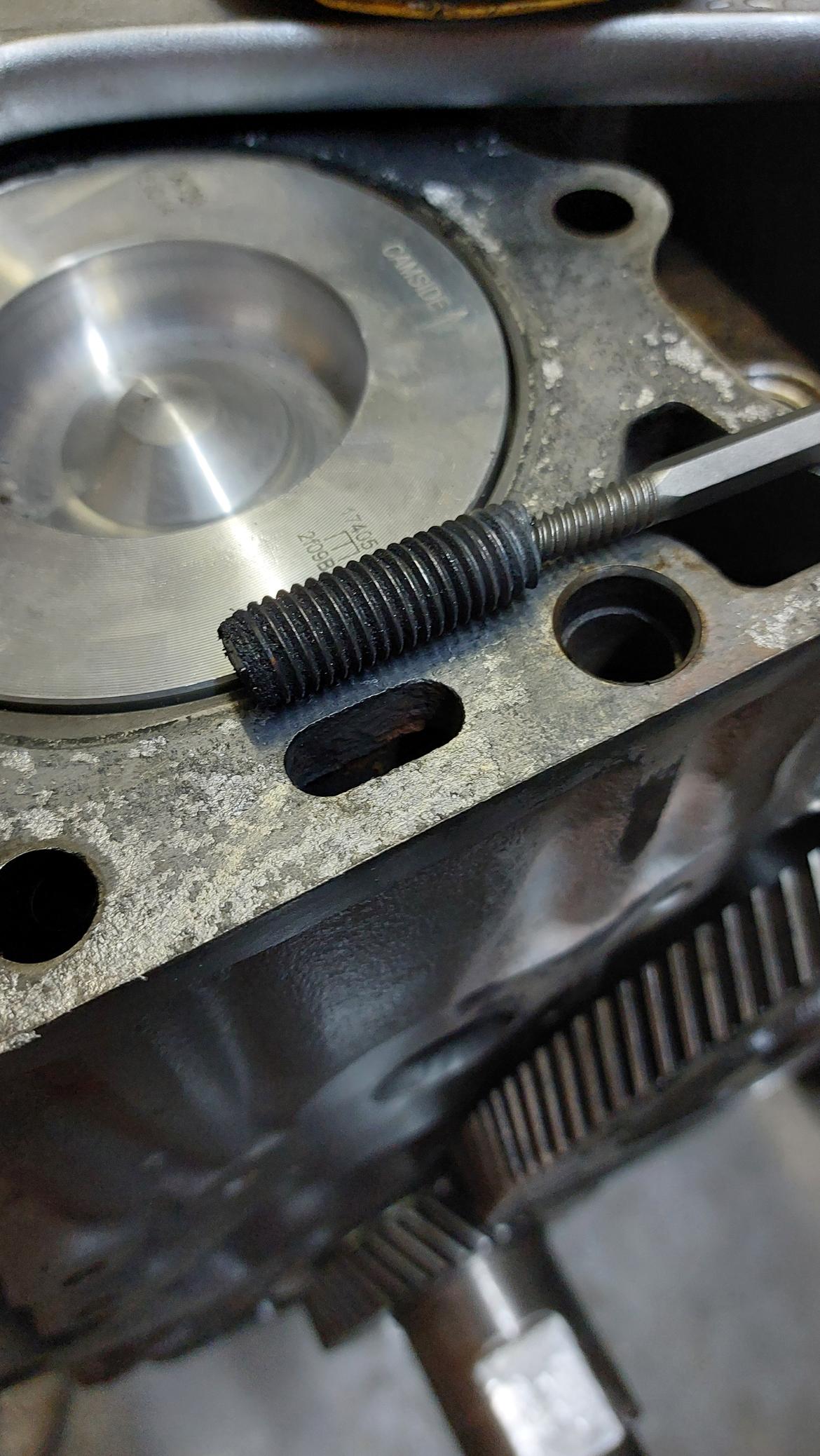
You mention that the threads were chased. Based on the amount of crud I see on the bolt, the holes were never flushed after the tap was run. The bottom of the threaded hole might have had enough material for the bolt to bottom out. While that alone should not have broken the bolt, as far as the other head bolts, it might have given you a click on the torque wrench while not providing the proper clamp force. I would not trust any of the torque readings on any of the holes until the block was flipped over and the threaded holes given a good clean with brake clean usisng the red straw that comes with the can.
The oil on the threads might also be a problem if there was enough to create a hydraulic lock at the bottom of the bolt-hole. It might be that the bottom of the hole was full of oil and the crud was enough to create a seal that kept the bolt from going all the way in. Again, not that it should have caused the bolt to brake as you did not exceed the torque spec.
That sure doesn't look like 95 pound feet.
In reply to NOHOME :
Your first statement nailed it. My first thought was "that hole is just a tiny bit shallower than the rest, but I like your thought better. Might be a bit of both (combined with a bad bolt!)
I like where you went as you continued as well. Excellent instructions 
jgrewe
Dork
8/30/24 10:23 p.m.
All good things to double check. I chased with grease on the tap and cleaned it often. We blew the holes out and were careful about the amount of oil on the threads.
The grit you are seeing is most likely from the drill process to give the easy out a hole to grab. It was tough to get a nice cut going with the reverse drill bit on the 10.9 bolt. Things got a little crispy as I was putting heat into the bolt yesterday too.
My first thought was the torque wrench to be honest. I left it as it was set and it was within a pound at 95 when I had it tested the next day. We ran it up to 140 and got a similar result, within a pound.
No Time
UberDork
8/30/24 10:43 p.m.
I'd clean the hole, thread a bolt all the way in by hand until it bottoms out, mark it (painter tape or sharpie), then put it through the hole in the head to see where the mark is relative to the bottom of the head.
Then do the same with one of the holes where a bolt didn't break, and the hole it went through in the head to see if there's a difference.
I'd also read the assembly instructions to see if oiling the bolt threads is appropriate in this application. It is my understanding that fasteners are to be installed and torqued dry unless specifically instructed otherwise.
torque is just a convenient way to "measure" clamp load, but the measurement is way off if the thread is oiled when the spec calls for dry, or Vice versa.
jgrewe
Dork
8/30/24 11:22 p.m.
Instructions called for oil. They got a dip then a drag across a microfiber cloth to remove the excess.
Successfully removing a broken bolt is very satisfying. 
It definitely torque fractured and stretched. Definitely has/had garbage in the threads.
In reply to stuart in mn :
Yes.
Had to remove the outer race of a ball bearing that had failed, the race was pressed into a pocket in the end of a shaft, no way to get at the backside of it. Since the race was hardened, I hoped I could crack it by using a hammer and punch, if it would crack or shatter it would release the tension holding it into the pocket an allow me to pull it out. Well, that didn't work, but it did mushroom the end of the punch I was using. I realized that the mushroomed head of the punch would fit into the recessed groove of the race and allow it to grab it pretty well, so, I ended up using the punch as a lever - turned it around, stuck the head of the punch into the bearing race groove, held it in there tightly, and worked my around it using the hammer to firmly tap on the tapered end of the punch. It took awhile, but I could finally feel (and hear) it start to give. Couple more taps, and out it came.
Whew.